Innovations and Challenges in Chemical Manufacturing
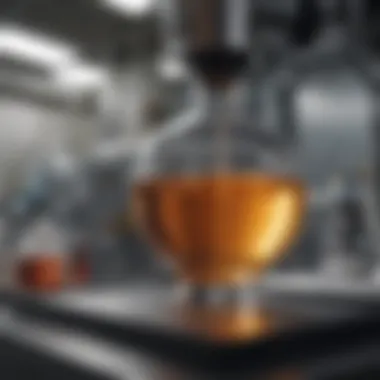
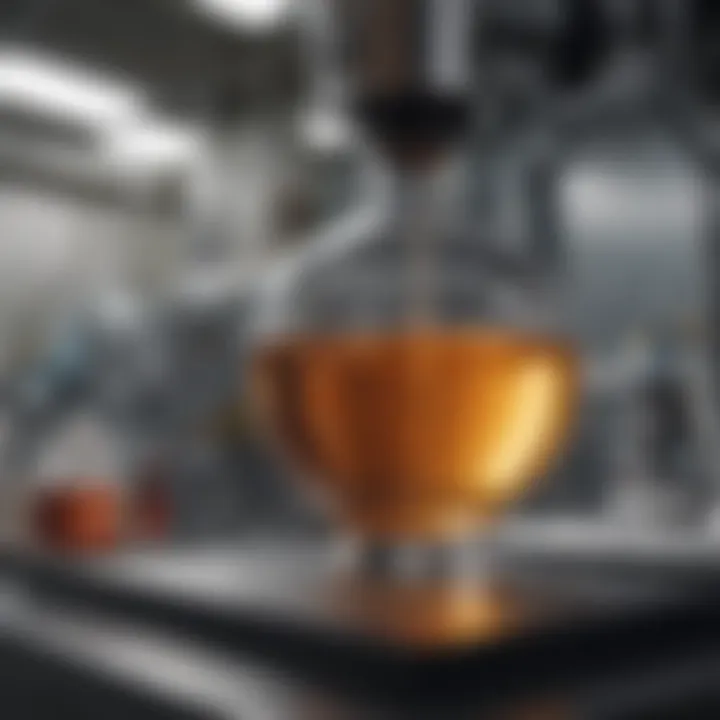
Intro
Chemical manufacturing plays a vital role in modern society, influencing a broad spectrum of industries from agriculture to pharmaceuticals. Understanding the landscape of chemical manufacturing, its innovations, challenges, and future directions is crucial for stakeholders in various fields. As we delve into this topic, we will highlight significant findings, examine historical context, and identify emerging trends that shape the future of this sector.
The significance of chemical manufacturing cannot be overstated. It impacts daily life, from the availability of essential consumer products to advancements in medical science. Therefore, comprehending the dynamics of this industry is essential for students, researchers, and professionals alike. By recognizing the advancements in technology and the pressing challenges faced, one can better appreciate the future directions and sustainable practices that are becoming increasingly relevant.
This article aims to provide a thorough analysis of the various facets of chemical manufacturing, addressing everything from safety protocols to regulatory frameworks. It will also explore the implications of these factors on the economy and the environment.
Engaging with this content will equip readers with a well-rounded understanding of the intricacies involved in manufacturing chemicals, allowing them to grasp the complexities that define the industry today.
Overview of Chemical Manufacturing
Chemical manufacturing plays a crucial role in the modern economy, providing the foundational materials that support a wide range of industries. It involves the production of chemicals through various processes that convert raw materials into valuable products. Understanding this field's scope is essential not only for those within the industry but also for policymakers and consumers who rely on it.
Definition and Scope
Chemical manufacturing refers to the processes involved in the production of chemicals and chemical products. This includes the formulation, mixing, and processing of substances. The scope of chemical manufacturing is extensive, covering everything from basic substances like acids and bases to intricate formulations such as pharmaceuticals, agrochemicals, and specialty chemicals. Manufacturers employ diverse methods, including batch processing, continuous processing, and specialty techniques tailored for specific products.
The industry is a critical link in the supply chain that supports other sectors, including agriculture, energy, and technology. Innovations in chemical manufacturing have led to more efficient processes, increased yields, and the development of greener alternatives.
Importance in Various Industries
Chemical manufacturing is not an isolated field. Its importance stretches across multiple sectors, all of which depend on various chemical products. Some key industries influenced by chemical manufacturing include:
- Pharmaceuticals: The production of Active Pharmaceutical Ingredients (APIs) essential for medications relies heavily on chemical manufacturing processes.
- Agriculture: Agrochemicals, including fertilizers and pesticides, originate from chemical manufacturing, enhancing food production and crop yield.
- Energy: The production of biofuels and other chemical energy sources is integral to transitioning toward sustainable energy solutions.
- Consumer Goods: Everyday products such as detergents, cosmetics, and plastics are all derived from chemical manufacturing processes.
The industry's adaptability to trends, such as sustainability and technological advancements, shapes its future. Innovation within chemical manufacturing is not just about efficiency; it also addresses environmental concerns and societal needs. As such, a thorough understanding of this field is indispensable for those looking to engage with the complexities of modern manufacturing and its implications on daily life.
Historical Development
The historical development of chemical manufacturing is a crucial aspect that provides insight into how contemporary practices and methodologies have evolved. Understanding these historical contexts enriches our comprehension of modern innovations in the field. The industry has undergone significant changes due to advancing science, technology, and changing societal needs. These elements have collectively shaped the landscape of chemical manufacturing today.
Early Chemical Production
Early chemical production can be traced back to ancient civilizations. The use of substances like alkalis, acids, and salts in various applications marks the beginning of chemistry as a practical science. Early chemistry was more an art than a science; it was characterized by trial and error. Ancient Egyptians produced dyes and perfumes from natural resources, while the Chinese are known for creating gunpowder in the 9th century.
Moreover, the Greeks laid the philosophical groundwork for chemical thought. The concept of the four elements—earth, water, air, and fire—originated from this period. However, it was not until the Middle Ages that alchemy emerged, focusing on the transmutation of base materials into gold and the quest for the philosopher's stone. This mystical approach eventually paved the way for modern chemistry.
The transition from alchemy to chemistry happened rapidly during the Enlightenment period. Discoveries of new elements and compounds, along with the formulation of early chemical laws by scientists such as Antoine Lavoisier, shifted the focus towards understanding matter more scientifically. Lavoisier, for instance, is often referred to as the father of modern chemistry for establishing the law of conservation of mass. This era laid the foundational knowledge crucial for future advancements in chemical manufacturing.
Industrial Revolution and Chemical Manufacturing
The Industrial Revolution marked a pivotal moment in the history of chemical manufacturing. It was during the late 18th and the early 19th century that the industrial production of chemicals emerged on a larger scale. Prior to this period, chemical production was localized and less efficient.
The advent of steam power and mechanization led to the mass production of chemicals such as sulfuric acid, a vital compound in various applications, including fertilizers, explosives, and synthetic materials. The establishment of large-scale chemical factories, particularly in Europe and the United States, initiated new opportunities and challenges within the industry. The introduction of specialized equipment and methods allowed for increased efficiency and output.
As the need for new chemical products grew, so did the development of synthetic organic chemistry. Innovations in dye production, specifically the synthesis of synthetic dyes, revolutionized textile manufacturing. This period also saw the birth of pharmaceuticals, with the production of compounds like aspirin coming to fruition around the late 19th century.
The impacts of the Industrial Revolution are still visible today. It set the stage for the globalization of chemical production, establishing a framework that influences production processes and regulatory aspects. Additionally, it raised challenges related to environmental sustainability and worker safety, issues that the industry continues to grapple with today.
Current Manufacturing Processes
Current manufacturing processes in the chemical industry are crucial for driving efficiency, scalability, and innovation. These processes not only determine how products are made but also impact costs, environmental sustainability, and quality. Chemical manufacturing today relies on various strategies to optimize production and enhance product development. Understanding these processes allows industry professionals to make informed decisions that align with both economic and environmental goals.
Batch vs. Continuous Processing
Batch processing and continuous processing represent two fundamental approaches in chemical manufacturing.
- Batch Processing: This method involves producing a specified quantity of product in discrete batches. Each batch goes through the entire manufacturing process before the next one begins. It is widely used for products requiring precise control and customization. Examples include pharmaceuticals and specialty chemicals. The flexibility of batch processing allows manufacturers to adapt to changing demands but may result in higher production times and costs.
- Continuous Processing: In stark contrast, continuous processing entails a constant flow of raw materials through the production process. This method is ideal for high-volume production where standardization is key. It maximizes efficiency, reduces waste, and can lead to lower operational costs. However, it generally involves a higher initial investment and can be less adaptable to changes in product specifications.
Each method has its advantages and disadvantages, and the choice often depends on the specific needs of the product and market conditions.
Key Production Techniques
Several key production techniques significantly influence the chemical manufacturing landscape today:
- Reactor Design: Efficient reactor design is critical for maximizing yield and minimizing energy consumption. Various types of reactors, such as batch, plug flow, and stirred-tank reactors, serve different process needs.
- Separation Techniques: Techniques like distillation, filtration, and chromatography are essential for isolating and purifying chemical products. Advances in separation technologies improve product purity and recovery rates.
- Heat Exchange: Effective heat exchange systems enhance process efficiency. They help in capturing and reusing heat, thereby reducing energy consumption and lowering production costs.
These techniques epitomize the blend of science and engineering that drives chemical manufacturing forward. Continuous improvement in these areas enhances productivity and ensures a more sustainable approach to production.
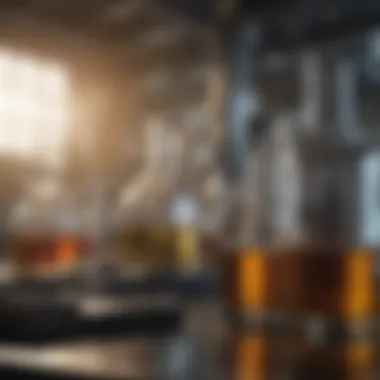
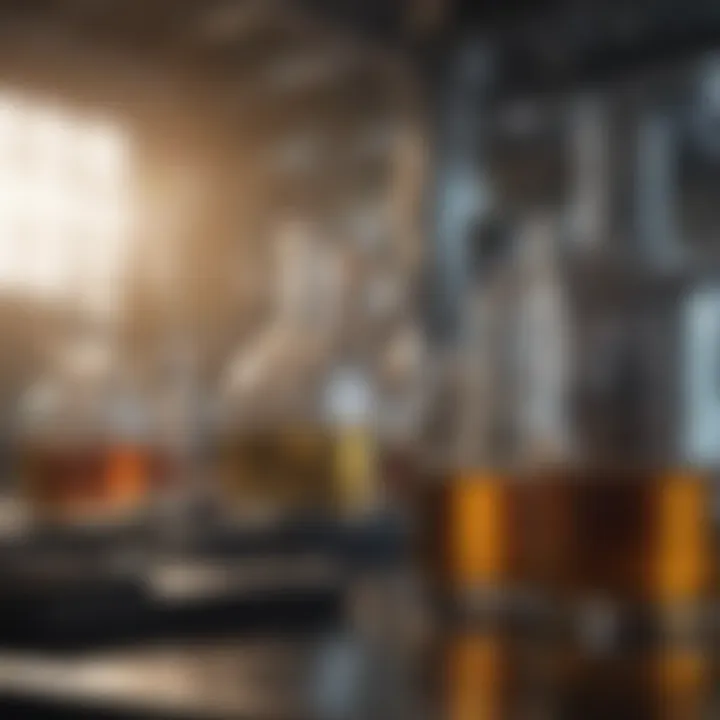
Automation and Robotics in Manufacturing
Automation and robotics are transforming the chemical manufacturing sector. The integration of automated systems streamlines operations, increases accuracy, and minimizes human error. Here are some notable aspects:
- Increased Efficiency: Automated systems can operate continuously with minimal downtime. This allows for round-the-clock production without the fatigue that human operators might experience.
- Enhanced Safety: Robots can perform dangerous tasks, such as handling toxic materials, reducing the risk of accidents in the workplace. This is particularly important in environments where hazardous chemicals are present.
- Data Integration and Analysis: Automation facilitates real-time data collection and monitoring, enabling manufacturers to optimize processes based on precise analytics. This data-driven approach allows for quicker responses to production challenges.
Adopting automation and robotics not only enhances productivity but also positions manufacturers to address the growing demands for safer and more sustainable production practices.
"The future of chemical manufacturing lies in embracing technology that enhances both efficiency and safety. Automation is not just an option; it is essential for competitiveness in the market today."
In summary, current manufacturing processes are diverse and multifaceted, playing a vital role in shaping the chemical industry. Understanding the intricacies of batch versus continuous processing, the key production techniques, and the impact of automation allows stakeholders to navigate the complexities of modern chemical manufacturing effectively.
Technological Innovations
Technological innovations play a crucial role in the advancement of chemical manufacturing. They not only enhance efficiency and productivity but also help to address pressing environmental concerns. As industries seek to optimize their operations, innovations in technology become essential in driving change. In this section, we will explore some key advancements in catalysis and process intensification techniques that are reshaping the landscape of chemical manufacturing.
Advancements in Catalysis
Catalysis significantly influences the effectiveness of manufacturing processes. The advancement in catalytic technologies leads to faster reactions and reduced energy consumption. This area has seen considerable progress with the development of new materials and methods.
Several types of catalysts, including heterogeneous and homogeneous ones, offer various benefits. For example, heterogeneous catalysts can easily be separated from the reaction mixture, which reduces production costs and time. On the other hand, homogeneous catalysts can provide higher selectivity, resulting in fewer by-products. The fusion of nanotechnology with catalysis has also proven beneficial, as it enhances the surface area and reactivity of catalysts.
Moreover, new strategies involving biocatalysis, where enzymes are used to speed up reactions, present opportunities for more sustainable production. By utilizing enzymes derived from biological sources, manufacturers can conduct reactions under milder conditions, which reduces energy requirements and resource consumption.
"Innovations in catalysis not only increase efficiency but also make chemical processes more sustainable."
Process Intensification Techniques
Process intensification refers to the methodologies that aim to enhance the productivity and efficiency of chemical processes. This approach seeks to modify existing processes to achieve significant improvements in resource utilization while minimizing waste.
Common techniques include microreactor technology and continuous flow systems. Microreactors allow for precise control of reaction conditions, leading to safer and more efficient chemical processing. They can handle reactions at a smaller scale while maintaining high reaction rates.
Continuous flow systems, in contrast to traditional batch processing, ensure a constant flow of reactants through the system. This leads to shorter reaction times and improved heat and mass transfer. The adoption of such techniques contributes to less energy use and more consistent product quality.
Furthermore, the integration of automation and real-time monitoring in process systems allows manufacturers to respond quickly to any deviation from ideal conditions, enhancing overall process control. Overall, process intensification systematically optimizes chemical production, aligning with the industry's focus on efficiency and sustainability.
Environmental Impact and Sustainability
Environmental impact and sustainability are crucial components in the discussion of modern chemical manufacturing. As industries face increasing scrutiny from both regulatory bodies and the public, the focus on reducing environmental footprints is paramount. It is not just about adhering to laws; it is about fostering corporate responsibility and being proactive in environmental stewardship.
Incorporating sustainable practices into chemical manufacturing can yield significant benefits. Companies that prioritize sustainability can reduce waste, lower energy consumption, and improve their overall efficiency. This not only enhances profitability but also ensures compliance with stringent environmental regulations.
Chemical Waste Management
Chemical waste management involves the careful handling, treatment, and disposal of waste generated during manufacturing processes. The generation of hazardous waste is a serious concern in the industry, which makes effective waste management practices necessary. Proper disposal techniques can include recycling, treatment, and safe disposal methods designed to minimize risks to the environment and human health.
One such method is the adoption of closed-loop systems that recycle materials within the manufacturing process. This approach reduces the need for raw materials and minimizes waste, aligning with sustainability goals.
Key strategies in chemical waste management include:
- Identification of waste sources: Understanding where and why waste is generated during production helps in developing mitigation strategies.
- Treatment technologies: Investing in advanced waste treatment technologies can effectively neutralize hazardous compounds, reducing their impact.
- Regulatory compliance: Ensuring that waste management practices meet local and international regulations is essential for the industry’s sustainability.
Implementing these strategies can lead to a significant decrease in environmental pollution and enhance the overall sustainability of chemical manufacturing practices.
Green Chemistry Principles
Green chemistry principles focus on designing chemical processes and products that minimize hazardous substances. These principles prioritize sustainability by encouraging the reduction and elimination of waste, not just at the end of the manufacturing cycle, but from the outset. Adopting green chemistry can lead to safer and more efficient processes.
The twelve principles of green chemistry emphasize the respect for human health and the environment, and include:
- Prevention of waste: Design processes to minimize waste.
- Atom economy: Maximize the incorporation of all materials used in the process into the final product.
- Less hazardous chemical syntheses: Plan synthetic methods to use and generate substances that possess little or no toxicity to human health and the environment.
- Design for energy efficiency: Run chemical processes at ambient temperature and pressure whenever possible.
- Use of renewable feedstocks: Use raw materials derived from renewable sources rather than depleting ones.
By aligning with these principles, the chemical manufacturing sector can innovate while reducing its ecological footprint.
"The shift towards sustainable practices in chemical manufacturing is not just a trend, but a necessity for future viability."
In summary, focusing on environmental impact and sustainability sets the stage for long-term success in chemical manufacturing. It encourages innovation, promotes compliance, and safeguards human health and ecosystems.
Regulatory Framework
The regulatory framework surrounding chemical manufacturing is essential for ensuring safety, environmental protection, and industry integrity. As the chemical industry impacts both the economy and the environment, adhering to the regulatory standards is crucial for manufacturers. Regulations guide the processes from production to disposal, influencing how chemicals are developed and used. Such frameworks aim to minimize risks associated with chemical production while maximizing safety for workers and communities.
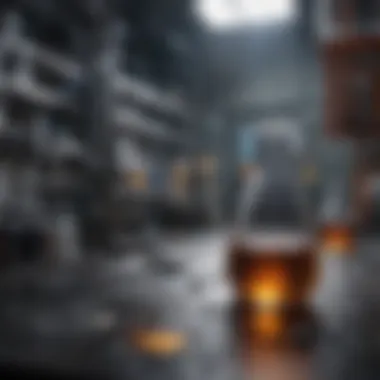
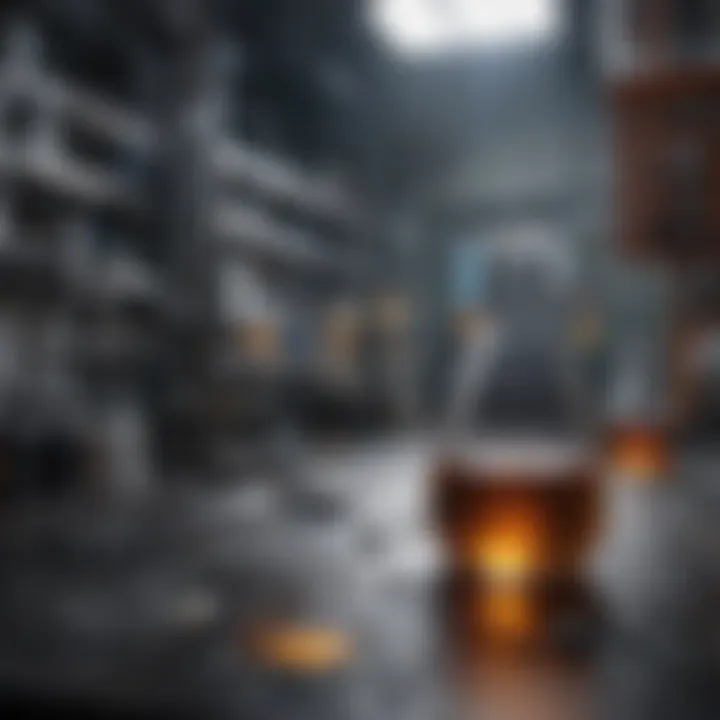
Multiple regulatory bodies exist globally, each imposing its own set of standards. These standards can influence everything from plant operations to product formulation. By following these regulations, manufacturers can demonstrate their commitment to environmental stewardship and ethical practices.
Understanding the regulatory landscape allows businesses to avoid legal pitfalls and fosters innovation in safer processes. The significance is twofold: protecting public health and enhancing economic competitiveness.
Global Regulations and Standards
Chemical manufacturing is governed by an array of global regulations and standards. These rules vary by region but are primarily designed to ensure safety and environmental sustainability. In the United States, the Environmental Protection Agency (EPA) enforces regulations like the Toxic Substances Control Act (TSCA), which governs the introduction of new or already existing chemicals. In the European Union, the Registration, Evaluation, Authorisation and Restriction of Chemicals (REACH) regulation plays a pivotal role, requiring extensive testing and documentation for chemical substances.
Some key aspects of global regulations include:
- Safety Protocols: Regulations mandate safety measures to protect workers and local communities.
- Environmental Impact Assessments: Many countries require manufacturers to conduct assessments to gauge the potential ecological footprint of chemical plants.
- Compliance Reporting: Companies must frequently report their adherence to the established guidelines. Non-compliance can result in severe penalties, including fines and shutdowns.
These regulations serve to build consumer trust and ensure that chemical manufacturers operate within clearly defined ethical boundaries.
Compliance Challenges for Manufacturers
Navigating the complex landscape of regulatory compliance presents numerous challenges for chemical manufacturers. First, the inconsistency of regulations between jurisdictions can lead to confusion. A product approved in one country may face restrictions in another, making international operations complicated.
Cost implications also play a significant role. Compliance often requires investment in specialized training, auditing, and reporting. New regulations can necessitate changes to manufacturing processes, leading to unexpected financial burdens.
Moreover, many manufacturers struggle to keep up with the ever-evolving regulatory environment. Changes in policies can occur rapidly, making it difficult for companies to adapt without incurring penalties. This fluidity often requires producers to allocate substantial resources to stay informed about the latest regulations.
"Staying compliant in the chemical manufacturing sector is not just about following the law; it is a matter of sustaining the trust of consumers and shareholders alike."
In summary, while the regulatory framework is vital for safe chemical manufacturing, it also presents challenges that require careful management. Understanding and adapting to regulations is critical in maintaining operational integrity and positioning a company for success in the market.
Safety and Risk Management
Ensuring safety in chemical manufacturing is crucial for protecting workers, stakeholders, and the environment. As the industry continues to innovate, it is essential for companies to prioritize effective risk management strategies. This involves regular assessments of potential hazards and the implementation of systematic procedures to mitigate these risks. The goal is to create a safe work environment while maintaining operational efficiency, hence the importance of safety and risk management cannot be overlooked.
Hazard Identification and Analysis
Hazard identification is the first step in a proactive risk management approach. It involves recognizing possible dangers present in the chemical manufacturing process. This could include chemical exposure, equipment failures, or even human errors. Once hazards are identified, a thorough analysis follows to evaluate the level of risk associated with each hazard. This can be done using qualitative and quantitative methods.
- Qualitative Methods: These involve subjective assessments based on expert opinions or historical data on accidents and incidents.
- Quantitative Methods: This approach uses numerical data to estimate the likelihood of an event occurring and its potential impact.
Effective hazard analysis allows manufacturers to prioritize risks based on their potential severity. This aids in the development of appropriate safety protocols. For instance, high-risk factors may require immediate action, such as enhanced training or equipment upgrades.
Emergency Response Procedures
In the realm of chemical manufacturing, emergency response procedures are vital. These plans ensure swift action in case of incidents like spills, fires, or chemical leaks. Having a robust emergency response plan in place minimizes damage and protects lives.
An effective emergency response plan includes:
- Clear Communication Channels: All workers should know who to contact during an emergency. This includes internal and external stakeholders.
- Training and Drills: Regular training ensures that employees are familiar with emergency procedures. Drills should be conducted to practice these procedures regularly.
- Resource Accessibility: Necessary resources, such as safety equipment and first-aid supplies, must be easily accessible. Quick access can make a significant difference during emergencies.
- Documentation: All emergency protocols should be well-documented and made available to all staff.
"Effective risk management in chemical manufacturing not only protects lives but enhances overall operational efficiency."
Overall, safety and risk management in chemical manufacturing is all about developing a culture of safety. This involves proactive hazard identification, thorough analysis, and preparedness for emergencies. Successfully navigating these elements ultimately leads to a safer environment and a more sustainable industry.
Economic Factors Influencing Chemical Manufacturing
Understanding the economic factors that influence chemical manufacturing is crucial for assessing the industry's future and sustainability. These factors can determine how effectively chemical companies can operate, compete, and innovate. Economic influences manifest through a variety of elements, including market demand, globalization, and technological advancements, which all intersect to shape operational strategies and market outcomes.
Global Supply Chain Dynamics
The global supply chain plays a significant role in chemical manufacturing. Today, raw materials are often sourced across different geographies, where costs and availability can vary dramatically. Raw materials such as petrochemicals, polymers, and specialty chemicals derive from diverse geographical locations.
- Cost Variability: Fluctuations in raw material prices can directly impact production costs. For example, disruptions in geopolitical stability can lead to supply shortages or price hikes.
- Transport and Logistics: Efficient transportation strategies are vital. Companies need to evaluate shipping costs and logistics efficiency to minimize expenses and ensure timely production.
- Local Regulations: Import tariffs and trade policies can also affect the costs associated with sourcing materials internationally. Understanding these regulations helps manufacturers optimize their supply chain for cost-effectiveness.
- Sustainability Concerns: There's an increasing demand for sustainable practices in supply chains. Manufacturers are now tasked with integrating environmentally responsible sourcing practices into their operations.
Entering new markets requires comprehensive strategies that consider local supply chain conditions and potential partnerships.
Cost Optimization Strategies
Effective cost optimization strategies are paramount for chemical manufacturers aiming to enhance profitability and maintain competitive advantage. These strategies can vary widely but share core elements that drive efficiency.
- Process Improvement: Companies invest in refining production processes to eliminate waste and enhance productivity. This might include transitioning from batch processing to continuous processing for certain products, significantly reducing downtime.
- Energy Management: Energy costs are a substantial part of overhead in chemical manufacturing. Implementing energy-efficient technologies and practices is essential. For instance, investing in modern machinery that consumes less energy can lead to significant savings over time.
- Outsourcing Non-Core Activities: Another method is to focus on core competencies while outsourcing non-essential tasks. This approach allows companies to reduce operational costs and redirect focus toward strategic growth areas.
- Use of Digital Technologies: Embracing digital technologies, such as predictive maintenance and AI-driven analytics, can help anticipate equipment failures before they occur, thus reducing costly downtimes and maintenance expenses.
"Cost optimization in chemical manufacturing isn't just about cutting expenses; it's about fundamentally rethinking how processes are organized to achieve higher efficiency."
Future Directions in Chemical Manufacturing
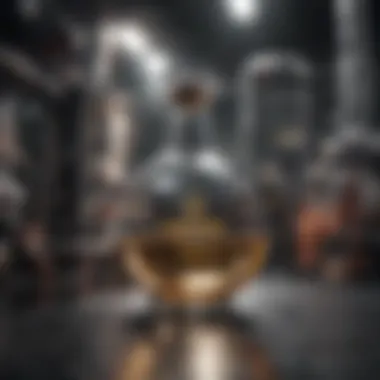
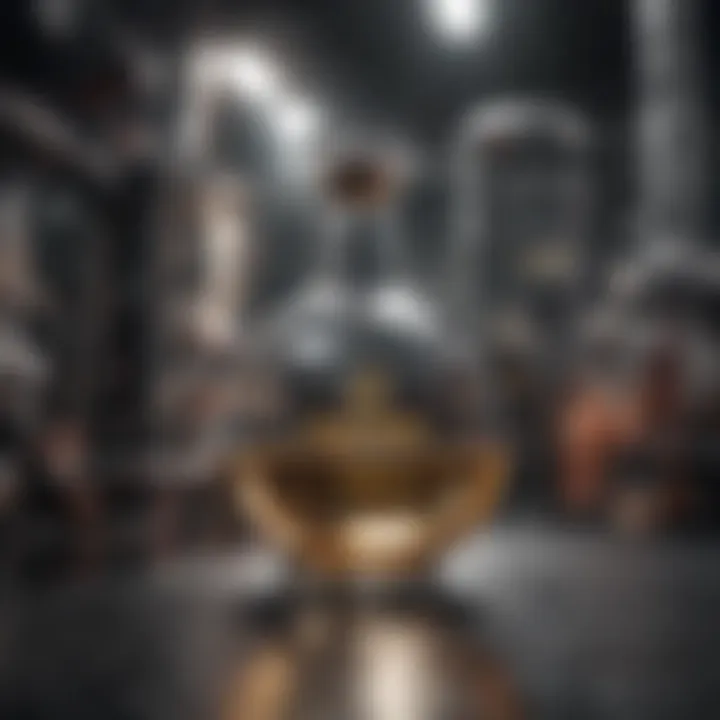
Future directions in chemical manufacturing present essential considerations for the long-term viability of the industry. The landscape is rapidly shifting due to technological advancements and increasing demands for sustainability. This section discusses these pivotal changes and their implications.
Emerging Technologies
Emerging technologies play a crucial role in revolutionizing chemical manufacturing. These innovations not only enhance productivity but also address the growing concerns of environmental impact. For instance, biomanufacturing is gaining traction, utilizing living organisms to produce chemicals more sustainably. This method can reduce waste generation and lower energy consumption compared to traditional techniques.
Another area of focus is the utilization of artificial intelligence and machine learning. These technologies can optimize production processes, improve quality control, and facilitate predictive maintenance. The integration of smart sensors and IoT devices offers real-time monitoring, leading to more efficient operations.
It is clear that emerging technologies can significantly reshape chemical manufacturing, making it more sustainable and efficient.
Furthermore, the rise of digital twins—virtual replicas of physical systems—allows for better simulation and analysis before actual production. This predictive approach can help identify potential issues, thus reducing downtime and enhancing productivity.
Sustainable Practices and Innovations
Sustainability has never been more critical within chemical manufacturing. The sector faces pressure from regulations and the public to reduce its carbon footprint. Therefore, companies are increasingly adopting sustainable practices. One notable trend is the shift towards circular economy principles, which emphasize reusing materials and minimizing waste.
Innovations such as process intensification help in achieving sustainability goals. These techniques reduce the number of steps in chemical processes, lowering energy requirements and waste production. Additionally, innovations in green chemistry methods prioritize safer, more sustainable chemicals in production.
Several companies are also exploring novel materials that can biodegrade after use, eliminating long-term waste problems. Companies like BASF and Dow are leading initiatives to develop bio-based feedstocks, which can lower reliance on fossil fuels.
Case Studies of Successful Chemical Manufacturing
Case studies serve as illustrative examples of best practices within the chemical manufacturing industry. They provide insights into how specific companies have navigated challenges, exploited opportunities, and implemented innovations. Understanding these instances is crucial for several reasons. First, they highlight the critical role of modernization and adaptation in today's fast-evolving market. Furthermore, these case studies underscore the importance of sustainability efforts, showcasing how companies can maintain profitability while being environmentally responsible.
Additionally, analyzing successful case studies offers lessons that can be applied across various segments of the chemical manufacturing sector. They can guide future strategies for both large and small enterprises in terms of operational efficiency, technology integration, and regulatory compliance.
Large-scale Chemical Plants
Large-scale chemical plants represent the backbone of the chemical manufacturing industry. These facilities produce various chemicals at massive volumes, catering to diverse industries ranging from pharmaceuticals to plastics. Key elements such as economies of scale and advanced processing technologies play paramount roles in their operations.
For instance, Dow Chemical's Baytown Complex in Texas showcases how integration and innovation are employed to enhance productivity and reduce costs. The site operates several production units that produce ethylene and propylene, serving as foundations for a wide range of chemicals. By leveraging sophisticated process control systems and real-time data analytics, Dow optimizes its output and minimizes waste.
Moreover, large-scale plants often face significant challenges, including supply chain disruptions and environmental regulations. However, many have adopted sustainable practices. One example is BASF's Ludwigshafen site in Germany, which has implemented a circular economy approach, minimizing chemical waste while maximizing resource recovery. This adaptability is beneficial not only to the companies but also to the industries relying on their products.
Innovations in Small Enterprises
While large chemical plants dominate production, small enterprises also play a significant role in innovation and sustainability within the chemical manufacturing sector. These smaller entities often focus on niche markets, creating specialized products that fulfill specific consumer demands. For example, a small startup might develop eco-friendly cleaning agents by utilizing biobased feedstocks, thus addressing the growing consumer awareness surrounding health and environmental issues.
Case studies of such enterprises demonstrate how agility in operations allows for faster adaptations to market trends. A notable example is GreenChem, which has successfully innovated a range of biodegradable cleaning products that market well due to their sustainability claims. Their focus on research and development, even with limited resources, reveals that ingenuity can outpace the size advantage of larger corporations.
Moreover, partnerships with academic institutions often enrich these small businesses, allowing them to tap into cutting-edge research and development without significant overhead. Through this collaboration, small enterprises can bring innovative products to market quickly and efficiently. This ability enhances competition and drives the entire industry toward more sustainable practices.
Interdisciplinary Approach to Chemical Manufacturing
The field of chemical manufacturing is increasingly drawing insights from diverse disciplines. An interdisciplinary approach fosters innovation and leads to more holistic problem-solving capabilities. By integrating knowledge from chemistry, engineering, environmental science, and even sociology, the industry can enhance both efficiency and sustainability. This section will explore collaboration with academic institutions and the significance of industry partnerships to propel advancements in the field.
Collaboration with Academic Institutions
Collaboration between academic institutions and chemical manufacturers is crucial. Universities and research organizations often serve as innovation hubs. They conduct cutting-edge research that can be transformed into practical applications.
Such partnerships can take various forms, including:
- Joint research initiatives that focus on new materials and processes.
- Internships and co-op programs that provide real-world experiences for students while addressing industry needs.
- Workshops and seminars that facilitate knowledge transfer between researchers and professionals.
This collaboration helps to drive the development of new technologies. For example, research in catalysis at universities has led to more efficient production methods in chemical plants. Furthermore, access to academic resources allows manufacturers to stay ahead of regulatory changes and incorporate sustainable practices.
Industry Partnerships and Research
Industry partnerships are vital in bridging the gap between theoretical research and practical application. Manufacturers often face challenges that require immediate solutions, and academic research can provide those solutions. Through partnerships, both industries and academic institutions can benefit from shared resources, funding, and expertise.
Some notable aspects of these partnerships include:
- Collaborative research projects that address specific industry problems, such as waste reduction or energy efficiency.
- Access to cutting-edge technology and highly skilled labor, enhancing production capabilities.
- Initiatives to align academic curricula with industry needs, ensuring future generations are equipped with relevant skills.
Moreover, partnerships can expedite the commercialization of innovative products. By leveraging each other’s strengths, they can create a symbiotic relationship that fuels growth and enhances competitiveness in the global market.
"Interdisciplinary collaboration is not just beneficial; it is essential for the evolution of chemical manufacturing. It paves the way for innovations that can redefine the industry."
In summary, the interdisciplinary approach in chemical manufacturing is a catalyst for growth and innovation. Through collaboration with academic institutions and strategic industry partnerships, manufacturers can leverage diverse knowledge and skills. This not only enhances operational efficiency but also fosters a culture of continuous improvement and sustainability.
Finale
The conclusion is a vital section of this article as it presents a synthesis of the key findings related to chemical manufacturing. It reinforces the significance of understanding the innovations, challenges, and future directions that characterize this domain. One must recognize how these aspects contribute not only to economic growth but also to sustainable practices in the chemical industry.
In summarizing key insights, we revisit the importance of technological advancements in manufacturing processes. These innovations lead to improved efficiency, reduced waste, and safer operations. The integration of automation and robotics enhances precision while minimizing human error, which is critical in managing hazardous chemicals. Furthermore, the article emphasizes the role of regulatory frameworks. Staying compliant with these regulations is not just a legal obligation, but an ethical one that underscores the industry's commitment to safety and environmental stewardship.
Research indicates that addressing the environmental impacts of chemical manufacturing is imperative.