In-Depth Exploration of Plasma Nitriding Processes
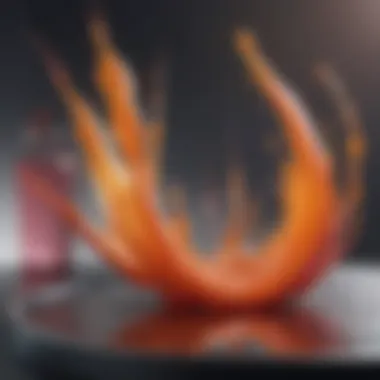
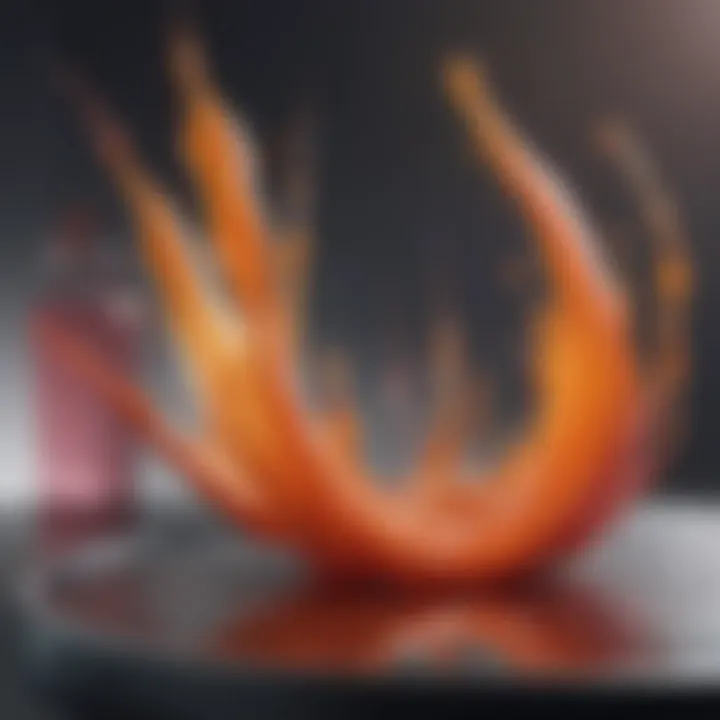
Intro
Plasma nitriding is a pivotal surface treatment that addresses critical performance requirements in various materials. By enhancing properties like hardness, wear resistance, and corrosion resistance, it plays an essential role in industries such as automotive, aerospace, and manufacturing. This article will explore the nuances of plasma nitriding, dissecting its processes, applications, and advantages. A systematic approach is vital to understanding how this technique can improve material performance and adapt to evolving industrial needs.
Research Overview
Key Findings
This exploration reveals several important aspects of plasma nitriding:
- Improved Surface Hardness: Plasma nitriding significantly boosts the surface hardness of materials, which is crucial for enhancing durability.
- Wear Resistance: The process provides a tough surface that withstands abrasion and extends the lifespan of components.
- Corrosion Resistance: Enhanced resistance to corrosion helps in prolonging the lifecycle of tools and parts, reducing maintenance costs.
- Versatility: Suitable for a range of materials from steel to titanium, plasma nitriding offers broad application potential.
Study Methodology
To gather insights, a comprehensive review of existing literature and case studies was conducted. The methodology involved analyzing research papers, industry reports, and technical documents. This ensures an up-to-date understanding while incorporating historical perspectives.
Background and Context
Historical Background
The evolution of plasma nitriding can be traced back to the late 20th century when the need for advanced surface treatments became evident. Initially, conventional nitriding methods dominated. However, as technology progressed, plasma nitriding emerged, offering superior control over the process parameters and more consistent results.
Current Trends in the Field
Today, plasma nitriding is gaining traction as industries prioritize sustainability and efficiency. New research focuses on optimizing process conditions to minimize energy consumption and reduce environmental impact. Additionally, advancements in automation and real-time monitoring are improving accuracy and reliability in production.
"By enhancing material properties, plasma nitriding contributes significantly to both performance and longevity, making it an essential technique in modern manufacturing."
As we delve deeper into this exploration, it will become clear how plasma nitriding not only addresses the demands of today but also paves the way for future developments in materials science.
Intro to Plasma Nitriding
Plasma nitriding is an advanced surface treatment process notable for its ability to significantly enhance the hardness, wear resistance, and corrosion resistance of materials. In a manufacturing landscape that constantly seeks to improve the performance of components, understanding plasma nitriding becomes essential. The relevance of this topic is reflected in its diverse applications across various industries including automotive, industrial machinery, and medical devices.
The importance of plasma nitriding lies in its unique characteristics compared to traditional nitriding methods. It operates at lower temperatures, reducing the risk of distortion in heat-sensitive components. This feature is particularly valuable in producing intricate parts or components with close tolerances. Not only does the process improve the surface qualities, but it also extends the lifespan of parts, thus providing economic benefits through reduced replacement costs.
Definition and Overview
Plasma nitriding is defined as a thermochemical Treatment method that diffuses nitrogen into the surface of materials to create a hardened layer. The process involves the ionization of gas, typically nitrogen, inside a vacuum chamber. The resulting plasma creates a reactive environment where nitrogen ions penetrate the surface of the workpiece. This results in the formation of hard nitrides, enhancing the material's properties.
In practice, plasma nitriding can be applied to various metals, most commonly steel. The process is particularly effective for components that require exceptional hardness and durability, enabling them to withstand harsh operating conditions. Unlike traditional nitriding, plasma nitriding allows for better control over the treatment, including nitrogen concentration and treatment duration, leading to more predictable outcomes.
Historical Context
The origins of nitriding trace back to the early 20th century, primarily focusing on gas nitriding. However, as technology advanced, the need for more effective and precise techniques emerged. Plasma nitriding began to gain traction in the 1970s during the rise of industrial automation and the aerospace sector.
Over the decades, plasma nitriding has evolved significantly. Technological innovations have led to improvements in equipment and process control. Researchers have continued to refine the process, addressing challenges such as uniformity of the nitrided layer and the minimization of dimensional changes in critical components.
The ongoing development in plasma nitriding technology has made it a preferred choice for many industries aiming to enhance the performance of their products. It is widely recognized for its capabilities and numerous advantages, establishing itself as a key process in modern manufacturing.
Fundamental Principles of Plasma Nitriding
Understanding the fundamental principles of plasma nitriding is essential for grasping how this advanced treatment technique enhances material properties. Plasma nitriding fundamentally relies on the interaction between ionized nitrogen and the surface of the material. When examining this process, three primary areas deserve attention: the mechanism of plasma generation and the dynamical aspects of the nitriding process.
Mechanism of Plasma Generation
The creation of plasma is the first critical step in plasma nitriding. Plasma can be defined as a state of matter where gas is ionized, containing free electrons and ions. This ionization occurs in a vacuum chamber. A common gas, such as nitrogen, is introduced into the chamber, which is then subjected to a high-voltage electric field. This electric field causes the nitrogen gas molecules to become ionized.
- Ionization Process:
- Plasma Characteristics:
- Temperature Control:
- When nitrogen gas molecules are exposed to the high-voltage, they break apart, forming positive ions and free electrons. This ionization is crucial for the nitriding process.
- The resulting plasma is chemically active. The ions generated are directed toward the surface of the material, which will be treated. This controlled environment allows for precise manipulation of process parameters.
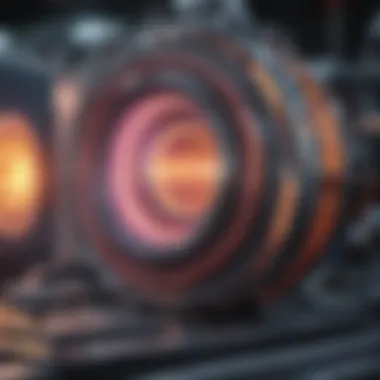
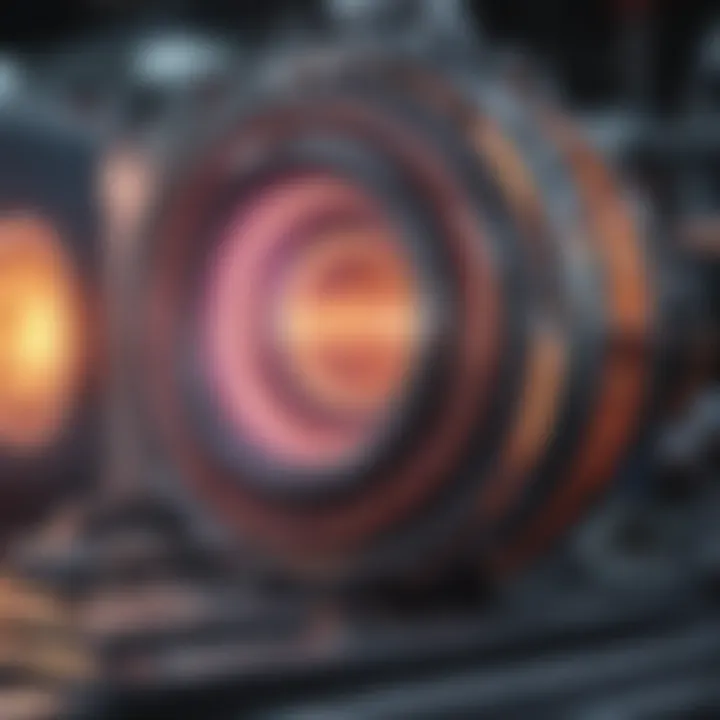
- Plasma generation occurs at relatively low temperatures, usually between 400 to 600 degrees Celsius. This is an advantage as it reduces distortion and maintains the integrity of the material being treated.
The effectiveness of plasma generation significantly influences how nitriding occurs. Inappropriate control of these elements can cause inefficient treatment or potential damage to the material.
Nitriding Process Dynamics
Nitriding itself involves several dynamic steps once the plasma has been generated. Understanding these dynamics can help optimize the plasma nitriding process for various applications.
- Diffusion:
- Chemical Reaction:
- Time and Pressure:
- Monitoring Parameters:
- After ion bombardment, nitrogen ions begin to diffuse into the surface of the material. The diffusion rate can be controlled by factors such as temperature, duration of exposure, and material type.
- As nitrogen diffuses, it reacts with the surface, forming nitrides. These nitrides are significantly harder than the base material, leading to enhanced wear resistance.
- The process time and chamber pressure play crucial roles in determining the depth of nitriding. Longer exposure times at optimal pressures can lead to deeper diffusion layers, providing better surface characteristics.
- Continuous monitoring of the process is essential. Factors like gas composition, pressure fluctuations, and power input must be maintained within specific ranges to achieve the desired results.
"Plasma nitriding offers an innovative approach to modifying the surface of materials, thus improving their overall performance in challenging environments."
By comprehending these principles, students, researchers, educators, and professionals can better appreciate how plasma nitriding enhances material properties.
Plasma Nitriding Equipment
The importance of plasma nitriding equipment cannot be overstated. It serves as the backbone of the nitriding process, directly impacting the efficiency and quality of the finished product. Understanding the different types of equipment and the selection criteria is crucial for any operation looking to adopt this advanced surface treatment technique. This section delves into the essential elements of plasma nitriding equipment, exploring its benefits and considerations necessary for optimal performance.
Types of Equipment Used
Plasma nitriding requires specialized equipment tailored for generating an appropriate plasma environment. Some of the main types of equipment include:
- Plasma Nitriding Chambers: These are the primary units where the nitriding process occurs. They maintain a controlled atmosphere necessary for effective nitrogen infusion into the metal surface.
- Power Supplies: High-frequency generators or transformer-rectifiers provide the energy necessary to create plasma. They must be selected based on the desired power level for different types of materials.
- Vacuum Pumps: Essential for maintaining a low-pressure environment in the chamber, vacuum pumps enable the removal of air and contaminants prior to the nitriding process.
- Gas Feed Systems: These systems introduce nitrogen and other gases at controlled rates. Proper gas management is vital for achieving uniform treatment.
- Cooling Systems: They regulate the temperature during and after the nitriding process. Excess heat can affect the properties of the material being treated.
Each of these components plays a significant role in the overall nitriding process, contributing to its efficiency and effectiveness.
Selection Criteria for Equipment
Choosing the right plasma nitriding equipment is a multifaceted decision that hinges on several critical factors:
- Material Compatibility: Equipment must accommodate the specific materials being treated. Different materials may require adjusted parameters for effective nitriding.
- Processing Capacity: The size and volume of the equipment should match the production needs. Facilities processing large batches will need larger chambers and more robust power supplies.
- Energy Efficiency: Given the ongoing concerns about energy consumption, selecting equipment with high energy efficiency can lead to significant cost savings over time.
- Control Systems: Advanced control systems provide better monitoring and adjustments during the process. These systems improve consistency and ensure quality production.
- Cost vs. Benefit: Initial investment costs are important, but potential returns on investment from enhanced surface properties must also be considered.
When selecting equipment, consider both current needs and future expansion plans to ensure your investment remains relevant.
The right combination of equipment facilitates a more reliable nitriding process. By addressing these selection criteria carefully, organizations can position themselves to achieve optimal results in plasma nitriding.
Applications of Plasma Nitriding
The application of plasma nitriding is crucial in various industries due to its ability to significantly enhance the surface properties of materials. This advanced process is widely recognized for its benefits in improving hardness, wear resistance, and corrosion resistance. The versatility of plasma nitriding allows it to be employed across numerous sectors, ensuring durable and high-performance products. A few notable applications include automotive components, industrial machinery parts, and medical devices. Each of these sectors benefits uniquely from plasma nitriding, which ultimately enhances the longevity and performance of their respective products.
Automotive Components
In the automotive industry, plasma nitriding is extensively used to treat components that face high-stress conditions. Parts such as crankshafts, gears, and valve trains undergo this process to achieve superior surface hardness. The enhanced hardness not only extends the lifespan of these components but also reduces the likelihood of mechanical failure, which is critical for vehicle reliability.
One significant advantage of plasma nitriding in automotive applications is its uniform case depth, which can be precisely controlled. This uniformity allows engineers to tailor the nitriding process according to specific performance requirements. Additionally, the lower processing temperatures associated with plasma nitriding minimize distorsion, a common issue with traditional nitriding methods.
Industrial Machinery Parts
The industrial sector also heavily relies on plasma nitriding for various machinery parts. Components such as shafts, coupling parts, and dies benefit from the increased wear resistance that plasma nitriding provides. As these parts typically operate in harsh environments and must endure repeated friction, the surface treatment ensures they maintain functionality over time.
By treating industrial machinery parts with plasma nitriding, manufacturers can achieve significant reductions in maintenance costs due to less frequent replacements. Furthermore, the smoother surface finish resulting from the nitriding process can enhance lubrication efficiency, vastly extending gear life and operational efficiency in machinery.
Medical Devices
In the medical field, the application of plasma nitriding offers critical advantages as well. Medical devices, including surgical instruments and implants, benefit from enhanced biocompatibility and surface hardness. Here, the increased resistance to wear and corrosion is essential, as these devices often interact with bodily fluids and tissues.
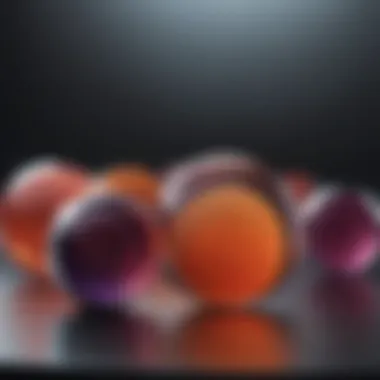
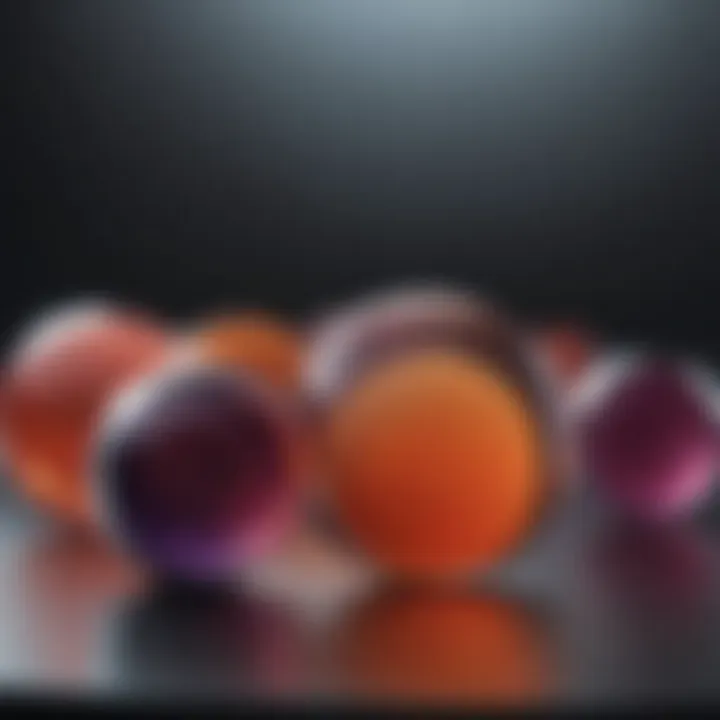
The meticulous control over surface properties via plasma nitriding ensures that medical devices maintain their integrity and function over extended periods. Additionally, the process can improve the aesthetic appearance of instruments, a consideration that is important for both practical usage and patient trust.
Plasma nitriding enhances the longevity and reliability of medical components, making it a preferred treatment in the healthcare sector.
Plasma nitriding is an advanced technique that addresses the critical demands across multiple industries, ensuring enhanced performance, longevity, and reliability.
In summary, the applications of plasma nitriding span various high-demand sectors. Each sector can uniquely benefit from the advantages this process provides, leading to improved performance, efficiency, and durability. As industries continue to evolve and face new challenges, the role of plasma nitriding remains essential for achieving the desired material properties.
Comparative Analysis with Other Nitriding Techniques
The comparative analysis of plasma nitriding with other nitriding techniques is crucial in understanding the unique advantages and limitations of each method. As industries increasingly seek effective methods to enhance material properties, distinguishing the characteristics of plasma nitriding helps in making informed decisions regarding its application. This analysis will particularly consider gas nitriding and ion nitriding, two prominent alternatives.
Comparison with Gas Nitriding
Gas nitriding is a widely adopted method that utilizes ammonia gas to treat metal surfaces. In this process, the gas dissociates and diffuses nitrogen into the surface layers of the material, resulting in hardness improvements.
Key Comparisons:
- Process Control: Plasma nitriding allows for better control of process parameters. This results in more consistent outcomes regarding depth and hardness. In contrast, gas nitriding can sometimes yield uneven results.
- Temperature and Time: Plasma nitriding operates at lower temperatures (typically between 400Β°C and 600Β°C) and shorter duration compared to gas nitriding. This reduces the risk of thermal distortion for sensitive components, making plasma nitriding favorable for high-precision parts.
- Environmental Impact: The emissions in gas nitriding can be higher due to ammonia usage, whereas plasma nitriding often generates fewer harmful substances. This makes plasma nitriding an attractive option from an environmental standpoint.
Comparison with Ion Nitriding
Ion nitriding, like plasma nitriding, involves the use of a plasma environment, but the approach differs. It uses ionized nitrogen rather than a neutral gas to introduce nitrogen into the material surface. This allows deeper penetration and enhanced properties.
Key Comparisons:
- Surface Modification: Ion nitriding often results in a superficial layer that is harder than that produced by plasma nitriding. It is effective for components that require maximum hardness at the surface level.
- Cost-Effectiveness: Ion nitriding equipment typically involves higher initial investment and operational costs compared to plasma nitriding setups. Organizations need to weigh the benefits of hardness against cost when choosing between these methods.
- Complexity of Operation: Ion nitriding requires a more intricate setup and greater operational expertise. Plasma nitriding, while still advanced, may be more accessible for facilities lacking extensive technical resources.
"Understanding the differences between these nitriding techniques is essential for industries aiming to optimize the performance of their components."
Advantages of Plasma Nitriding
Plasma nitriding is recognized for its significant advantages in enhancing the surface properties of various materials. This is crucial in industries where durability and performance are paramount. The benefits of plasma nitriding extend beyond mere surface treatment; they fundamentally alter the properties of materials, making them more suitable for demanding applications. Understanding these advantages is essential for industries looking to improve product performance and reliability.
Enhanced Surface Hardness
One of the most notable benefits of plasma nitriding is the enhancement of surface hardness. During the nitriding process, nitrogen atoms diffuse into the surface of the material, forming hard nitrides. This increase in hardness improves the material's ability to withstand wear and stress. Materials like steel can achieve hardness levels significantly higher than those of untreated counterparts. This property is especially beneficial in automotive and industrial applications where components face constant friction and abrasion.
Improved Wear Resistance
In addition to hardness, plasma nitriding greatly increases wear resistance. The process not only hardens the surface but also alters the microstructure of the material to be more resilient to wear. Components treated with plasma nitriding tend to show less degradation over time, which can lead to longer service life and reduced maintenance costs. For instance, in machining processes, tools that undergo plasma nitriding experience less wear, translating to higher efficiency and lower replacement rates. This is a clear advantage for manufacturers seeking to optimize production costs.
Corrosion Resistance
Corrosion is a significant concern for many industries, especially those involving harsh environments. Plasma nitriding offers considerable improvements in corrosion resistance as well. The treatment forms a diffusion layer that protects the base material from corrosive agents. This is vital for components in medical devices, petrochemical equipment, and other industries exposed to aggressive conditions. By enhancing corrosion resistance, plasma nitriding contributes to the longevity and reliability of components, ensuring they perform effectively under challenging circumstances.
"Plasma nitriding is not just a surface treatment; it fundamentally enhances material properties, crucial for performance-driven applications."
In summary, the advantages of plasma nitriding encompass enhanced surface hardness, improved wear resistance, and increased corrosion resistance. Each of these benefits is significant in ensuring durability and reliability in various applications across multiple industries. For those involved in material selection and treatment processes, understanding these advantages is essential for making informed decisions.
Environmental Considerations
Understanding the environmental considerations associated with plasma nitriding is crucial for a holistic view of the process. As industrial practices evolve, concerns over emissions and waste management have gained prominence. It is essential to address these issues not only to comply with regulations but also to promote sustainable manufacturing.
Emissions and Waste Management
The plasma nitriding process typically generates fewer emissions compared to traditional nitriding methods. This is due to its vacuum environment, which minimizes the release of harmful gases. However, substances like nitrogen oxides can still be emitted. Proper monitoring is necessary to manage and mitigate these emissions effectively. Historically, industries have faced significant challenges in waste management, particularly regarding the disposal of hazardous materials. With plasma nitriding, solid waste is often reduced, yet the remaining waste must be handled according to strict standards.
To ensure responsible waste management, companies can adopt several strategies:
- Recycling: Materials that can be recycled should be recovered to minimize waste volume.
- Treating Hazardous Waste: When hazardous materials are unavoidable, using appropriate treatment methods is key to reducing their environmental impact.
- Regular Maintenance: Keeping equipment in optimal working condition limits unintentional waste production.
By focusing on emissions reduction and effective waste management, enterprises can not only fulfill legal obligations but also demonstrate a commitment to environmental stewardship.
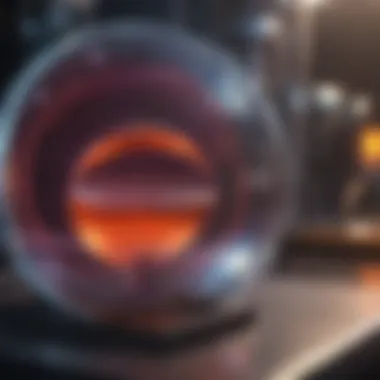
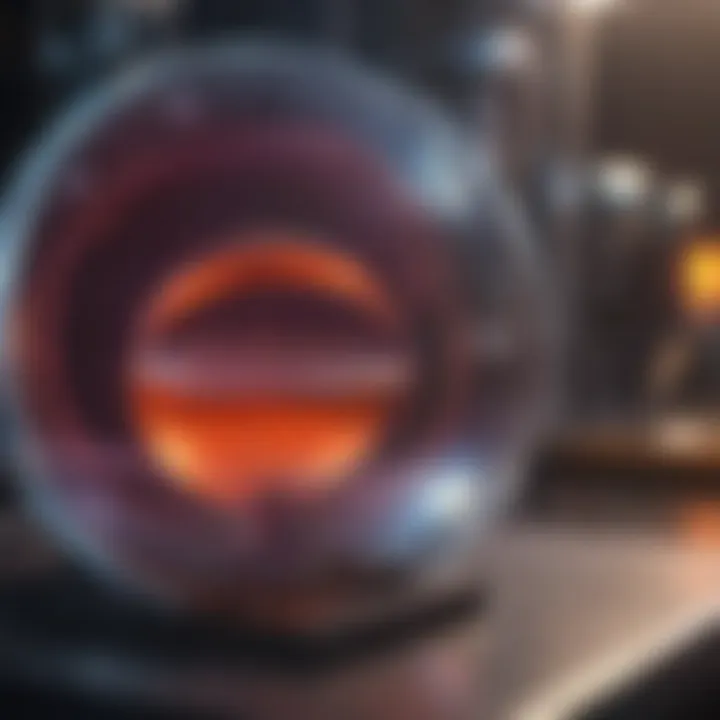
Regulatory Compliance
Regulatory compliance for plasma nitriding is paramount. Various regulations exist to govern emissions and waste disposal, ensuring that industries operate within acceptable environmental limits. Organizations must be aware of these regulations to avoid penalties and maintain a positive public image.
In the United States, agencies like the Environmental Protection Agency (EPA) establish guidelines that plasma nitriding facilities must follow. Compliance includes adherence to emission limits and waste management practices. Other countries have similar regulatory bodies, along with specific local regulations.
Establishing a robust compliance strategy is beneficial. Businesses should conduct regular audits to assess their adherence to regulations. Additionally, training employees on compliance requirements can foster a culture of accountability and awareness.
In summary, integrating environmental considerations into plasma nitriding practices enhances sustainability and compliance, fostering both ecological responsibility and operational efficiency.
Safety Protocols in Plasma Nitriding
Safety protocols are fundamental in ensuring a safe and effective plasma nitriding process. Neglecting these can lead to accidents that pose serious threats to workers' health and the integrity of the equipment. The importance of implementing thorough safety protocols cannot be overstated as they protect personnel, minimize risk, and ensure that operations comply with industry regulations.
Workplace Safety Practices
In plasma nitriding environments, workplace safety practices serve as the first line of defense against accidents. Establishing a culture of safety is essential in minimizing hazards. Here are key practices to consider:
- Personal Protective Equipment (PPE): Workers should wear appropriate PPE, such as gloves, goggles, and face shields to guard against exposure to high temperatures and chemicals used during the process.
- Training Programs: Regular training sessions for employees are vital. Training should cover operational procedures, emergency protocols, and proper use of safety equipment.
- Clear Signage: Proper signage should be displayed. This includes alerts for potential hazards and instructions for safe operation.
- Regular Safety Audits: Conducting audits can help identify safety lapses and areas for improvement. Routine check-ups of safety equipment and emergency exits ensure everything is functional.
- Emergency Protocols: Having a well-defined emergency response plan is necessary. All employees should be familiar with procedures for fires, chemical spills, or equipment failures.
- Ventilation Control: Adequate ventilation in the working area minimizes exposure to harmful fumes. Implementing proper exhaust systems is crucial.
By emphasizing these practices, facilities can create a safer working environment.
Equipment Safety Standards
Another layer of safety involves adherence to equipment safety standards. Equipment used in plasma nitriding must meet specific criteria to prevent malfunctions and accidents. Key standards include:
- Regular Maintenance: Equipment should undergo routine maintenance checks to ensure it operates correctly. This includes inspecting power sources, gas lines, and control systems.
- Calibration Protocols: Equipment must be calibrated to ensure precise operation within tolerable limits. This directly affects the quality of the nitriding process and reduces risk of failure.
- Safety Features: Plasma nitriding equipment should include safety features such as emergency shutoff switches and alarms that detect malfunctions.
- Compliance with Regulations: Equipment must comply with local, national, and sometimes international safety regulations. This can include standards set by organizations like the Occupational Safety and Health Administration (OSHA).
- Documentation and Record Keeping: Maintaining thorough records of maintenance, inspections, and safety training ensures accountability and transparency in operations.
In summary, following stringent safety protocols is vital for the plasma nitriding industry. Clear workplace safety practices combined with robust equipment safety standards pave the way for safer operations and enhanced productivity. Organizations that prioritize these can significantly reduce risks associated with plasma nitriding.
Recent Advancements in Plasma Nitriding Technology
Recent advancements in plasma nitriding technology are shaping its future and expanding its applications. This section highlights the essential developments in the field and how they have improved the process and its outcomes. Innovations in this area provide significant benefits, not only to industries utilizing plasma nitriding but also in terms of addressing environmental concerns and enhancing operational efficiency.
Technological Innovations
Technological advancements have played a pivotal role in optimizing plasma nitriding. One of the major improvements includes the use of advanced plasma generators. These generators enable more precise control over nitrogen levels and plasma properties. By fine-tuning the parameters, manufacturers can achieve better surface hardness and wear resistance.
Another innovation is the increased automation of the nitriding process. Automated systems reduce human error and contribute to consistent results. In addition, the implementation of real-time monitoring systems allows for adjustments during the process, improving product quality.
- Improved plasma uniformity: Modern technologies ensure a more uniform plasma distribution, leading to consistent nitriding across substrate surfaces.
- Optimized energy consumption: Innovations focus on reducing energy use while maintaining effectiveness, which can lead to lower operational costs for companies.
- Enhanced safety features: New equipment designs incorporate safer handling practices for technicians, minimizing risks related to toxic gas emissions.
"Technological advancements are crucial for enhancing the efficiency and effectiveness of plasma nitriding processes."
Future Trends
Looking forward, the plasma nitriding landscape is expected to evolve further. Emerging trends suggest a focus on sustainability and eco-friendly practices. There is a growing emphasis on reducing emissions and waste during the nitriding process. Companies are looking for ways to incorporate more green technologies without sacrificing performance.
Moreover, the compatibility of plasma nitriding with hybrid processing techniques is an area of interest. Combining plasma nitriding with other surface treatment methods could result in even greater material properties. For instance, integrating laser treatment with plasma nitriding might enhance adhesion and surface characteristics.
As industries continue to pursue higher performance materials, the demand for plasma nitriding will likely increase. This growth will necessitate ongoing research and development, with universities and research institutions playing a role in shaping the future of plasma nitriding technology.
Epilogue
The conclusion serves as a vital component in this exploration of plasma nitriding. It helps solidify the information shared across the entire article while drawing attention to the essential benefits and considerations of this advanced surface treatment. This technique is not merely an industrial process; it embodies innovation and progress in material science.
Summary of Key Points
Throughout this article, various aspects of plasma nitriding have been detailed. Here are the primary points that have been discussed:
- Definition and Mechanism: Plasma nitriding enhances surface properties through a controlled plasma environment, introducing nitrogen into the material's surface.
- Applications: The technology finds utility in automotive components, industrial machinery, and medical devices, enhancing their performance and longevity.
- Comparative Analysis: Compared to gas and ion nitriding, plasma nitriding offers more controlled treatment, leading to superior results in hardness and wear resistance.
- Advantaes: The key benefits include increased surface hardness, improved wear resistance, and enhanced corrosion resistance, making it a suitable option for various industries.
- Environmental Considerations: Discussions on emissions and regulatory compliance reflect an awareness of environmental responsibility in manufacturing.
- Safety Protocols: Workplace safety practices and equipment standards are essential to ensure a safe operational environment.
- Recent Advancements: The latest technological innovations point towards a promising future for plasma nitriding in material processing.
Final Thoughts on the Future of Plasma Nitriding
As we look ahead, plasma nitriding is likely to continue evolving. The advancements in technology may lead to more efficient processes, reducing time and resource consumption. Enhanced control mechanisms could improve precision, allowing for customized nitriding based on the specific needs of various industries.
Innovations such as integrating smart technologies can enable real-time monitoring of the nitriding process, ensuring quality and consistency. Moreover, the ongoing research into environmental impacts may yield processes that are not only effective but also sustainable.
"Understanding advanced surface treatment processes like plasma nitriding is crucial for future innovations in material science and engineering."
By grasping the complexities and advantages discussed here, stakeholders can make informed decisions that better their practices and contribute to the ongoing evolution of their respective fields.