Advancements in Laser Seam Tracking Technologies
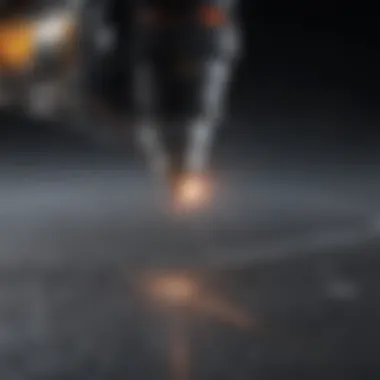
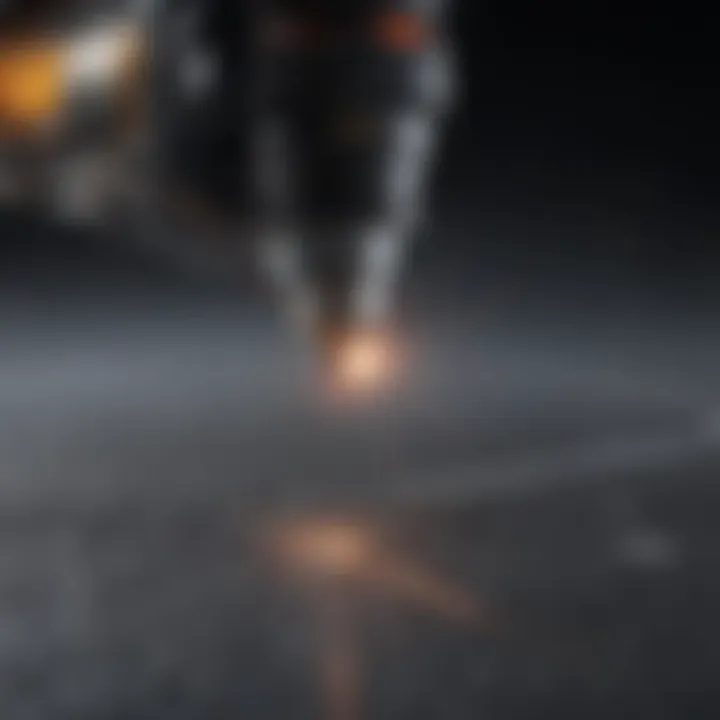
Research Overview
Laser seam tracking technologies have emerged as indispensable tools in modern manufacturing, providing enhanced precision and efficiency in fabrication processes. This section outlines the key findings regarding the principles of operation, systematic advantages, and applications of these technologies, as well as the methodologies applied in recent studies.
Key Findings
- Precision and Accuracy: Laser seam tracking systems significantly improve the alignment of welding torches or cutting tools, which minimizes errors and enhances the quality of the final product.
- Real-time Data Processing: Advanced data processing techniques enable immediate feedback loops, allowing adjustments to be made on-the-fly during manufacturing.
- Increased Efficiency: By automating seam tracking, these systems reduce the need for manual adjustments, thereby accelerating the manufacturing process.
- Diverse Applications: Technologies find applications not just in welding, but also in robotic manipulations, 3D printing, and other fabrication systems.
"Laser seam tracking is transforming traditional processes, bridging gaps between precision and speed."
Study Methodology
Research into laser seam tracking technologies has typically employed various quantitative and qualitative methods. Common practices include:
- Experimental Trials: Analysis of different laser setups in real-world conditions to identify optimal configurations.
- Simulation Models: Computer-based models to predict system performance and troubleshoot potential issues.
- Surveys and Questionnaires: Collecting feedback from industry professionals to gauge effectiveness and areas for improvement.
Background and Context
Understanding the context and evolution of laser seam tracking is crucial for grasping its present significance.
Historical Background
The development of laser seam tracking technologies dates back to the late 20th century when laser-based systems began to be integrated into manufacturing environments. Initially, these systems focused on basic alignment tasks. Over time, rapid advancements in laser and sensor technology fostered more sophisticated systems capable of handling complex geometries and dynamic environments.
Current Trends in the Field
Today, laser seam tracking is experiencing rapid growth. Key trends include:
- Integration with AI: The incorporation of artificial intelligence is enhancing decision-making capabilities within these systems.
- Miniaturization of Components: Smaller, more efficient components allow for more versatile implementations in tight spaces.
- Cross-industry Applications: The versatility of laser seam tracking technologies has extended their usefulness to industries such as aerospace, automotive, and electronics.
In summary, laser seam tracking technologies represent a significant advancement in manufacturing precision. The capability to adapt to various applications while ensuring efficiency positions these systems as a key focus for future research and development.
Preface to Laser Seam Tracking
Laser seam tracking is integral to modern manufacturing processes. This technology enhances the precision of welding and cutting operations, which are crucial in various industries. Understanding laser seam tracking allows professionals to appreciate its benefits in improving productivity and ensuring quality in production. This introduction sets the stage for a deeper exploration of the technology, focusing on its definition, evolution, and relevance.
Definition and Overview
Laser seam tracking refers to the use of laser technology to aid in the alignment and monitoring of seams during welding or cutting operations. This system employs laser beams that continuously assess the position of the workpiece. By tracking the seams in real-time, it enables machines to adjust dynamically, ensuring accurate operations even in complex geometries or varying materials.
The primary objectives of a laser seam tracking system include enhancing precision, reducing wastage, and improving overall production efficiency. This technology integrates hardware components, such as lasers and cameras, with sophisticated software algorithms to process the data collected. By doing so, it provides operators with immediate feedback on seam location. The overall impact is quite significant, reducing the risks of human error and contributing to more reliable production outcomes.
Historical Context and Evolution
Laser seam tracking technologies emerged in the late 20th century, evolving from basic positional sensing systems. Initially, manufacturers relied on mechanical systems for seam alignment, which often resulted in inaccuracies and inefficiencies. The introduction of laser technology revolutionized this area by providing a non-contact method of monitoring seams.
As laser technology advanced, so did the capabilities of seam tracking systems. Early models were limited to simple linear tracking applications. However, innovations in sensor technology and data processing in the 1990s expanded the applications of laser seam tracking. Now, these systems can adapt to different materials, shapes, and welding processes.
Over the years, laser seam tracking has found applications in various fields, including aerospace, automotive, and electronics industries. Manufacturers began to recognize the advantage of integrating these systems into their processes. Today, laser seam tracking represents a crucial component of automated manufacturing systems, embodying a significant leap in precision and efficiency.
Principles of Operation
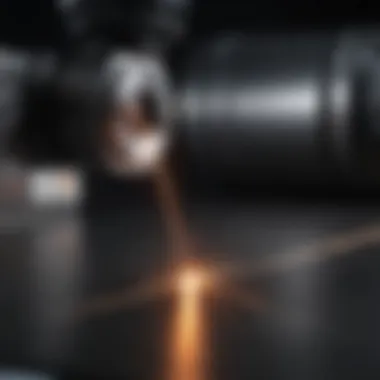
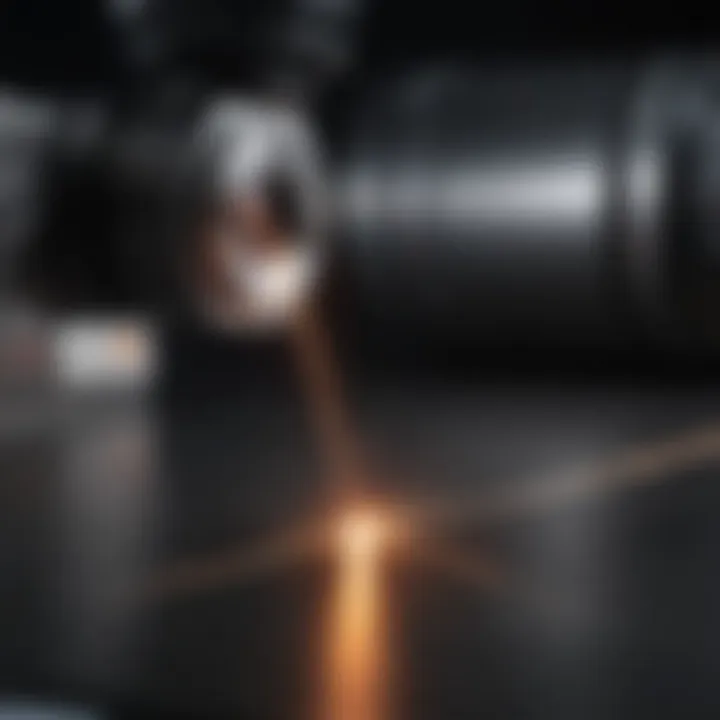
The principles of operation for laser seam tracking technologies serve as the backbone for understanding their effectiveness in various applications. These principles guide the way lasers interact with materials and how data is processed to ensure precision in manufacturing processes. Knowledge of these principles is critical for anyone interested in optimizing production quality and efficiency.
Laser Technology Fundamentals
Laser technology is pivotal in laser seam tracking systems. Lasers produce coherent light that can be concentrated on a small area. The interaction of this light with materials results in predictable outcomes—such as reflection, absorption, or scattering. It is this predictability that laser seam tracking relies upon.
To ensure optimal performance, different types of lasers can be utilized based on the specific material and process involved. For example, fiber lasers are popular in metal cutting due to their high power efficiency and beam quality, while CO2 lasers are often used for non-metals like plastics. Each type of laser has unique characteristics that can be leveraged for various applications in manufacturing.
Seam Tracking Mechanisms
Seam tracking mechanisms are essential for the accurate alignment of the laser beam with the seam to be welded or cut. These mechanisms typically rely on sensors that detect the seam’s position in real-time and adjust the laser accordingly. There are various types of sensors, such as CCD cameras and photodiodes, each offering distinct advantages.
The most common method is to use edge detection algorithms. When the laser beam hits the seam, variations in light intensity provide the data needed to identify the exact location of the seam. This information is then fed back into the control system, allowing for immediate adjustments. Such responsiveness ensures that even with dynamic movements of the workpiece, the laser remains perfectly aligned, which is critical for producing high-quality welds.
Data Acquisition Techniques
Data acquisition is a vital aspect that underpins effective seam tracking technology. It involves gathering the information necessary to monitor and control the process dynamically. Common techniques include the use of high-speed cameras and sensors that record the laser's interaction with the material.
These systems often integrate advanced software for image processing and analysis. The data collected can be processed using algorithms that help determine the necessary adjustments in real-time. Notably, the integration with machine learning is becoming increasingly common, allowing for predictive adjustments based on historical data.
"The efficiency of data acquisition systems directly influences the overall performance of laser seam tracking technologies. Without robust data processing capabilities, precision cannot be achieved."
Investments in cutting-edge data acquisition technology can enhance the information accuracy, leading to significant improvements in production outcomes. This is particularly important in fast-paced industrial environments where immediate feedback is essential for maintaining operational pace.
In summary, understanding the principles of operation—encompassing laser technology, seam tracking mechanisms, and data acquisition techniques—provides critical insights into how laser seam tracking functions. This knowledge is indispensable for students, researchers, and professionals looking to advance their understanding of modern manufacturing technologies.
Applications of Laser Seam Tracking
The field of laser seam tracking technology has gained significant traction in recent years. Its applications stretch across various sectors, reflecting its versatility and effectiveness. This section delves into the importance of laser seam tracking in different industries, elaborating on specific elements, benefits, and considerations important to this technology.
Manufacturing Industries
In manufacturing, laser seam tracking plays a crucial role in enhancing production quality. The technology enables precise alignment of components during the welding process, leading to smooth, consistent seams.
- Quality Assurance: With better tracking, defects decrease, which reduces waste and rework costs. An improved seam quality strengthens the end product, leading to enhanced durability.
- Process Automation: Integrating laser seam tracking into automated systems minimizes human intervention, supporting faster production cycles.
- Flexibility: The adaptability of laser seam tracking systems allows them to be used with various materials and weld types, ensuring that they meet diverse manufacturing needs.
Automotive Sector Utilization
In the automotive sector, the implementation of laser seam tracking technology has become indispensable. With increasing demands for precision in vehicle fabrication, laser solutions rise to meet these needs effectively.
- Speed and Accuracy: The automotive industry often engages in high-volume production. Laser technology offers rapid seam tracking while ensuring dimensional accuracy, crucial for fitting various components.
- Cost Reduction: By lowering the rate of defective components, companies save on costs associated with recalls and repairs. Enhanced seam quality translates to less need for adjustments and repairs.
- Innovation Support: As car designs evolve and integrate advanced materials, laser seam tracking assists manufacturers in adapting to these changes, supporting innovation in vehicle engineering.
Aerospace Applications
The aerospace industry has recognized the profound impact that laser seam tracing can have on safety and performance. The use of this technology means maintaining strict tolerances in high-stakes environments.
- Critical Precision: Aerospace components often undergo extreme conditions. Seam integrity is vital, making laser tracking essential for ensuring high-quality welds.
- Testing and Compliance: Implementing laser seam tracking supports compliance with stringent industry standards. It enables manufacturers to produce documentation proving the quality of their seams.
- Lightweight Structures: The aerospace sector increasingly opts for lightweight materials. Laser tracking effectively accommodates these materials, ensuring adhesion and integrity without added weight.
Electronics and Semiconductor Industries
Laser seam tracking also finds significance in the electronics and semiconductor sectors. The miniaturization of components demands precision in manufacturing.
- Component Density: As devices become smaller and more complex, laser tracking ensures that assemblies align accurately, maintaining performance outputs.
- Reduced Cycle Times: Faster tracking speeds up the production process in this sector, which is often challenged by tight deadlines and increasing consumer demands.
- Quality Management: Precision in assembling electronic components leads to enhanced yield rates, helping companies maintain quality while controlling production costs effectively.
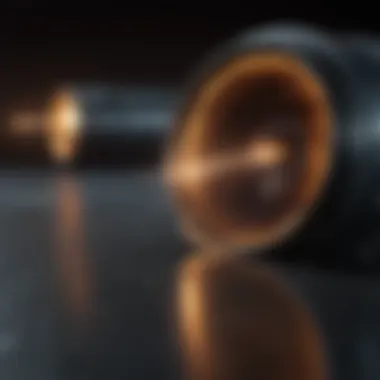
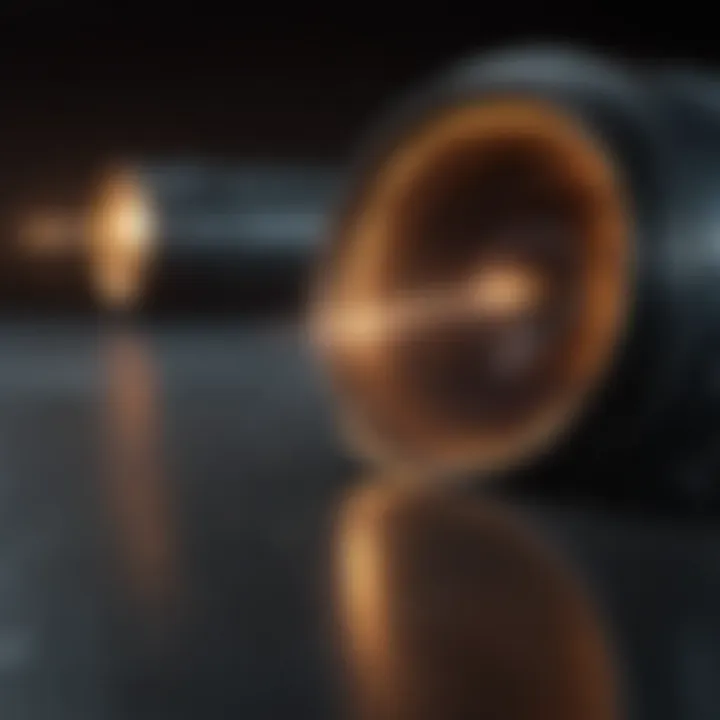
Laser seam tracking technologies stand at the forefront of enabling innovations across diverse sectors, ensuring quality and efficiency in modern manufacturing practices.
Technological Advantages
Laser seam tracking technologies offer significant advantages in modern manufacturing processes. These advantages directly influence the precision, efficiency, and cost-effectiveness of production methods. Understanding these benefits is essential for industries that seek to adopt advanced automation and improve their outputs.
Increased Precision and Accuracy
One of the most notable benefits of laser seam tracking is the enhanced precision it brings. Traditional manual or fixed tracking systems often lead to errors in aligning the materials being processed. With laser seam tracking, the system continuously monitors the position of the weld seam in real-time. This dynamic feature allows adjustments on-the-fly, ensuring that operations remain aligned with exact specifications.
The use of laser technology offers a resolution not easily achievable with other forms of seam tracking. For example, systems like the Telmar Opti-Laser provide accuracy levels of ±0.1 mm. This precision is crucial in sectors where even small discrepancies can lead to structural failures or inefficient energy use. Industries such as aerospace and automotive greatly benefit from this technological edge, turning what once required meticulous manual adjustments into a streamlined automated process.
Improved Production Efficiency
Laser seam tracking not only increases precision; it also fosters improved production efficiency. By automating the monitoring of the seam position, these systems significantly reduce the time spent on manual checks and adjustments. Operators can focus on higher-level tasks rather than getting bogged down in repetitive work.
Additionally, the rapid adjustment capabilities of laser systems allow for faster production cycles. When integrated into robotic welding processes, the ability to adapt to changes in material dimensions or alignments in real-time leads to minimal downtime. The result is a more fluid manufacturing process, where production rates can increase by as much as 30%.
"The integration of laser seam tracking dramatically cuts down operational delays and refines throughput, making it a vital asset for modern factories."
Cost-Effectiveness in the Long Run
While the initial investment in laser seam tracking technology can be substantial, the long-term cost savings make it an attractive option. Enhanced accuracy leads to a decrease in material waste. When seams are aligned with high precision, less reworking is required, which translates into reduced costs for material and labor.
Moreover, the increase in production efficiency often results in lower operational costs. Faster production cycles mean that factories can produce larger quantities without the need for additional workforce or overtime expenses. This cost-effectiveness is particularly advantageous in competitive markets where margins are tight.
In summary, the investment in laser seam tracking technologies pays off through improved precision, increased efficiency, and significant cost reductions, leading to a more competitive stance in any industry.
Challenges and Limitations
Understanding the challenges and limitations associated with laser seam tracking technologies is critical for professionals and researchers in the field. While these technologies present numerous advantages, they also come with specific obstacles that can impact their effectiveness and implementation. By examining these challenges, stakeholders can make informed decisions regarding the application and integration of laser seam tracking in various manufacturing processes.
Environmental Factors
Laser seam tracking systems can be significantly affected by environmental conditions. The presence of dust, smoke, or vibrations can hinder the laser's accuracy. Additionally, variations in ambient light can interfere with data acquisition, leading to incorrect seam detection. For instance, in an industrial setting with fluctuating environmental conditions, maintaining optimal performance requires adaptive solutions. This includes employing robust filtration systems or utilizing laser technologies that mitigate the impact of external factors. Consequently, understanding these environmental challenges is vital for ensuring consistent accuracy in seam tracking applications.
System Complexity and Integration Issues
Integrating laser seam tracking systems into existing manufacturing processes can present considerable complexity. The technology requires a proficient understanding of both hardware and software components. Challenges often arise in the synchronization of these systems with other machinery, necessitating specialized integration solutions. Furthermore, operators must be trained to manage this complexity. This can lead to steep learning curves and potential downtime during the transition phase. Addressing these integration issues is essential for the successful implementation of laser seam tracking in various sectors.
Maintenance and Operational Costs
The operational management of laser seam tracking systems includes ongoing maintenance, which is essential to sustain system performance and reliability. Regular calibration, software updates, and hardware inspections require dedicated resources and skilled personnel. Moreover, the costs associated with maintenance can accumulate, impacting the overall cost-effectiveness of using laser seam tracking. It is crucial for organizations to analyze these long-term expenditures before implementation, ensuring that the benefits of adopting this technology outweigh the operational costs.
Future Directions and Innovations
The field of laser seam tracking is in constant evolution. Innovations in this area will have a critical impact on efficiency and productivity in various industries. Here, we explore emerging technologies, current research trends, and the importance of interdisciplinary collaborations, revealing how these elements together shape the future of laser seam tracking.
Emerging Technologies
Recent advancements are shaping new technologies in laser seam tracking. One example is the integration of artificial intelligence. Machine learning algorithms can analyze data in real time, leading to better decision-making in seam tracking. These algorithms enhance the ability of systems to adapt to different environments and materials.
Furthermore, the development of compact and more powerful laser sources has become possible. These lasers can provide high-resolution tracking with less energy consumption. Additional innovations include enhanced sensor technologies that allow for better detection of seam position. The combination of these innovations is expected to unlock significant improvements in accuracy and speed for manufacturing applications.
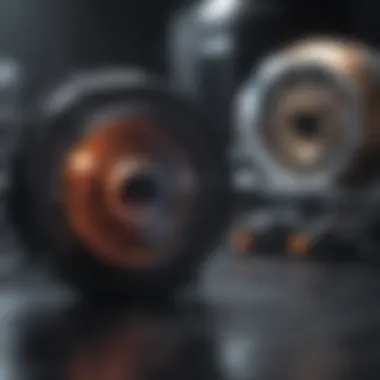
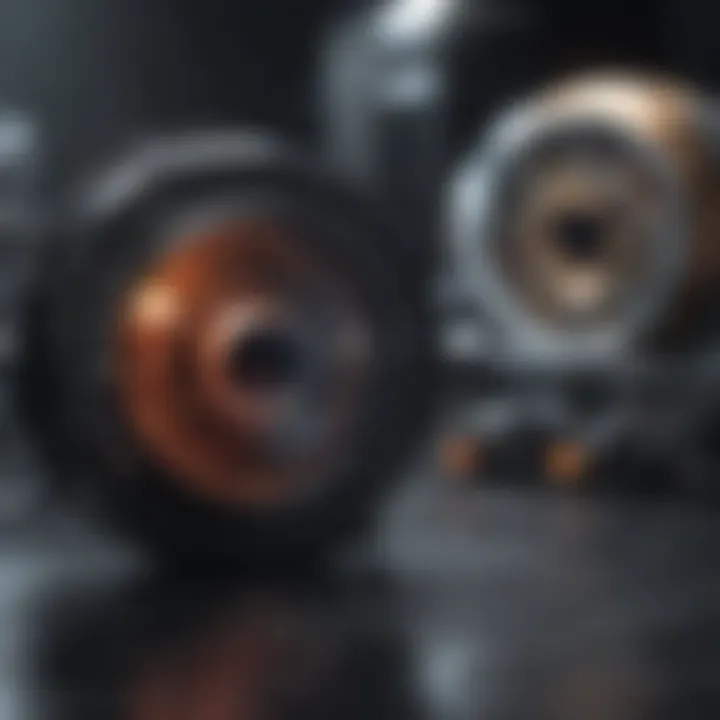
Research Trends in Laser Tracking
Ongoing research is critical in advancing laser seam tracking technologies. Current projects are focusing on improving the robustness of these systems in challenging environments. For example, researchers are exploring how weather variables, such as humidity and temperature, can affect laser tracking. Studies are also investigating the integration of 3D scanning capabilities into seam tracking systems, which could offer real-time adjustments and feedback during the manufacturing process.
Moreover, the shift toward Industry 4.0 emphasizes the need for systems to be interconnected and communicate seamlessly. Research is being directed towards ensuring that laser seam tracking can be integrated with IoT devices. This will enable manufacturers to monitor performance metrics and optimize processes dynamically.
Interdisciplinary Collaborations
Interdisciplinary collaborations are essential to drive innovation in laser seam tracking. This involves cooperation among engineers, computer scientists, and industry experts. Such partnerships can lead to the development of new methodologies and tools that enhance the effectiveness of laser seam tracking technologies.
For instance, combining insights from material science with laser technology research allows for tailored solutions for specific industrial needs. With materials increasingly becoming more specialized, an interdisciplinary approach becomes necessary to explore how different materials interact with laser systems.
Additionally, cross-industry collaborations can lead to shared insights that foster more extensive applications. Technology used in aerospace can inform advancements in automotive sectors and vice versa. These collaborations push the boundaries of what laser seam tracking can achieve, ultimately leading to innovative solutions that benefit multiple domains.
Emerging technologies, research trends, and interdisciplinary collaborations are vital for the successful evolution of laser seam tracking.
Case Studies
The importance of case studies in this article is paramount. They serve as concrete examples that illustrate the practical applications and effectiveness of laser seam tracking technologies. By examining real-world scenarios, we can appreciate not only how these systems are implemented but also the tangible benefits they bring to various industries.
Furthermore, case studies allow us to analyze the impact of laser seam tracking on productivity, quality, and operational efficiency. They provide a lens through which readers can assess the viability of these technologies in overcoming challenges faced in different sectors. This narrative is vital for students, researchers, educators, and professionals as it underscores the relevance of theoretical knowledge in practical domains.
"Case studies bridge the gap between theory and practice, demonstrating the real-world implications of technological advancements."
Successful Implementations in Industry
Numerous industries have successfully adopted laser seam tracking technologies, enhancing their manufacturing processes. One notable example is seen in the automotive sector, where companies like Ford have integrated these technologies into their assembly lines. By using laser tracking, Ford has achieved higher precision in welding seams, which translates into improved vehicle safety and performance.
In the aerospace industry, Boeing has also embraced laser seam tracking. The technology aids in ensuring that components fit correctly during the assembly of aircraft, significantly reducing the risk of errors that could lead to costly delays or safety hazards. Using laser seam tracking, Boeing has documented a measurable increase in production efficiency while maintaining high safety standards.
Application in electronic manufacturing, such as by Intel, showcases another successful implementation. The need for precision in assembling intricate circuits is critical. Laser tracking ensures that each connection is aligned accurately, thereby reducing rework rates and enhancing product quality. This demonstrates the versatility of laser seam tracking across various sectors.
Comparative Analysis with Traditional Methods
When comparing laser seam tracking technologies to traditional methods, several factors come into play. Traditional methods often rely on manual alignment and fixed-jig setups. Such approaches can lead to inconsistencies and variability in seam quality, which ultimately affects the final product.
In contrast, laser seam tracking offers dynamic adaptability. Systems can adjust to real-time changes in the workpiece or environment, which traditional methods cannot accommodate effectively. Enhanced precision is another critical advantage; laser tracking achieves accuracies often beyond human capabilities. This translates into significant cost savings over time due to reduced material waste and fewer defects.
Moreover, the implementation of laser seam tracking facilitates automation. As industries move toward more automated environments, traditional methods may not suffice to meet modern speed and precision requirements. Laser technology integrates seamlessly with robotic systems, further amplifying productivity and efficiency in manufacturing processes.
Epilogue
The conclusion of this article serves as a pivotal synthesis of the journey through laser seam tracking technologies. Understanding these systems is essential for grasping their relevance in the modern manufacturing landscape. Key components, operational mechanics, and industry applications converge to reveal why these technologies matter today.
Summary of Key Insights
In our exploration, several insights emerged:
- Technological Precision: Laser seam tracking substantially enhances accuracy in welding and cutting processes.
- Industry Versatility: The applications span various domains, including automotive, aerospace, and electronics, highlighting its widespread relevance.
- Cost Savings: Over time, implementing laser tracking can drastically reduce waste and improve productivity, offering economic benefits.
- Integration Challenges: Despite advantages, challenges such as environmental factors and system complexities exist, necessitating innovative solutions.
These insights underscore the transformative impact of laser seam tracking technologies on manufacturing efficiency and product quality. By understanding these elements, stakeholders can better appreciate the nuances that drive industrial advancements.
Implications for Future Research
The implications of our findings suggest a need for continued investigation into several areas:
- Advanced Technologies: Research should focus on integrating artificial intelligence and machine learning with laser tracking to enhance functionality and adaptability.
- Environmental Resilience: Addressing how environmental factors affect laser performance will be crucial in optimizing these systems.
- Operator Training: As technology evolves, so too must the training programs to ensure operators fully harness the potential of laser seam tracking.
In summary, future research should aim to refine existing technologies and explore innovative intersections across disciplines. This will play a critical role in ensuring that laser seam tracking remains at the forefront of manufacturing innovation.