Exploring Pressure Instrumentation: Insights and Trends
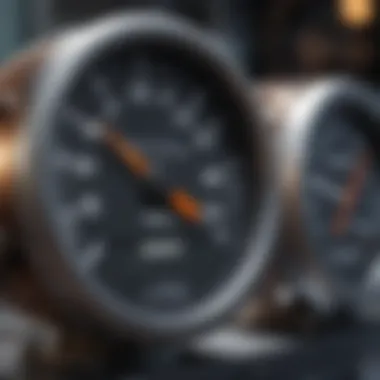
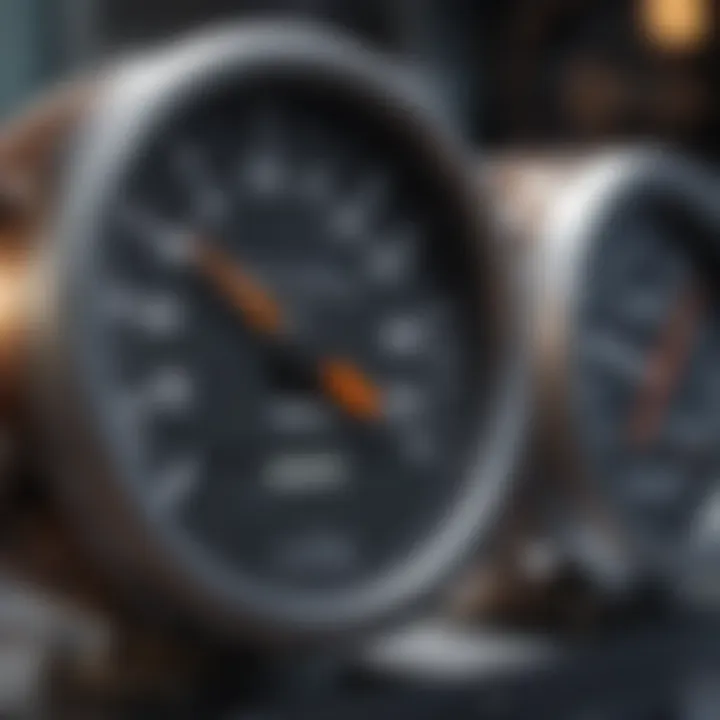
Intro
Pressure instrumentation plays a crucial role in various industries. Understanding how pressures are measured and controlled is essential for safety and efficiency in manufacturing, energy, and environmental monitoring. This article examines the critical principles of pressure measurement and explores modern applications. It also looks into technological advancements and future trends that may shape this field.
Research Overview
Key Findings
- Importance of Calibration: Accurate calibration is essential for ensuring the reliability of pressure sensors.
- Diversity of Sensors: There are several types of pressure sensors, including piezoresistive, capacitive, and optical sensors.
- Industry Applications: Different industries employ pressure instrumentation differently, from HVAC systems to aerospace engineering.
- Emerging Technologies: Innovations such as IoT and advanced materials are enhancing pressure measurement capabilities.
Study Methodology
The research involved a review of existing literature, along with case studies from various industries. Interviews with experts provided insights into current practices and challenges in the use of pressure instrumentation. Data was collected from reputable sources, ensuring a comprehensive understanding of the subject matter.
Background and Context
Historical Background
The development of pressure measurement can be traced back to ancient civilizations. Over time, technologies evolved from simple barometers to sophisticated electronic systems. The 20th century saw rapid advancements, particularly with the introduction of semiconductor technology.
Current Trends in the Field
Today, there is a noticeable shift towards digital pressure sensors. These devices offer enhanced accuracy and real-time monitoring capabilities. Industries increasingly adopt wireless technology, making pressure monitoring more efficient. Furthermore, there is a growing emphasis on the integration of pressure instrumentation with automated systems to streamline processes.
"Effective pressure measurement is not just about technology. It involves understanding the principles that govern measurement and calibration."
The future of pressure instrumentation is likely shaped by ongoing advancements in materials science, precision engineering, and data analytics. As industries face new challenges, understanding these dynamics becomes ever more important.
Foreword to Pressure Instrumentation
Pressure instrumentation plays a crucial role in ensuring the efficient and safe operation of various systems across numerous industries. By accurately measuring and monitoring pressure, engineers and technicians can avert potentially dangerous situations and optimize processes. Pressure measurement is not merely a technical necessity but a foundational aspect of systems ranging from industrial machinery to healthcare equipment.
The significance of understanding pressure instrumentation cannot be overstated. Accurate pressure measurement leads to enhanced safety standards, improved operational efficiency, and reduced costs over time. In industrial applications, such as oil and gas extraction, inaccuracies in pressure measurement can result in catastrophic outcomes. Thus, the foundations of pressure measurement are essential knowledge for both practitioners and scholars.
Definition and Importance of Pressure Measurement
Pressure measurement refers to the assessment of the force exerted by fluids (liquids or gases) on a surface area. This measurement is vital across various sectors, including manufacturing, environmental monitoring, and health care.
Pressure is a fundamental physical quantity, influencing diverse applications. For instance, in the oil and gas industry, maintaining appropriate pressure levels in pipelines can prevent leaks and explosions. In healthcare, devices like sphygmomanometers rely on accurate pressure readings to determine blood pressure, ultimately influencing patient outcomes and treatments.
Understanding pressure measurement also involves comprehending the technologies and methods employed in this process. Knowing how to select the appropriate sensor or gauge for a specific application is paramount to achieving reliable results. As such, learning about the underlying principles governs the successful implementation of pressure instrumentation in real-world scenarios.
Historical Context and Evolution of Pressure Instruments
The history of pressure measurement is both rich and varied, tracing back to ancient civilizations. The earliest known pressure measurement devices appeared in the form of simple water columns used by the Greeks. Over the centuries, advancements led to more sophisticated tools, such as the Bourdon gauge introduced in the 19th century, which revolutionized mechanical pressure sensing.
The evolution of pressure instruments tracks with technological advancements. The introduction of electronic components in the mid-20th century led to the development of electronic pressure sensors. Today, contemporary advancements continue to enhance the accuracy, reliability, and usability of pressure measurement devices.
In the current landscape, the influence of digital electronics cannot be ignored. Digital pressure gauges and smart sensors integrate sophisticated algorithms to enhance measurement precision. Real-time data transmission and analysis support decision-making and monitoring, marking a significant forward leap
"The evolution in pressure instrumentation has paved the way for improvements in safety and efficiency, signifying that history inevitably shapes modern practices.β
The trajectory of pressure measurement has not only broadened the scope of practical applications but also fostered innovation. Understanding this evolutionary context is crucial for recognizing future trends and applications of pressure instrumentation. As industries continue to demand higher performance levels, the journey of pressure measurement technology will surely continue transforming, shaping how we maintain standards in safety and performance in the process.
Fundamental Principles of Pressure Measurement
Understanding the fundamental principles of pressure measurement forms the backbone of effective pressure instrumentation. Pressure measurement plays a critical role in industries ranging from manufacturing to healthcare, ensuring process accuracy and safety. A firm grasp of these principles equips professionals with the knowledge needed to select, implement, and maintain pressure measurement devices effectively.
Basic Physics of Pressure
Pressure, in its simplest form, is defined as force per unit area. Mathematically, it is expressed as:
[ P = \fracFA ]
where P represents pressure, F is the force applied, and A is the area over which the force is distributed. This equation illustrates that as force increases, pressure also increases, assuming the area remains constant. Conversely, increasing the area with a constant force will decrease the pressure.
This basic principle applies to various scenarios, including fluid dynamics and material science. In practice, pressure is frequently measured in units such as pascals (Pa), bar, and psi. Understanding these units and how to convert between them is essential for accurate measurements.
Several factors influence pressure readings. Temperature and density of the fluid being measured can cause variations in pressure. Furthermore, non-ideal conditions like viscosity and turbulence can distort measurements. Recognizing these factors is vital to achieving accurate pressure readings in real-world applications.
Differentiating Absolute, Gauge, and Differential Pressure
Pressure can be categorized primarily into three types: absolute pressure, gauge pressure, and differential pressure. Each plays a unique role and is relevant in specific contexts.
- Absolute Pressure: This is the total pressure exerted by a fluid, measured relative to a perfect vacuum. It is crucial in applications where accurate readings are essential, such as meteorology and vacuum systems. For example, absolute pressure is used to determine the ambient pressure at high altitudes.
- Gauge Pressure: Gauge pressure measures the pressure relative to atmospheric pressure. It is commonly used in everyday applications, such as in tire pressure gauges. One key consideration is that gauge pressure can read zero when the actual pressure equals the surrounding atmospheric pressure.
- Differential Pressure: This type measures the difference in pressure between two points in a system. Differential pressure sensors are vital in processes like flow measurement or filtration systems. For instance, a differential pressure sensor can help monitor a filterβs performance by measuring the pressure drop across the filter.
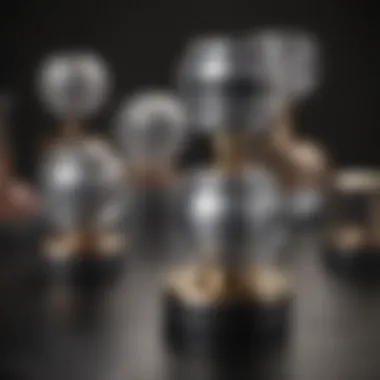
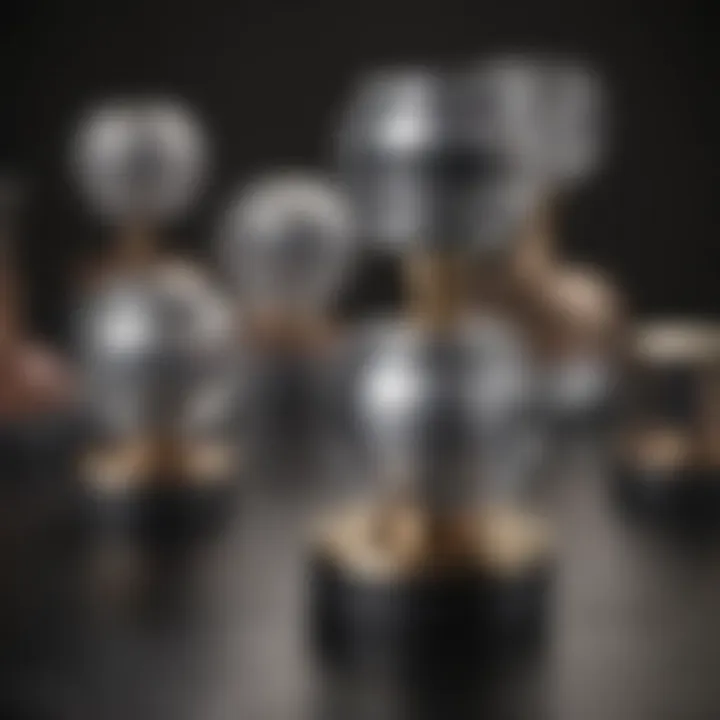
Understanding these distinctions is crucial for selecting the appropriate pressure measurement tools in practical scenarios. Misunderstanding what type of pressure is needed can lead to inaccurate data and potential system failures.
In summary, the fundamental principles of pressure measurement encompass both the basic physics that define pressure itself and the various types of pressure that are relevant in specific applications. With this foundational knowledge, industry practitioners can better navigate the complexities of pressure instrumentation.
Types of Pressure Sensors
In the realm of pressure instrumentation, understanding the types of pressure sensors is essential. These sensors are critical for accurate pressure measurement across various industries. They allow for monitoring, control, and feedback in numerous applications. Knowing the strengths and limitations of each type can lead to better choices in pressure measurement solutions. This section will explore mechanical and electronic pressure sensors, along with optical and hybrid sensors.
Mechanical Pressure Sensors
Mechanical pressure sensors are traditional devices that use physical elements to measure pressure. These sensors often provide reliable, real-time data and are known for their durability in tough environments.
Diaphragm Pressure Transducer
The diaphragm pressure transducer is pivotal for measuring dynamic pressure changes. It uses a flexible diaphragm that deflects under pressure, producing a voltage signal that corresponds to the pressure applied. A key characteristic of this sensor is its sensitivity. It allows for precise measurements in a variety of settings, making it a beneficial choice for applications requiring accuracy.
The unique feature of the diaphragm transducer is its ability to handle both static and dynamic pressure effectively. It can measure rapidly changing pressures, which is crucial in many applications like aerospace and automotive industries. The advantages include high sensitivity and a wide measurement range. However, limitations exist, such as potential sensitivity to temperature changes, which must be considered.
Bourdon Gauge
The Bourdon gauge is another significant mechanical sensor. It operates on the principle of elastic deformation. As pressure increases, the Bourdon tube (curved or coiled tube) straightens, and this movement is translated into a pressure reading. Its key characteristic lies in its simplicity and robustness, making it a popular choice in industrial applications.
A unique feature of the Bourdon gauge is its ability to measure high-pressure levels. This functionality makes it suitable for environments like processing plants or hydraulic systems. Advantages include ease of use and the lack of need for external power. However, accuracy can decrease at extreme pressures, and it may not be ideal for very low-pressure measurements.
Electronic Pressure Sensors
Electronic pressure sensors have gained popularity due to their precision and versatility. These sensors convert pressure into an electronic signal. They are often used in advanced applications that require digital monitoring.
Piezoelectric Sensors
Piezoelectric sensors are known for their capability to detect rapid changes in pressure. They work based on the piezoelectric effect, where pressure creates a charge in certain materials. Their key characteristic is high-speed response, which is crucial for monitoring transient pressure changes in various processes.
The unique advantage of piezoelectric sensors is their ability to operate under extreme conditions, including high temperatures. This feature makes them particularly useful in the automotive industry, where they monitor engine performance. However, these sensors can be affected by temperature and require careful calibration.
Strain Gauge Sensors
Strain gauge sensors operate using a wire that changes resistance when distorted by pressure. This type of sensor is favored for its flexibility in design and accuracy. The key characteristic that stands out is their sensitivity to minute pressure changes.
A key advantage of strain gauge sensors is their adaptability. They can be used in various applications, from industrial machinery to research laboratories. However, they require a power supply and can be susceptible to environmental factors such as humidity, which may affect long-term performance.
Optical and Hybrid Pressure Sensors
Optical and hybrid pressure sensors represent advanced technologies in the field of pressure measurement. These sensors combine optical methods with traditional measurement systems to enhance accuracy and reliability. Optical sensors can measure pressure through changes in light properties, while hybrid systems integrate multiple technologies for better performance.
The main advantage of optical pressure sensors is their immunity to electromagnetic interference, making them suitable for sensitive environments. However, they may be more complex and costly than traditional sensors. As industries advance, the integration of optical and hybrid sensors may lead to innovative applications and improved measurement techniques.
Calibration Techniques in Pressure Instrumentation
Calibration is a critical aspect of pressure instrumentation. It ensures that pressure measuring devices provide accurate and reliable readings. This is important in various fields such as industrial manufacturing, aerospace, and healthcare, where precise pressure measurements are essential. Inaccurate readings can lead to serious consequences, including equipment failure or safety hazards. Therefore, understanding calibration techniques is vital.
Importance of Calibration
Calibration establishes a relationship between the pressure measured by an instrument and the actual pressure. It is essential for maintaining consistency and reliability in pressure measurements. Consistent calibration enhances the quality of data collected which supports decision-making processes in critical environments. Moreover, calibration helps comply with standards and regulations. This reduces liability risks and ensures accountability. Accurate calibrations also prolong the lifespan of measuring equipment and reduce maintenance costs over time.
Methods of Calibration
Calibration can be performed using different methods, each with unique characteristics that suit various applications.
Deadweight Tester
A deadweight tester is a popular calibration device. It uses known weights to create a specific pressure. The primary goal of this method is to provide highly accurate calibration. The key characteristic of a deadweight tester is its ability to generate primary pressure standards. This makes it a foundational tool in the field.
One unique feature of the deadweight tester is its simplicity. It operates on gravitational force, eliminating many variables affecting precision. The advantage of this method is its high accuracy and repeatability, making it a go-to choice for laboratories and industries requiring stringent calibration standards. However, it can be limited by the range of pressures it can test and the requirement for meticulous setup.
Comparative Calibration
Comparative calibration involves comparing the output of a test instrument to a reference standard. This method is effective for verifying multiple instruments efficiently. The major strength of this approach lies in its flexibility. It can be implemented in situ, which can save time and resources.
This method uniquely allows for quick adjustments based on real-time data. The advantage is that it accommodates a wider range of instruments and does not require a lot of specialized equipment. On the downside, comparative calibration can introduce uncertainties due to errors in the reference standard, making it less reliable when extreme accuracy is required.
Challenges in Calibration
Calibrating pressure instruments is not without difficulties. Measurement uncertainty is a prominent challenge. Even the most advanced instruments can have inherent inaccuracies. Environmental influences, such as temperature fluctuations and humidity, can also affect calibration results. Therefore, understanding and managing these challenges is crucial for obtaining valid data.
Pressure Measurement Applications
Pressure measurement applications play a pivotal role across various domains, impacting efficiency and safety in numerous industries. The precise measurement of pressure is vital not only for maintaining optimal operational conditions but also for meeting regulatory compliance and ensuring safety standards. Understanding these applications provides insights into how pressure instrumentation integrates into practical scenarios.
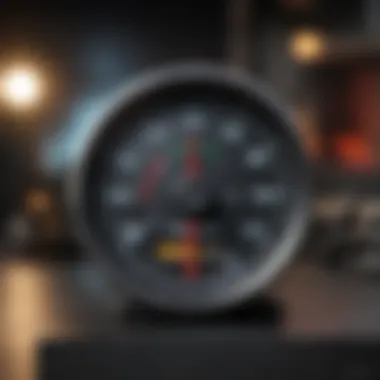
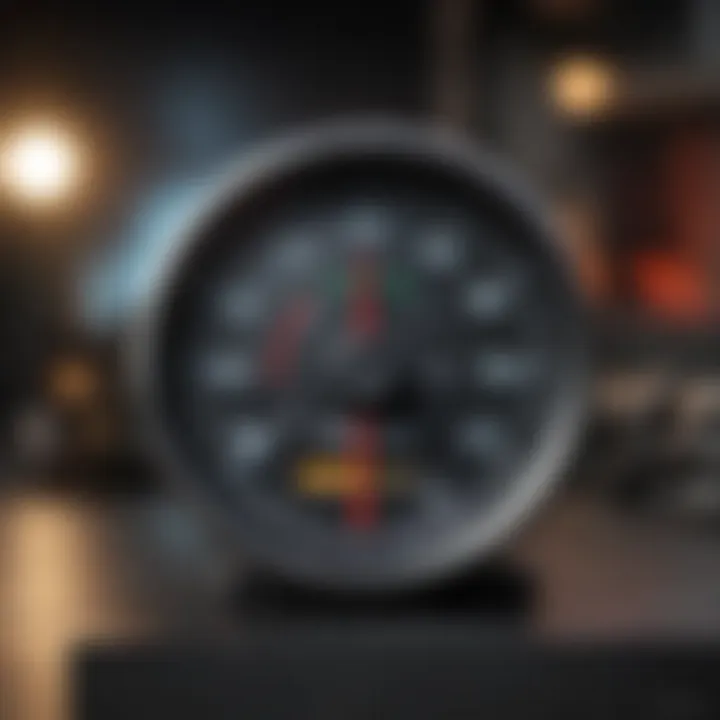
Industrial Applications
Oil and Gas
In the oil and gas industry, pressure measurement is crucial for the extraction and transportation of resources. Accurate pressure readings can help optimize extraction methods and enhance safety during drilling operations. The key characteristic of pressure instrumentation in this sector is its ability to operate in extreme conditions, including high pressure and temperature.
The unique challenge here is ensuring the reliability of sensors used in harsh environments. This resilience is what makes oil and gas applications a significant focus in the study of pressure instrumentation. However, it is essential to consider that inaccurate pressure readings can lead to catastrophic failures, posing environmental risks and operational safety issues.
Chemical Processing
In chemical processing, accurate pressure measurement is imperative for maintaining consistent product quality and ensuring chemical reactions occur within safe limits. This sector often employs pressure sensors that can withstand corrosive substances. The main characteristic here is the need for sensors that not only provide accuracy but also durability.
Chemical processing can greatly benefit from advanced pressure measurement technologies, which can reduce operational costs and minimize waste production. However, one disadvantage is the potential for sensor fouling or degradation over time, which may impact measurement accuracy.
Aerospace and Automotive Applications
Engine Monitoring
Engine monitoring systems rely heavily on accurate pressure measurement to ensure optimal performance and safety. Instruments that provide real-time pressure data can significantly contribute to preventing engine failures. One of the key characteristics of this application is the need for immediate response data, which enhances decision-making processes.
This integration of pressure measurement into engine designs plays a vital role in improving fuel efficiency and performance. A drawback, however, can be the complexity of the systems, which may require specialized knowledge for maintenance and troubleshooting.
Flight Control Systems
In aviation, pressure sensors are integral to maintaining the functionality of flight control systems. Accurate pressure readings inform pilots and automated systems about airspeed and altitude, among other critical data. The key aspect of flight control systems is their reliance on real-time data to maintain aircraft stability.
These sensors help to improve the overall safety of flight operations. On the downside, dependency on electronic systems can create vulnerabilities in case of malfunctions, which place added importance on regular checks and maintenance.
Medical Applications
Blood Pressure Monitoring
In the medical field, blood pressure monitoring stands out as a critical area for pressure measurement. Accurate readings are essential for diagnosing various health conditions and determining treatment plans. The key characteristic here is the correlation between precise pressure measurements and patient outcomes.
The technology used for blood pressure monitoring has evolved significantly, allowing for non-invasive, continuous measurements. However, cost and accessibility can be a concern in some healthcare settings, limiting widespread implementation.
Respiratory Systems
Pressure sensors are similarly crucial in respiratory systems, where they help ensure appropriate airflow and pressure levels for patients relying on ventilators. The main focus is on patient safety during mechanical ventilation, which emphasizes the need for reliable and accurate pressure readings.
The unique feature of this application is its direct impact on critical patient care. Nonetheless, reliance on technology introduces risks, including equipment failure that can lead to serious health outcomes.
Technological Advancements in Pressure Instrumentation
Technological advancements in pressure instrumentation play a crucial role in enhancing precision, efficiency, and versatility in various applications. As industries evolve, the demand for more reliable and accurate pressure measurement systems continues to grow. This section will explore several key advancements that have significantly impacted this field, which includes smart pressure sensors, wireless pressure measurement, and the integration with the Internet of Things (IoT).
Smart Pressure Sensors
Smart pressure sensors are an innovative leap forward in pressure measurement technology. These sensors incorporate digital signal processing and advanced algorithms to provide enhanced accuracy and real-time data analysis. They also come equipped with features like self-diagnostics and calibration capabilities, which increase reliability.
Benefits of Smart Pressure Sensors:
- Increased Accuracy: They offer better precision than traditional sensors, reducing the margin for error.
- Real-Time Monitoring: Smart sensors provide continuous updates, allowing for immediate error detection.
- Data Logging: They can store historical data, enabling trend analysis and predictive maintenance.
The use of smart pressure sensors is particularly beneficial in industries such as oil and gas, where operational safety is paramount. By utilizing these advanced technologies, companies can optimize system performance and predict equipment failures before they occur.
Wireless Pressure Measurement
Wireless pressure measurement systems are transforming how data is transmitted in pressure instrumentation. These systems eliminate the need for extensive cabling, offering flexibility in sensor placement and ease of installation.
Considerations for Wireless Systems:
- Signal Integrity: With wireless systems, concern for signal interference and data loss is essential. Employing robust communication protocols can mitigate this issue.
- Battery Life: As many wireless sensors operate on batteries, energy efficiency becomes a significant factor. Advanced batteries and energy harvesting technologies extend operational life.
- Security: Ensuring data security is critical. Integration of encryption protocols secures transmitted information against unauthorized access.
The ability to measure pressure without physical connections simplifies the process and reduces costs. Industries such as manufacturing and pharmaceuticals benefit from the flexibility of wireless solutions, allowing for rapid setup and reconfiguration.
Integration with Internet of Things (IoT)
The integration of pressure instrumentation with the Internet of Things represents a paradigm shift in data accessibility and analysis. This connectivity enables real-time data management and enhances decision-making processes.
Impact of IoT Integration:
- Remote Monitoring: Users can monitor pressure measurements from anywhere, leading to quicker responses to potential issues.
- Big Data Analytics: Gathering large amounts of pressure data allows for advanced analytics, helping in forecasting and trend prediction.
- Interoperability: IoT devices can interact with other systems, improving coordination across different operational areas.
"The integration of IoT in pressure instrumentation not only provides immediate access to data but also fosters innovation in how industries approach operational efficiency."
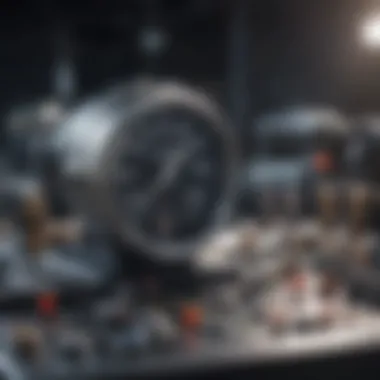
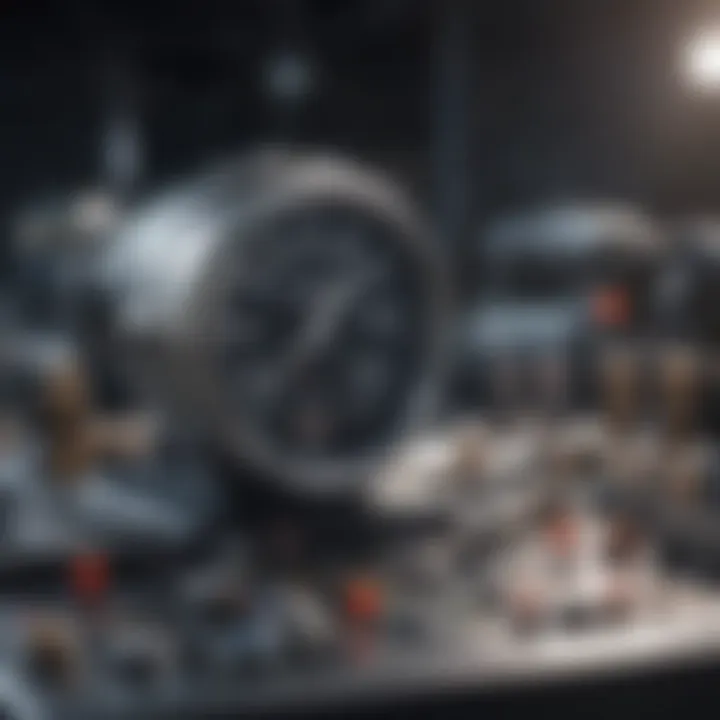
As pressure measurement systems adapt to these technological changes, industries will be better equipped to face challenges, improve safety, and enhance productivity. Emphasizing advancements in smart sensors, wireless capabilities, and IoT integration paves the way for a future characterized by innovation and improved measurement systems.
Future Trends in Pressure Instrumentation
Understanding future trends in pressure instrumentation is crucial for both academic researchers and industry practitioners. As technologies evolve, there are significant changes in how pressure measurements are taken and utilized. Innovations could enhance efficiency, accuracy, and reliability in various applications, from industrial processes to medical diagnostics. This section discusses key elements shaping the future of pressure instrumentation, along with the benefits and considerations associated with these trends.
Emerging Materials and Technologies
The development of new materials plays an essential role in advancing pressure instrumentation. Considerable research is focusing on materials that provide better durability and resistance to extreme conditions. For example, advanced composites and nanomaterials could lead to more sensitive pressure sensors with enhanced performance.
New technologies, such as microelectromechanical systems (MEMS), are also revolutionizing the field. MEMS devices can integrate pressure sensing capabilities within compact designs, enabling miniaturization. This can lead to their use in more applications, such as wearables or smart devices.
Key Points:
- Advanced materials increase sensor lifespan.
- MEMS technology enables smaller and more accurate devices.
- Various innovations could enhance overall system performance.
Regulatory and Compliance Standards
As pressure instrumentation evolves, complying with regulatory standards is becoming increasingly complex. Organizations face the challenge of meeting strict guidelines for accuracy and safety. Regulatory bodies often update their standards to reflect the latest technological advancements. Therefore, keeping abreast of these updates is essential for manufacturers and users.
Moreover, standardizing pressure sensors across industries can lead to consistency. A uniform approach helps ensure interoperability of devices. Organizations such as the International Organization for Standardization (ISO) provide crucial frameworks to help industries navigate compliance requirements effectively.
Considerations:
- Regular updates to standards can impact device design.
- Compliance can enhance trust among consumers and industries.
- Collaboration with regulatory bodies is crucial for development.
Impact of Artificial Intelligence and Machine Learning
The integration of artificial intelligence (AI) and machine learning in pressure instrumentation presents exciting prospects. These technologies can analyze vast datasets from pressure measurements to optimize systems. For instance, predictive analytics can identify potential issues before they escalate into failures, ultimately enhancing safety.
In addition, AI can improve calibration processes by making them more efficient. Algorithms can learn from previous calibrations and reduce the need for manual intervention, thus minimizing human error. Machine learning might also enable more adaptive sensors that fine-tune their responses based on changing conditions.
"Artificial intelligence and machine learning will redefine accurate monitoring in pressure instrumentation."
Benefits:
- Enhanced predictive maintenance capabilities.
- More efficient calibration processes.
- Adaptive sensors for real-time performance improvements.
Challenges in Pressure Instrumentation
Understanding the challenges in pressure instrumentation is crucial for anyone engaged in the field. This section addresses key elements that affect the accuracy and reliability of pressure measurements. With industries relying heavily on precise data, the implications of such challenges can be significant.
Measurement accuracy is one of the foremost concerns in this area. Various factors can introduce uncertainty into readings. Consequently, a thorough grasp on measurement uncertainty is vital. By identifying the sources of error, professionals can enhance their instruments or calibration methods. This approach can minimize discrepancies in pressure readings.
Measurement Uncertainty
Measurement uncertainty refers to the doubt that exists regarding the result of a measurement. It encompasses various sources of error, including instrument calibration, environmental conditions, and resolution limitations. For example, an improperly calibrated gauge can yield readings that diverge from the true value.
Specific factors that contribute to measurement uncertainty include:
- Instrument precision: The resolution of an instrument can either limit or enhance the observation of small pressure changes. High-quality devices usually offer better precision.
- Environmental impact: Temperature fluctuations can impact sensor behavior, leading to inaccurate readings.
- Operator error: User interaction with instruments also plays a role. Misreading or misunderstanding measurement protocols can skew results.
"Accurate pressure measurement is not just about advanced instruments; it requires an understanding of the factors contributing to uncertainty."
Environmental Influences on Pressure Measurement
Environmental factors profoundly influence the performance of pressure instruments. Variations in temperature, humidity, and altitude can alter the characteristics of the sensing technology.
- Temperature variations: High or low temperatures can cause sensor components to expand or contract. This mechanical change affects the pressure measurement accuracy.
- Humidity effects: Excess moisture can impair electronic components. This degradation may lead to false readings or even complete instrument failure.
- Altitude: As altitude changes, atmospheric pressure levels also fluctuate. Instruments must be adjusted or specified for use in different elevations to maintain accuracy.
Epilogue
The conclusion of this article serves as a crucial component, synthesizing the diverse topics and insights we've explored. Pressure instrumentation is not merely a technical subject; it holds significant implications across various industries and applications. As we have seen, the measures of pressure are fundamental to not only maintaining safety standards but also to enhancing efficiency and effectiveness in processes ranging from industrial operations to medical monitoring.
In summation:
- Key Insights: The intricate relationship between pressure measurement technologies and their specific applications showcases how nuanced and essential this study is. Knowing the differences between types of pressure sensors and their calibration methods can lead to significant improvements in operational reliability.
- Future Directions: The exploration of emerging technologies, especially those integrating artificial intelligence and smart systems, highlights the potential for innovation within the field.
Summary of Key Insights
Throughout the article, we have outlined several essential points regarding pressure instrumentation. Firstly, the distinction between absolute, gauge, and differential pressure cannot be overstated. Each type serves different applications and contexts, making it imperative for professionals in the field to choose appropriately. Secondly, we have examined various pressure sensors. Mechanical sensors like the Bourdon Gauge and regulators play a significant role alongside electronic sensors like piezoelectric and strain gauge sensors.
Moreover, calibration techniques are fundamental to ensure precision in measurements, with methods like the deadweight tester providing reliable benchmarks.
"Accurate pressure measurement is a cornerstone of effective control in many systems, influencing outcomes across industries."
The advances in wireless sensors and their integration with the Internet of Things (IoT) represent transformative trends. These developments promise enhanced data acquisition and analytics capabilities that can drive proactive decision-making in real-time.
Future Directions for Research
Looking ahead, research in pressure instrumentation should focus on several promising areas. One key aspect would be the study of new materials capable of improving sensor durability and sensitivity. Materials science can revolutionize the capabilities of sensors in extreme conditions. Another important area is the enhancement of calibration techniques to minimize measurement uncertainties, especially in critical applications.
Regulatory frameworks will also evolve, necessitating continued research to ensure compliance standards are met without compromising innovation. Furthermore, delving into the intersection of AI and machine learning with pressure instrumentation can lead to groundbreaking capabilities, such as predictive maintenance and automated adjustments based on real-time data analytics.
By addressing these points, future research efforts can lead to more efficient and reliable pressure measurement solutions, ultimately benefiting a multitude of sectors.