Exploring the Complexities of Glass Production
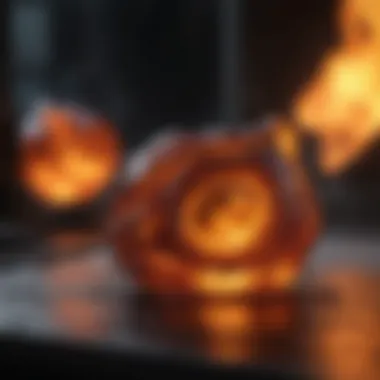
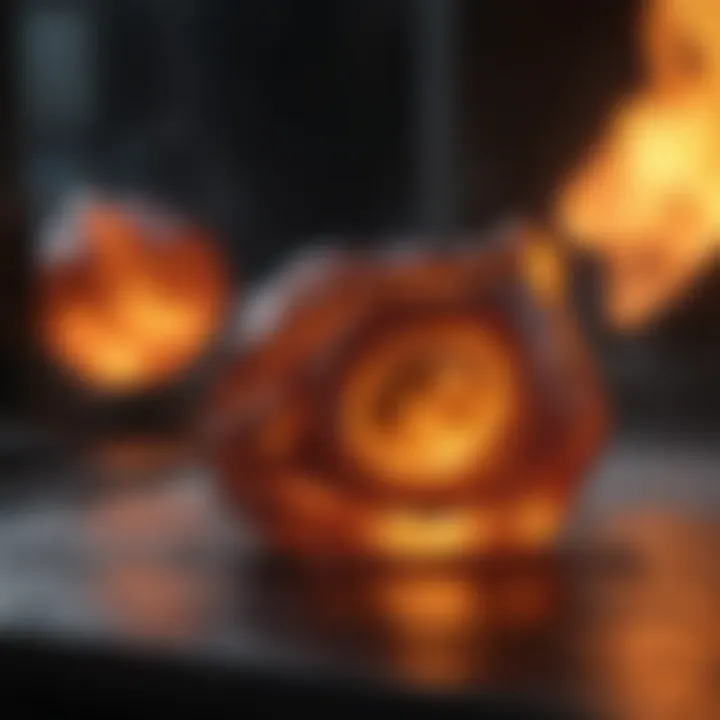
Intro
The production of glass is a fascinating blend of artistry and rigorous scientific principles. It intertwines ancient techniques with modern innovations, painting a picture that extends far beyond mere material crafting. Understanding glass production is crucial not just for artisans and manufacturers but also for anyone who appreciates its various applications—from architecture to art.
As we peel back the layers of this craft, we discover the intricacies involved in sourcing the raw materials, the heat-driven processes of shaping glass, and the chemical reactions that define its properties. With the glass industry evolving under the demands of sustainability and technological advancement, getting acquainted with this field provides an enlightening glimpse into how human creativity and scientific inquiry collide.
Research Overview
Key Findings
In the examination of modern glass production methods, several key findings emerge:
- Material Selection: The choice of raw materials significantly influences the quality and characteristics of the glass produced. Silica sand remains fundamental, yet recycled glass, known as cullet, is becoming increasingly predominant due to its economic and environmental benefits.
- Production Techniques: Advanced techniques such as float glass manufacturing and glass blowing show how traditional methods adapt to meet contemporary needs while maintaining the artistry of the craft.
- Environmental Considerations: There is a rising awareness concerning the ecological footprint of glass manufacturing processes, resulting in innovations aimed at reducing waste and enhancing energy efficiency.
Study Methodology
To gather insights into the field of glass production, the following methods were employed:
- Literature Review: Extensive research was conducted through academic journals and articles on glass science and production techniques.
- Interviews with Experts: Feedback from industry professionals and glass artists helped to bridge the gap between practical application and theoretical knowledge.
- Field Observations: Visits to glass production facilities provided firsthand experience of the mechanisms and environmental practices in action.
Background and Context
Historical Background
The journey of glass production dates back thousands of years, initially crafted in Mesopotamia around 3500 BCE. Over the centuries, artistic styles and techniques have evolved, influenced by cultural shifts and the expansion of trade routes. In ancient Egypt, glass was regarded as a luxury item and often used in decorative objects. The art of glassblowing emerged in the first century BC, representing a significant technological advancement that enabled the creation of thinner, more intricate glass forms.
Current Trends in the Field
Today, the glass industry is witnessing a combination of innovation and revival of traditional practices. Key trends include:
- Sustainable Practices: Many manufacturers are incorporating recycled glass into their production. This not only reduces landfill waste but also lowers energy consumption during the melting process.
- Smart Glass: The rise of smart glass technologies that can change properties based on environmental factors indicates a fusion of glass production with cutting-edge technology. These developments promise new applications, particularly in architecture and automotive industries.
- Artistic Collaborations: Contemporary artists are increasingly using glass as a medium for expression, pushing the boundaries of form and function, often delving into themes of fragility and permanence.
"Glassmaking is truly a dance between the elements—fire transforms sand into liquid, and skilled hands fashion it into works of infinite variety."
Prelims to Glass Production
Glass has been an integral part of human civilization for millennia. Its versatility and beauty make it an essential material, found everywhere from windows and bottles to intricate art pieces. Understanding the art and science behind glass production involves more than just knowing how it’s made; it requires an appreciation of its historical significance and its pervasive role in modern society.
Historical Context
The origins of glass production date back to ancient Mesopotamia and Egypt, where artisans first experimented with heating silica with soda. Over the centuries, different cultures enhanced techniques and introduced innovations. The Romans, for instance, mastered glassblowing, transforming the craft and making glassware accessible to the masses. This period marked a significant shift from primarily ornamental glass to practical applications, demonstrating glass’s potential usefulness in everyday life.
"Glass is a metaphor for clarity, transparency, and reflection of life itself."
In the Middle Ages, glass production was further revolutionized in Venice, where Murano Island became synonymous with exquisite glass craftsmanship. The techniques developed during this era still influence modern methods. Today, historical glass pieces fetch high prices at auctions, not just as art but as tokens of human ingenuity.
Importance of Glass in Modern Society
Fast forward to the present day, and glass has firmly established itself in a variety of essential applications. Its role in architecture, for instance, cannot be overstated. Skyscrapers dotted with glass facades reflect advancements in engineering and aesthetic values, providing natural light while minimizing energy consumption.
In the technology sector, glass is indispensable. Think of the screens on smartphones and computers. They're not just components; they are gateways to our digital lives, enabling connectivity and interaction.
There are also environmental factors at play. The recycling of glass is a critical process in sustainability efforts. It reduces the need for raw materials, conserves energy, and minimizes waste. According to estimates, recycling a single ton of glass can save over a ton of raw materials, paving the way for a more sustainable future.
In summary, glass production is not merely an industrial process; it represents a fusion of art, science, technology, and history. As we dive deeper into this complex world throughout this article, the relevance of glass becomes increasingly apparent—not just as a material, but as a key player in our daily lives.
Raw Materials in Glassmaking
Understanding the raw materials used in glassmaking is key to grasping the entire production process. Each of these materials contributes distinct properties that define not only the characteristics of the glass but also influence its applications, cost, and sustainability. This section will delve into the core materials essential for creating glass, as well as their roles, benefits, and potential drawbacks.
Silica Sand
Silica sand, mainly composed of silicon dioxide (SiO2), serves as the primary ingredient for all glass types. Its purity and grain size play critical roles in determining the clarity and quality of the final product. In glass production, silica sand functions as the backbone of the glass structure, providing the necessary framework to ensure strength and durability. Without high-quality silica sand, the integrity of the glass may be compromised.
One notable characteristic of silica sand is its high melting point, approximately 1,700 degrees Celsius. This requires significant energy consumption, making the choice of silica crucial not just for the glass's properties but also for its environmental impact during production. Moreover, silica sand sourcing can also pose ecological challenges if not done sustainably. In light of this, finding ways to minimize energy use and sourcing responsibly could enhance the sustainability of glassmaking.
Fluxing Agents
Fluxing agents lower the melting point of silica, making the glass production process more energy-efficient. Two common fluxing agents are soda ash and potash, each contributing differently to the glass's final quality.
Soda Ash
Soda ash, or sodium carbonate, is widely recognized for its effectiveness as a fluxing agent. Its addition to the batch composition significantly reduces the melting temperature of silicate materials to around 1,400 degrees Celsius, allowing for a more manageable and energy-efficient melting process. Additionally, soda ash helps improve the glass's workability during forming processes.
However, soda ash is hygroscopic, meaning it readily absorbs moisture from the atmosphere. This property can lead to challenges during storage and mixing, making it imperative to handle soda ash with care to avoid clumping or premature reaction during production. The balance of soda ash in the batch is vital as excessive amounts can lead to glass degradation and weakened physical properties.
Potash
Potash, or potassium carbonate, also serves as a flux but brings unique benefits to the glassmaking table. Its primary role is to improve the thermal and chemical durability of glass products. Potash yields a glass that is less prone to devitrification, a process where glass crystals form during cooling, potentially ruining the clarity and strength.
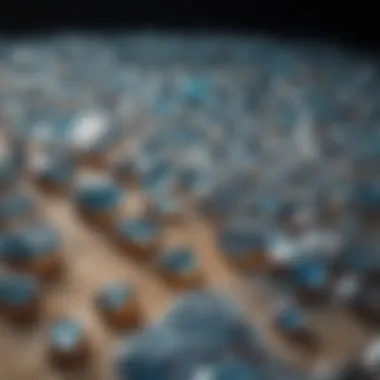
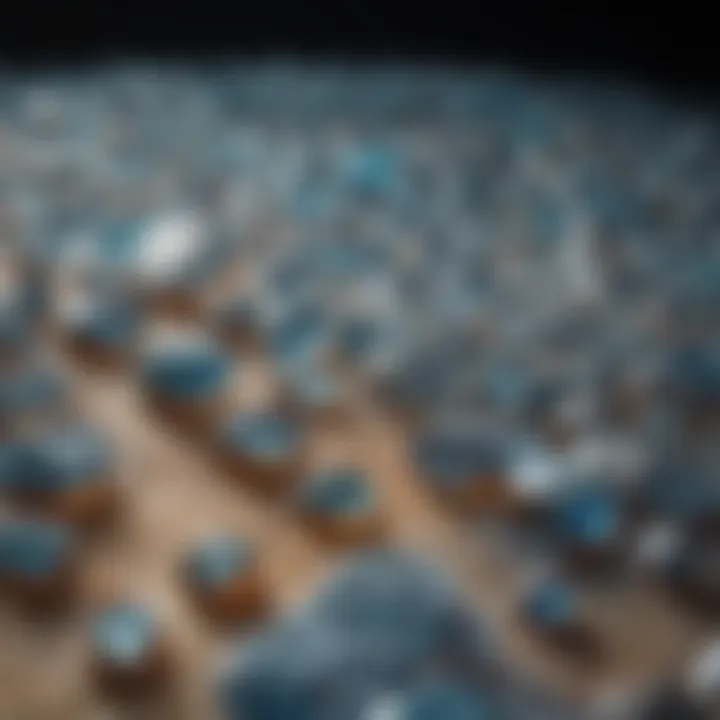
Due to its less common usage than soda ash, potash can contribute to a higher production cost, making its application more selective. Yet, the enhanced durability attributes make it a favorable choice for specialized applications, like certain decorative and technical glasses. The careful selection of potash allows glassmakers to meet precise product specifications while ensuring performance under various conditions.
Stabilizers
Stabilizers play an essential role in defining the chemical resistance and stability of glass products. Calcium oxide and barium oxide are two common stabilizers that find their way into many formulations.
Calcium Oxide
Calcium oxide functions as an indispensable stabilizer in many glass applications. This compound binds well with silicates and helps enhance the chemical durability of the glass. A particularly important feature of calcium oxide is its ability to mitigate the solubility of glass in water, thereby resulting in improved longevity and usage in various environments.
However, calcium oxide can contribute to increased viscosity during the melting process, requiring careful balancing with network formers to achieve optimal workability. Despite this, its cost-effectiveness makes it a staple in many manufacturing processes.
Barium Oxide
Barium oxide boasts impressive optical properties, making it highly sought after for optical glass production. One key characteristic is its ability to increase the refractive index of glass, allowing it to bend light more effectively. This makes barium oxide a popular choice for lenses and prisms.
On the downside, barium is less abundant and can be more expensive than other stabilizers, leading to increased production costs. Nonetheless, its unique features justify its use in high-end optical applications, where performance is paramount.
"The properties of the materials used in glass production not only influence the final product but also reflect the challenges and innovations present in the industry."
Overall, the selection of raw materials in glassmaking is a delicate balancing act, where each ingredient must be chosen for its specific characteristics and advantages, while also considering the environmental implications and economic factors at play.
The Glass-Making Process
The art of glassmaking is not merely a craft; it is a fusion of precision and creativity, where each step in the glass-making process plays a significant role in determining the final product's quality. Understanding this intricate process is crucial for anyone interested in glass production, whether for artistic endeavors or industrial applications. The glass-making process is a dance between raw materials, heat, and technique, yielding a versatile material seen in a myriad of applications today.
In essence, the process can be broken down into three main stages: batch preparation, melting the batch, and forming techniques. Each step interconnects, ensuring that the glass produced is not only functional but also aesthetically pleasing. Let's delve deeper into each of these sections to grasp the complexities involved in glass production.
Batch Preparation
Batch preparation is the initial stage in glass-making, where the raw materials are gathered and measured with pinpoint accuracy. This may sound simple, but it lays the groundwork for the entire process. If you think of glassmaking like baking a cake, this step equates to gathering all your ingredients, ensuring you have the right measurements before tossing them in the oven.
In this stage, silica sand is usually the star ingredient, accompanied by fluxing agents like soda ash and stabilizers such as calcium oxide. The proportions of these components must be carefully calculated since even the slightest deviation can lead to imperfections in the glass.
Melting the Batch
Once everything's in place, the mixture is ready for the furnace. Melting is perhaps the most critical phase of glass production, as it transforms the raw materials into molten glass.
Furnace Types
Various furnace types are used in glass production, each with its characteristics and advantages. The most common varieties include tank furnaces, pot furnaces, and crucible furnaces.
Tank furnaces are particularly popular due to their ability to handle large volumes of glass continuously, making them efficient for industrial-scale production. A unique feature of tank furnaces is their design, which allows for a consistent melting environment. However, they require significant energy input, posing an environmental concern.
Pot furnaces are smaller and offer more flexibility, often favored by artisans creating specialized glass pieces. Their compact size allows easy temperature control, yet they are limited in the volume of glass they can produce at one time.
Temperature Control
Temperature control during melting is a crucial factor that influences the quality of the glass. Maintaining the right temperature is key, as it ensures that the materials completely melt and interact properly. Too high a temperature might lead to bubbling, while too low could leave unmelted particles in the glass.
In modern glass production, sophisticated sensors and control systems enable precise monitoring of temperature fluctuations, ensuring that the desired properties of the glass, such as clarity and strength, are achieved consistently.
Forming Techniques
With the molten glass ready, the next step is forming, where creativity and technique come into play.
Blowing
Blowing is one of the oldest techniques in glass-making, allowing artisans to create unique shapes and designs by inflating molten glass into a bubble. This method is valued for its versatility, as it can produce everything from delicate ornaments to large sculptural pieces. The unique characteristic of blowing lies in the skill required to manipulate the glass bubble into the desired form, making it a favored choice for custom artworks. However, mastering this technique can take years of practice, presenting a steep learning curve for new artisans.
Molding
Molding is another prevalent forming technique. This process involves pouring molten glass into a predefined mold, resulting in uniform shapes and sizes. The key characteristic of molding is its efficiency; large quantities of glass products can be made quickly, making it advantageous for mass production. However, the limitation here is that it lacks the unique touch often seen in blown glass, leading to products that can feel less personal or artisanal.
Drawing
Lastly, drawing techniques involve pulling molten glass into strands or sheets, a common method used for manufacturing glass fiber used in several industries. The key feature of drawing is flexibility in the final product, providing a lightweight yet durable material. However, it does require precise control over speed and temperature during the pulling process, making it resource-intensive.
Finishing and Annealing
In the world of glass production, finishing and annealing play a pivotal role in ensuring the quality and durability of glass products. These processes are not merely afterthoughts but integral steps that can make or break the final product. After all, a beautiful piece of glass that cracks or breaks easily is not a satisfactory outcome, and that's where the finesse of these stages comes into play.
Surface Treatments
Polishing
Polishing glass is an art form that enhances the visual appeal of the final product. This process involves smoothing the surface through various methods, often using finer abrasives that bring out the material's inherent luster. The key characteristic of polishing is its ability to create a crystal-clear finish that not only looks stunning but also reduces abrasion effects. This makes it a popular choice among glass artisans and manufacturers.
The unique feature of polishing is that it can also improve the glass’s functionality. For example, in optical glass production, polished surfaces minimize distortion and light loss, ensuring high clarity. However, it is worth noting that over-polishing can lead to a compromised edge, making the glass more vulnerable to breakage.
Coating
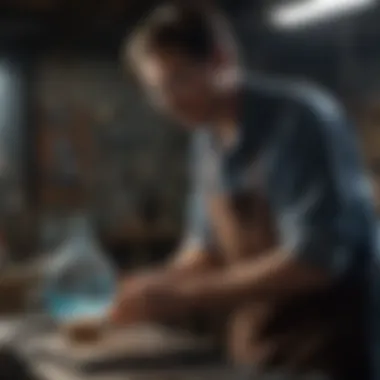
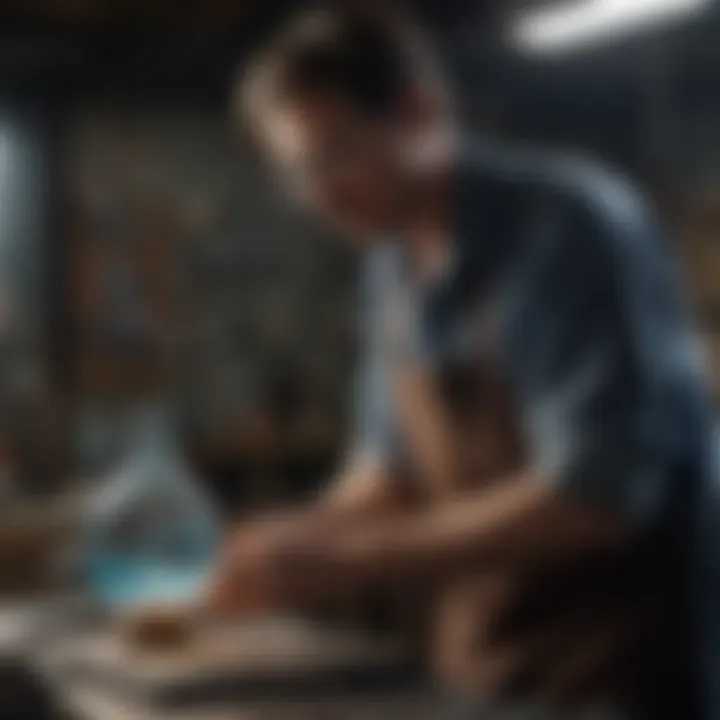
Coating is another essential surface treatment in glass production, designed to enhance the material's durability and appearance. This process often involves applying a layer of protective or decorative material on the glass surface. The critical characteristic of coating lies in its versatility; it can be tailored for various applications, from anti-reflective coatings in optical glass to tinted surfaces in architectural applications.
A unique feature of coating is that it can significantly improve the glass's resistance to scratches and environmental factors. However, there are disadvantages too, such as potential issues with adhesion over time or compromises in transparency. Despite these concerns, the benefits it brings often outweigh the drawbacks, making it a valued method in glass manufacturing.
Annealing Process
Purpose of Annealing
The purpose of annealing in glass production cannot be overstated. This heating and cooling process helps relieve internal stresses that develop during the glass-forming processes. Essentially, it allows the glass to cool uniformly, reducing the chances of thermal shock and subsequent cracking. A significant benefit of annealing is its effectiveness in enhancing the overall strength and longevity of the end product.
This practice is crucial, especially for glass items that will experience sudden temperature changes. The unique feature of annealing is that it introduces a controlled cooling phase, which is vital for maintaining the integrity of the glass structure. The drawback, however, is that it requires careful management of time and temperature, as improper conditions can lead to uneven results.
Temperature Profiles
Temperature profiles during the annealing process are critical in determining the success of this stage. These profiles dictate how quickly glass can cool down while maintaining structural integrity. A consistent temperature profile translates to fewer defects in the finished product, ensuring that the glass will be durable enough for its intended use.
The key characteristic of temperature profiles is their relationship with glass thickness and type. Each glass composition requires different cooling rates, making it essential to customize the profiles accordingly. This attention to detail ensures that the desired thermal properties are achieved without compromising quality. However, if not managed well, variations in these profiles can lead to increased wastage and lower overall production efficiency.
"Finishing and annealing are not just steps; they are the quiet heroes in the world of glass production that often go unnoticed but are fundamental to creating quality products that stand the test of time."
Thus, finishing and annealing are indispensable parts of glass production that not only enhance aesthetic value but also contribute significantly to the durability and functionality of glass items.
Quality Control in Glass Production
Quality control in glass production represents a pivotal aspect of the manufacturing process, ensuring that the final product meets established standards and specifications. This area is not merely an afterthought; rather, it is a fundamental component that intertwines with every stage of glass production, from selecting raw materials to the end-user applications. By maintaining rigorous quality control protocols, manufacturers can reduce defects, enhance product performance, and cultivate consumer trust.
Testing Techniques
Visual Inspection
Visual inspection, as a testing technique, holds a prominent position due to its immediacy and practicality. This method enables operators to quickly evaluate the surface quality, clarity, and general aesthetic of glass products. Key characteristics of visual inspection include its simplicity and low cost, which make it a popular choice in many manufacturing settings.
"In glass production, the eyes of the examiner can catch discrepancies that machines might overlook."
A significant advantage of visual inspection lies in its ability to detect surface imperfections like scratches, bubbles, and color inconsistencies at an early stage. However, it is not without its disadvantages; the effectiveness of this method can be heavily influenced by the human factor, potentially introducing variability due to subjective interpretations. As such, while visual inspection is invaluable for initial assessments, relying solely on this method may lead to oversight in quality assurance.
Mechanical Testing
Mechanical testing adds another layer of rigor to the quality control process. This technique is used to evaluate the physical properties of glass, such as strength and elasticity. Among its key characteristics, mechanical testing provides quantitative data that can validate the performance specifications needed for specific applications.
As a beneficial method, mechanical testing allows for an objective assessment of material properties, thus providing essential insights into how the glass will perform under stress or load. Unique features of this testing technique include utilizing standardized methods like tensile tests and impact resistance assays to predict real-life behavior of the product.
Nevertheless, mechanical testing does come with its downsides. The requirement for specialized equipment, along with comprehensive training for accurate interpretation of results, can represent substantial investments for manufacturers. Weighing these pros and cons is essential when designing an effective quality control framework.
Impact of Quality on Applications
The quality of glass directly influences its suitability for a variety of applications. For example, architectural glass must not only boast aesthetic appeal but also functional durability. Meanwhile, optical glass used in lenses demands a higher level of precision and clarity. The impact of quality is particularly pronounced in the safety glass sector, where lapses in quality can lead to catastrophic failures.
Maintaining stringent quality control dictates the positioning of glass in both everyday consumer products and specialized industrial uses. Whether it's ensuring flawless windows or high-definition screens, excellence in quality bolsters performance and longevity. The relationship between quality management processes and application effectiveness cannot be overstated; as glass technology advances, the expectations for quality will only escalate, pressuring manufacturers to evolve alongside the demands of their markets.
Innovations in Glass Manufacturing
Innovations in glass manufacturing play a crucial role in redefining the boundaries of what can be achieved in this age-old craft. As industry demands evolve, the push for efficiency, sustainability, and creativity becomes paramount. This section explores groundbreaking advancements that not only enhance production capabilities but also address environmental concerns associated with glass production.
Emerging Technologies
3D Printing of Glass
3D printing of glass is a fascinating frontier in glass manufacturing. It allows for the creation of complex designs that were previously difficult, if not impossible, to achieve through traditional methods. What sets this technology apart is its ability to produce intricate geometries with minimal waste, a critical point in an industry often criticized for its resource consumption.
The main characteristic of 3D printing of glass is the layer-by-layer approach that closely mimics traditional techniques while offering unparalleled precision. This method is particularly beneficial for artists and designers who seek unique forms, as well as industries requiring customized solutions. A unique feature of this technology is its adaptability; prototypes can be made swiftly, allowing for rapid iterations based on feedback without the long lead times commonly seen in conventional glass production.
However, it isn't all rosy. The technology is still in its infancy and might not yet match the durability and mechanical properties of traditionally manufactured glass, which raises questions about its long-term application in certain fields.
Sustainable Practices
Sustainable practices in glass manufacturing are becoming increasingly important in today's environmentally conscious landscape. The industry is under pressure to adopt practices that not only reduce waste but also lower energy consumption. Utilizing recycled glass is a cornerstone of this effort. By reprocessing cullet, manufacturers can significantly cut down on raw material use, effectively lessening the environmental footprint.
The key characteristic of sustainable practices lies in their focus on resource efficiency and circular economy principles—where industry waste is minimized and materials are reused effectively. This is viewed as a vital choice for businesses looking to enhance their reputations and meet regulatory demands. One unique feature is the use of renewable energy sources in glass furnaces, which can yield substantial reductions in greenhouse gas emissions.
Despite these advantages, challenges remain. The quality and consistency of recycled materials can vary, which may affect the characteristics of the final product. Manufacturers must invest in technology and processes to ensure that quality is maintained.
The Role of Automation
Robotics in Glass Production
Robotics in glass production is transforming the way tasks are performed on the shop floor. Automation not only increases efficiency but also enhances safety by handling hazardous materials or processes that involve intense heat. The standout quality of robotics is their ability to operate with pinpoint accuracy and in harsher conditions than human workers, thus minimizing errors often caused by fatigue or distractions.
Robotics also allow glass manufacturers to streamline processes, from sorting raw materials to managing production lines. However, despite these benefits, integrating robotics requires significant upfront investment, which can be daunting for smaller operations. Additionally, there is a need for skilled workers to maintain and operate such sophisticated systems, raising questions about workforce adaptability.
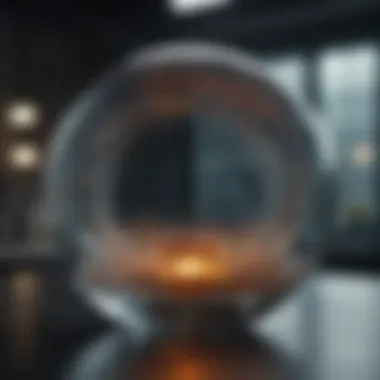
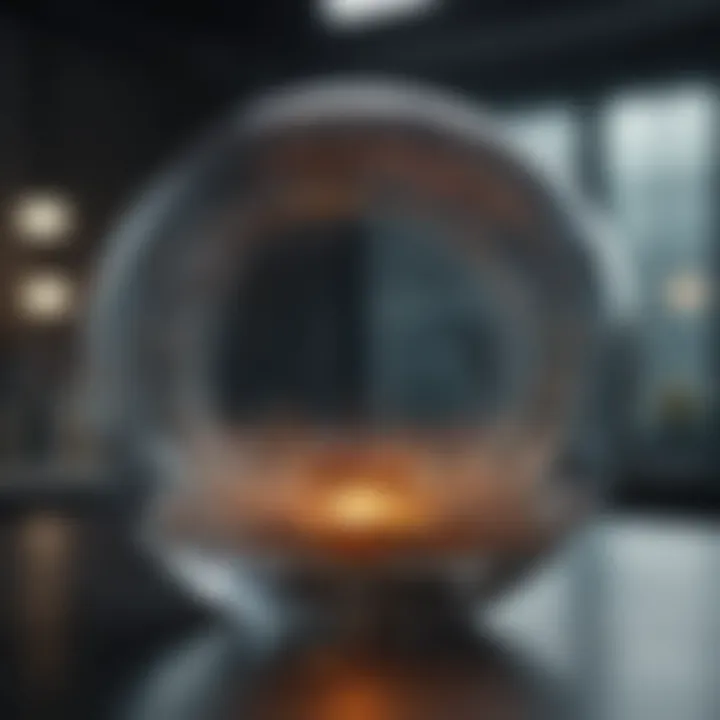
Data Analytics
Data analytics is paving the way for smarter decision-making in glass production. By closely monitoring production processes and analyzing data trends, manufacturers can identify inefficiencies, predict equipment failures, and optimize resource usage. The key characteristic of this approach is its reliance on real-time data, enabling rapid responses to issues that arise during production.
The unique feature of leveraging data analytics is its capacity to provide insights derived from complex data sets that would otherwise remain untapped. Companies that embrace this technology often enjoy lower operational costs and enhanced product quality. However, the downside is that there is a steep learning curve involved. For many manufacturers, adapting their workforce to be data-literate and technologically savvy poses a considerable challenge.
Overall, the innovations in glass manufacturing are not mere conveniences; they represent essential shifts that balance the age-old art of glass making with the demands of modern society.
Environmental Considerations
In an era where sustainability is a pressing concern, the glass production industry stands at a crossroads between demand and environmental responsibility. Glass, known for its durability and recyclability, plays a pivotal role in reducing waste and conserving resources. Understanding the environmental considerations in this sector is not merely an additional layer in glassmaking but an essential facet of its evolution. The push for greener practices continues to shape processes and technologies within this craft.
Energy Consumption
The glass production process is notoriously energy-intensive. Furnaces used for melting raw materials operate at extremely high temperatures, often exceeding 1700 degrees Celsius. This intense heat requires a significant amount of energy, which typically comes from fossil fuels or electricity. With global warming and the need to cut carbon emissions at the forefront of climate discussions, energy consumption in glass manufacturing is a critical point of contention.
Efforts are being directed towards optimizing this consumption through various innovations.
- Alternative Fuels: Some manufacturers are looking into using waste materials as alternative fuels. This practice can reduce dependency on traditional energy sources.
- Energy Recovery Systems: Implementing heat recovery systems allows facilities to utilize residual heat, making overall energy use more efficient.
- Advanced Furnaces: Technological advancements have led to the creation of more efficient furnaces, which can lower energy costs and emissions while still meeting production demands.
Recycling of Glass
Recycling plays a crucial role in mitigating the environmental impact of glass production. The process significantly reduces the need for raw materials, thereby conserving natural resources and reducing transportation emissions. Additionally, recycled glass melts at lower temperatures compared to raw materials, resulting in decreased energy usage during production.
Importance of Recycling
The benefits of recycling glass extend beyond environmental health. It reduces landfill contributions significantly, as glass takes millions of years to decompose. Furthermore, it supports local economies and creates job opportunities in the recycling sector. One key characteristic of recycling is its circular economy model, which emphasizes reuse rather than disposal. This makes recycling an attractive option for responsible production practices in the glass industry.
- Cost Efficiency: Recycling often reduces production costs in the long run by lowering the need for new materials.
- Resource Conservation: Recycling glass minimizes the depletion of silica sand and other raw materials, preserving these resources for future generations.
"Recycling glass is not just good practice; it is a necessity in ensuring sustainability for future generations."
Process of Recycling Glass
The process of recycling glass involves several steps that illustrate the industry’s commitment to sustainability.
- Collection: Glass is collected from various sources, including households and businesses, often sorted by color.
- Cleaning: Contaminants such as labels and caps are removed to ensure purity in recycling.
- Crushing: Clean glass is crushed into small pieces known as cullet, which can be melted and reformed.
- Melting and Remolding: The cullet is melted and reformed into new glass products or containers.
The recycling process not only helps in conserving materials and energy but also reduces waste, making it a win-win for both industry and environment. However, it does come with challenges, such as contamination issues and the need for public awareness on recycling practices. Understanding these hurdles can aid in developing solutions that drive both efficiency and sustainability in glass production.
Applications of Glass
The world of glass extends far beyond mere decorative aesthetics. Its versatility is the backbone of various industries, shaping not just our physical surroundings but also our technological advancements. Exploring the applications of glass gives us insight into its crucial role in architecture, optics, and the arts. Each application not only showcases the material's properties but also highlights how those properties can be harnessed for specific uses.
Architectural Glass
Architectural glass plays a pivotal role in modern building design. It is more than just a physical barrier; it provides natural light, energy efficiency, and even aesthetic value to structures. The benefits of utilizing glass in architecture include:
- Natural Light: Well-placed glass elements can transform dark spaces, reducing reliance on artificial lighting. This helps in conserving energy while creating a more inviting atmosphere.
- Thermal Performance: advancements in coated glass can enhance insulation properties, minimizing heat loss while still allowing brightness inside.
- Aesthetics: Glass surfaces can dramatically change the appearance of buildings, from sleek modern designs to intricate historical facades.
For example, the Burj Khalifa in Dubai showcases how expansive glass surfaces can blend luxury with cutting-edge engineering. Through a strategic combination of glass types and treatments, the building manages to reflect and absorb sunlight effectively, creating a visually stunning effect while maximizing energy efficiency.
Optical Glass
Optical glass is another essential category. Found in lenses, mirrors, and scientific instruments, it has applications that range from simple magnifying glasses to complex optical systems used in telescopes and cameras. The qualities of optical glass include:
- Clarity: High-quality optical glass is designed to minimize distortions and increase light transmission. This is crucial for applications in photography, astronomy, and advanced microscopy.
- Customizability: Manufacturers can alter the refractive index and dispersion to tailor glass for specific functions. A popular example is the Carl Zeiss lenses known for their precision in delivering clear images.
In areas like telecommunications and entertainment, optical fibers made from glass are essential for high-speed data transmission. With demand increasing for high-bandwidth connections, the development of fiber optic technology has changed the way we communicate, highlighting the importance of optical glass in our daily lives.
Art Glass
Art glass encompasses a broad spectrum of decorative and functional pieces, produced primarily for artistic expression rather than practical application. It is renowned for its vibrant colors, unique shapes, and ability to capture light.
- Expression of Identity: Artists use glass as a medium to reflect cultural narratives or personal experiences, often seen in the works of contemporary glass artists like Dale Chihuly, whose installations ignite imagination.
- Techniques: Various techniques, such as fusing, blowing, and casting, allow artists to manipulate glass into stunning forms. Each method brings unique challenges and opportunities, demonstrating the intricate balance between science and technique.
Art glass not only adds beauty to spaces but also encapsulates stories and emotions. From functional items like vases to elaborate sculptures, it illustrates the union of creativity and craftsmanship, proving that glass can transcend its materiality to become a form of emotional communication.
"Glass is all around us; it has a story in every shard and light in every reflection."
In summary, the applications of glass—be it in architecture, optics, or art—reflect its versatility and enduring significance. Each sector leverages glass’s unique properties, contributing to innovations and enhancing our everyday lives.
Ending
In summarizing the vast landscape of glass production, it’s clear that this craft is a critical intersection of art and science. The journey from ancient techniques to modern innovations shows us how deeply imbedded glass is in our daily lives. Its versatility spans numerous applications—from architectural creations that define skylines to finely crafted art pieces that adorn galleries.
When looking ahead, the future of glass production holds significant importance not only for manufacturers but also for environmental advocates. As methods shift towards more sustainable practices, the industry is learning to balance aesthetics with ecological responsibility. This evolution reflects changing consumer preferences and regulatory pressures that demand greener manufacturing processes.
Key elements to consider in the future of glass production include:
- Sustainability Initiatives: Efforts to reduce waste and recycle glass are gaining traction, as more manufacturers recognize the importance of closed-loop systems.
- Technological Advances: Emerging technologies, like 3D printing, are set to revolutionize how glass is produced—potentially leading to faster production while minimizing material wastage.
- Market Trends: Understanding how consumer demand influences glass designs can guide manufacturers to adapt better and create products that meet contemporary needs.
In summary, monitoring trends and developments in glass production not only helps in understanding this art form but also prepares stakeholders for opportunities in a constantly evolving landscape. The craftsmanship of glass is as relevant today as it was centuries ago, and as the future unfolds, it promises not only to enhance our environments but also to foster a greater connection with our natural ecosystem.
"Glass is not just an object; it’s an experience that encapsulates both artistry and practicality, ushering us towards a sustainable future."
As we progress, it’s imperative to keep these considerations in mind and foster innovation that respects both the art of glass production and our planet.