Exploring the Mechanisms of 3D Printing Processes
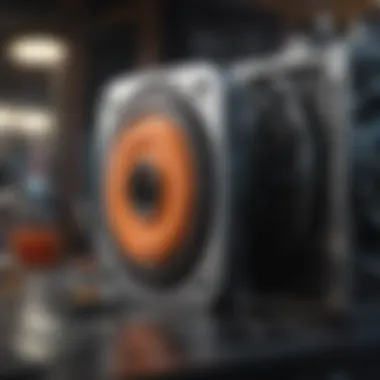
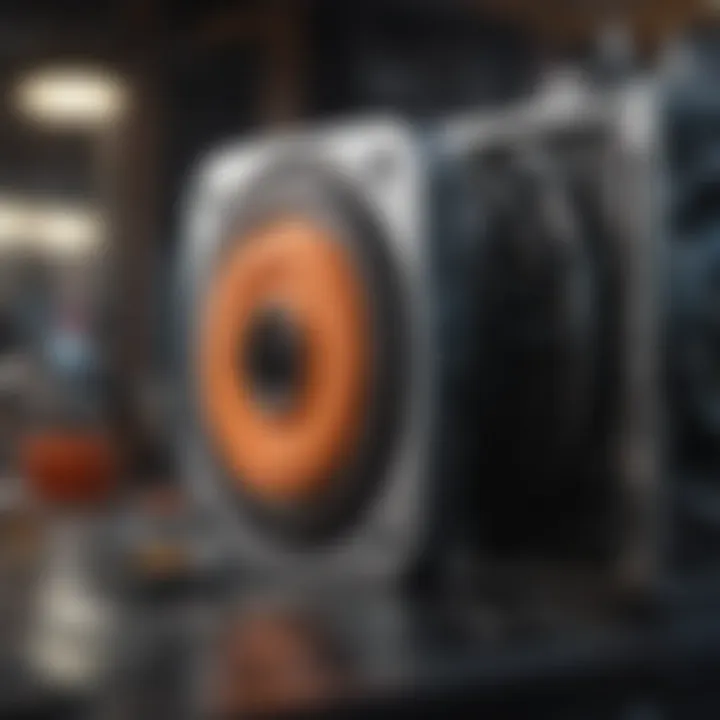
Intro
Three-dimensional printing stands at the frontier of modern manufacturing and design, reshaping various industries from healthcare to construction. This technique, often seen as cutting-edge, is in fact built upon principles that have evolved over decades. Whatâs remarkable is how accessible this technology has become, with dreams of creating something from scratch now within grasp for many. Understanding the mechanisms behind 3D printing takes us into the heart of this technological revolution.
In providing a closer look, we will explore the methods employed in this printing process, the materials used, and the various applications that reflect its versatility. The objective is to demystify how 3D printing operates and to highlight its significance in everyday life as well as its transformative potential for the future.
Research Overview
Understanding the mechanisms of 3D printing requires both a historical lens and a grasp of current advancements. Delving into these aspects allows us to appreciate how far weâve come and where we might be headed.
Key Findings
- 3D printing has moved from industrial applications to consumer accessibility.
- Multiple technologies exist in the realm of 3D printing, including Fused Deposition Modeling (FDM) and Selective Laser Sintering (SLS).
- The materials used range from plastics to metals, opening avenues for innovation in various sectors.
Study Methodology
This research compiles data and insights from numerous credible sources including academic journals, industry reports, and expert discussions. Observing trends in 3D printing technology showcases how it adapts and responds to the needs of various fields, underlined by real-world case studies.
Background and Context
In order to grasp the significance of 3D printing, grasping its roots and evolution provides essential context.
Historical Background
The roots of 3D printing trace back to the early 1980s, pioneered by Charles Hull, who introduced stereolithography. This innovation carved out the path for modern printing methods, as long as it may feel, itâs a story indeed short in the span of technological development.
Current Trends in the Field
Today, the landscape is rapidly changing. Numerous industries are embracing 3D printing, heralding it as a game-changer. From bio-printing for organs and tissues to custom prototypes for car designs, its reach grows broader every day. Current trends highlight the integration of Artificial Intelligence in optimizing printing processes, demonstrating a blend of tradition and innovation.
"3D printing technology is reshaping the very fabric of our industries, revealing new possibilities in both design and production."
Preamble to Three-Dimensional Printing
Three-dimensional printing has swiftly become a cornerstone in modern manufacturing and design, revolutionizing how products are conceived, created, and distributed. This form of additive manufacturing allows for the creation of tangible objects from digital models, using various materials. By laying down materials in layers, it enables intricate designs and customized solutions that traditional methods often cannot achieve. The importance of 3D printing in todayâs world cannot be overstated; it offers significant benefits such as reduced waste, enhanced efficiency, and the possibility of rapid prototyping.
Definition and Evolution
3D printing, at its core, is a technique that constructs objects from three-dimensional digital files. This technology has evolved rapidly since its inception in the 1980s. Originally, it was viewed as a niche process, primarily useful for prototyping in industrial settings. Today, however, it's making waves across various sectors. The evolution from basic materials, such as simple plastics, to complex composites and bioprinting materials showcases its versatility and potential. This technology has transformed from mere curiosity to a fundamental tool that enhances creativity and innovation.
Applications Across Industries
The reach of 3D printing extends well beyond hobbyist projects. Its applications are vast and diverse, influencing industries such as:
- Medical: Custom prosthetics, dental implants, and even bioprinted tissues.
- Aerospace: Lightweight components that reduce fuel consumption.
- Automotive: Rapid prototyping for design iterations and custom parts.
- Fashion and Art: Unique jewelry designs and bespoke art pieces.
- Construction: 3D-printed homes and structures that are quick to assemble.
"The best part about 3D printing is that it blurs the line between creativity and practicality."
Each of these industries benefits from the flexibility and efficiency of 3D printing. It's particularly noteworthy how this technology allows for customization and rapid iteration, which are crucial in a fast-paced market. As the technology continues to mature, the list of applications grows, hinting at an even more integrated future of production.
In summary, understanding the roots and current scope of 3D printing is essential for anyone interested in design, manufacturing, or technology. This article aims to delve deeper into its mechanics, operational principles, and the implications for various fields.
Key Technologies in 3D Printing
Understanding the key technologies in 3D printing is crucial for grasping how this innovative field operates and transforms various industries. Each technology has its own set of strengths and drawbacks, catering to different applications and materials. By delving into these specific approaches, we can appreciate their individual roles in the broader context of additive manufacturing. The evolution of these technologies marks significant advancements that lead to potential industrial revolution, enhancing capabilities from rapid prototyping to the production of complex structures.
Fused Deposition Modeling
Fused Deposition Modeling (FDM) stands as one of the most widespread and accessible 3D printing techniques. In essence, FDM works by extruding a thermoplastic filament through a heated nozzle, which melts the material and deposits it layer by layer to form a three-dimensional object. The process is akin to squeezing toothpaste from a tube, where the material flows out and is shaped as it cools and solidifies.
Benefits of FDM:
- Cost-Effectiveness: FDM printers are often more affordable compared to other technologies, making it a popular choice for hobbyists and educational institutions.
- Material Variety: A broad range of thermoplastics, such as ABS and PLA, can be utilized.
- Ease of Use: Many FDM printers come ready for use straight out of the box, lowering the barrier to entry.
However, FDM isn't without its limitations. The layer lines can be visible, affecting the surface finish, and the mechanical strength can sometimes vary due to the nature of how layers bond. Despite this, its simplicity and adaptability cement FDM as a go-to choice for many applications.
Stereolithography
Stereolithography (SLA) introduced a groundbreaking method by using ultraviolet light to cure liquid resin into solid forms. An SLA printer projects a UV laser onto a vat of photopolymer resin, solidifying the material layer by layer. This method is somewhat like painting with a laser: the laser traces patterns in the liquid resin, creating intricate designs.
Considerations for SLA:
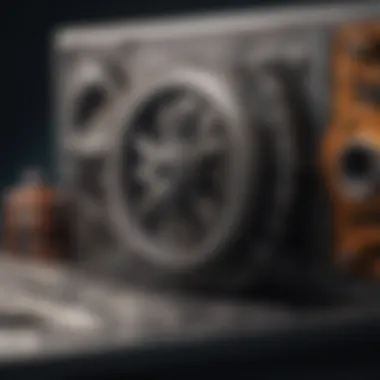
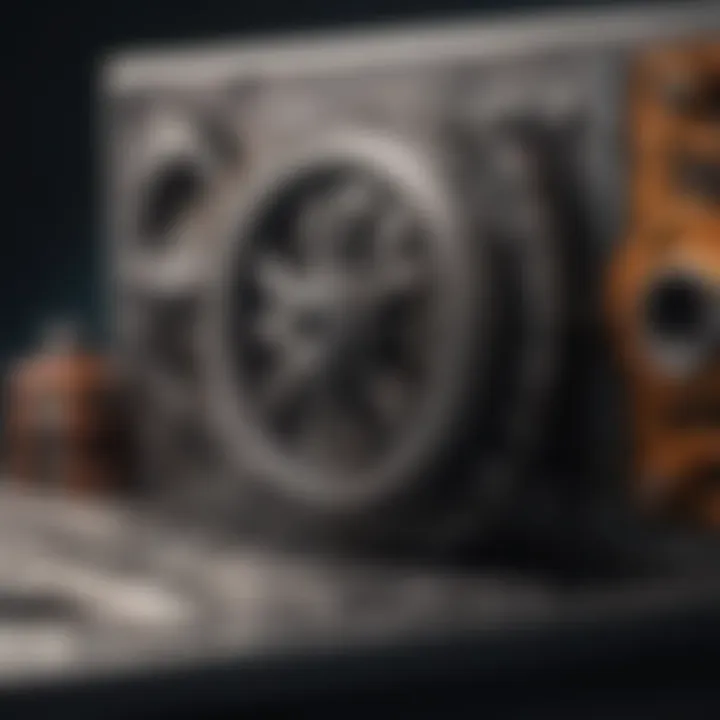
- High Resolution: SLA printers are capable of achieving remarkable detail and smooth surface finishes, making them ideal for prototypes, jewelry, and dental applications.
- Material Properties: Photopolymer resins can be engineered for various applications, including clear or flexible materials.
- Post-Processing Needs: After printing, models typically require washing and curing, which adds to the overall time and complexity of the process.
While SLA offers superior resolution, the associated costs of resin and post-processing can be drawbacks when considering it for large production runs.
Selective Laser Sintering
Selective Laser Sintering (SLS) is known for its ability to work with a variety of materials, including plastics, metals, and ceramics. The process involves using a powerful laser to sinter powdered material into solid structures. The laser selectively melts the powder based on the 3D model, layer by layer.
Key Advantages of SLS:
- No Support Structures: Uniquely, the unsintered powder acts as support for overhangs and complex geometries, which simplifies design possibilities.
- Material Versatility: SLS can utilize a variety of materials, expanding its applications in fields such as aerospace and automotive, where different properties might be required.
- Strength and Durability: Parts produced via SLS often have superior mechanical properties.
However, the equipment involved is costly, and the surface finish does generally require post-processing to achieve the desired aesthetic or functional quality.
Digital Light Processing
Digital Light Processing (DLP) is another resin-based technique similar to SLA, but it utilizes a digital light projector to cure the resin in one go. Instead of tracing the design with a laser, a DLP printer shines light onto an entire layer, curing the resin all at once.
Key Points of DLP:
- Speed: DLP generally provides faster production times due to the layer-wide curing method.
- Resolution: It achieves similar resolutions to SLA, although the quality of the model can depend greatly on the projector's detail.
- Material Properties: Like SLA, the choice of materials can be customized for specific applications, which adds versatility.
Despite the speed advantage, the ongoing costs related to resin and the limitations on part size due to the projector's resolution can pose challenges.
In summary, each of these technologies brings unique characteristics to the 3D printing arena, catering to an array of applications. Understanding their mechanisms lays the groundwork for exploring the wider implications of 3D printing innovation.
The 3D Printing Process Explained
Understanding the 3D printing process is crucial for anyone delving into this rapidly evolving field. This segment focuses on the essential steps that govern each build, covering the nitty-gritty details that ensure successful outcomes. Such insights not only underline the benefits of 3D printingâlike customization and efficiencyâbut also offer a roadmap for avoiding common pitfalls. Recognizing the intricacies involved can aid engineers, designers, and hobbyists alike in maximizing the technology's potential.
Model Design and Preparation
The journey of 3D printing begins with the creation of a digital model. This digital representation must be both precise and detailed. Specialized software tools like CAD (Computer-Aided Design) are frequently used at this stage. A well-constructed model ensures that the final output closely resembles the intended design.
Once the model is drafted, itâs time for some prep work. The file is converted into a format, typically STL, that the printer can understand. It's essential to check for any errors in this conversion. Sometimes, you might notice holes or gaps that never appeared in the design. Fixing these issues is pivotal because any discrepancy here can lead to structural weaknesses in the printed object. Choosing the right settings for the printing software is also part of this stage, from adjusting layer height to fill density. An informed choice here can greatly influence not just the strength of the component but also its overall aesthetic quality.
Material Selection
Material selection in 3D printing is like choosing the right ingredients for a dish; the outcome depends significantly on this choice. The properties of the chosen material can affect everything from durability to appearance. Common materials for 3D printing include thermoplastics like PLA and ABS, metals like titanium for industrial applications, ceramics for aesthetic elements, and even biomaterials for medical uses.
Considerations for material selection include:
- Mechanical properties: Strength, flexibility, and thermal resistance.
- Cost: Some materials are significantly pricier than others.
- Compatibility: Ensure the material works well with the specific type of printer being used.
- Availability: Not all materials are readily available, which might impact lead times.
The role of material selection cannot be understatedâit defines the feasibility of the project and ultimately influences the final quality.
Layer-by-Layer Construction
Once the model is set and materials are ready, we move into the heart of the process: layer-by-layer construction. This method is the essence of 3D printing. Here, the computer-controlled printer assembles the model slice by slice, using the specified material. The precision of layering is what distinguishes 3D printing from traditional manufacturing methods.
Each layer bonds with the previous one while ensuring that there are no mishaps. If the printer misapplies material in this phase, it can lead to warping or a failure to adhere properly. This stage also highlights the time efficiency of 3D printingâcomplex designs that would take weeks through machining can sometimes be done in hours. This capability opens doors for rapid prototyping, allowing designers to test and tweak their models without excessive delay.
Post-Processing Techniques
After the object emerges from the printer, the job isnât finished quite yet. Post-processing is a critical step that can elevate the quality and utility of the final product. This stage may involve cleaning up the print, removing supports, and applying surface finishes. Methods could include sanding to smooth out surfaces or painting for aesthetic appeal.
Additionally, techniques like annealing may be employed to relieve internal stresses and enhance strength. This step is often overlooked, yet it can significantly improve durability and meet specific design requirements. A well-executed post-processing phase can mean the difference between a mediocre piece and one that meets high professional standards.
"In 3D printing, quality doesn't just pop out of the machine; it requires careful thought at every step, especially post-processing."
Understanding these elements of the 3D printing process not only emphasizes the complexity involved but also provides a roadmap for anyone looking to utilize this cutting-edge technology successfully. Each step, meticulously executed, paves the way for innovative creations that can change the landscape across various industries.
Material Considerations in 3D Printing
In the realm of three-dimensional printing, the choice of materials cannot be overstated. Materials serve as the foundational building blocks of any 3D printed object, influencing not just the physical properties of the final product, but also its cost, functionality, and suitability for specific applications. Understanding the nuances of various materials opens up a plethora of possibilities, and in this section, we will delve into the main categories of materials employed in 3D printing, each with its own set of characteristics, advantages, and limitations.
Thermoplastics
Thermoplastics are often the go-to materials in the world of 3D printing, and itâs easy to see why. These materials become pliable or moldable at elevated temperatures, which means they can be repeatedly melted and reshaped without losing their original properties. This makes thermoplastics versatile and cost-effective, particularly in Fused Deposition Modeling (FDM) printing, where they are layered to create complex shapes.
Some popular thermoplastics include:
- PLA (Polylactic Acid): Derived from renewable resources, PLA is celebrated for its ease of use. Itâs non-toxic and produces a low odor during printing. Although it is strong for everyday applications, it may not be ideal for high-temperature environments.
- ABS (Acrylonitrile Butadiene Styrene): This material offers greater durability and higher temperature resistance compared to PLA. However, it can release unpleasant fumes and typically requires a heated bed for optimal printing.
- PETG (Polyethylene Terephthalate Glycol): PETG combines the best of both worlds. It's a clear material that's resistant to impact and temperature, making it a solid choice for parts that require strength.
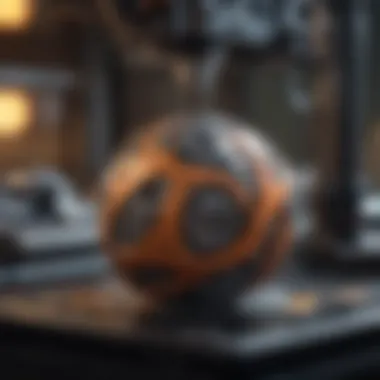
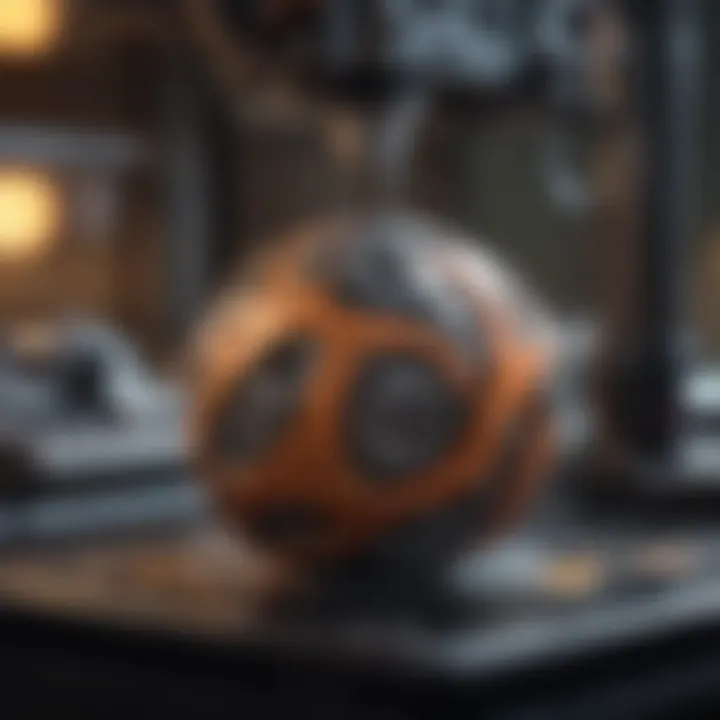
The choice of thermoplastic often hinges on the specific requirements of the project, including environmental considerations and desired material properties.
Metals
Metal 3D printing offers unparalleled strength and durability, which is why itâs making waves in high-stakes industries like aerospace and automotive. Traditional metal manufacturing can be costly and time-consuming; however, additive manufacturing methods like Selective Laser Melting (SLM) and Electron Beam Melting (EBM) have made it feasible to produce complex metal geometries without the need for extensive tooling.
Common metals used in 3D printing include:
- Titanium: Renowned for its strength-to-weight ratio, titanium is used in applications where lightweight materials are crucial. Its biocompatibility also makes it popular in the medical field.
- Stainless Steel: Known for its resistance to corrosion, stainless steel is used frequently across various sectors including manufacturing and engineering, offering a good balance between workability and performance.
- Aluminum: Lightweight and strong, aluminum is often chosen for prototypes or parts requiring heat resistance. Its conductive properties make it useful in electronics applications.
Navigating the world of metal 3D printing requires a strong grasp of both the printing technology and the specific characteristics of the metal being used.
Ceramics
Ceramics might not spring to mind when discussing 3D printing, yet their unique properties allow for fascinating applications. Known for their thermal stability and hardness, ceramics can be used in areas such as biomedical implants and art. Techniques such as binder jetting or SLA can create intricate designs that showcase the material's strengths.
Some notable ceramics include:
- Alumina: Highly durable, alumina is frequently used for cutting tools or medical applications due to its biocompatibility.
- Silicon Nitride: This material is recognized for its outstanding thermal stability, making it perfect for high-temperature applications.
Ceramics may present challenges during the printing process, such as the need for specific conditions to prevent cracking during cooling, yet they are invaluable in specialized niches.
Biomaterials
As the field of 3D printing continues to mature, the demand for biomaterialsâ substances crafted for compatibility with biological systemsâ has surged. They are particularly relevant in medical applications, where they support the creation of custom implants and prosthetics.
- Hydrogels: Used primarily in tissue engineering, hydrogels can mimic the properties of natural tissues due to their water content. Theyâre essential in research and development of soft tissue replacements.
- Bioactive Glass: This material supports bone regeneration and is ideal for orthopedic implants. Its bioactivity encourages the surrounding tissue to bond with the implant, stimulating healing.
As we move forward in this innovative landscape, biomaterials hold promise not only for enhancing human health but also for addressing the ethical considerations surrounding medical applications.
"The choice of material defines the realm of possibility for 3D printing, influencing both the capability of production and the applicability of the final products."
In summary, understanding material considerations in 3D printing is integral to harnessing its full potential. Each material type highlights a specific area where 3D printing excels, be it in cost efficiency, durability, or medical applications. This understanding can drive new innovations and lead to a future where 3D printing fundamentally reshapes manufacturing across multiple domains.
Applications of 3D Printing in Various Fields
The importance of exploring the applications of 3D printing in various fields cannot be overstated. This innovative technology, having transitioned from prototyping into full-scale production, has opened up avenues that were previously thought to be a pipe dream. From medical breakthroughs to reshaping the way buildings are constructed, the versatility and adaptability of 3D printing make it an essential focal point of modern manufacturing and design.
Medical and Dental Innovations
In the realm of healthcare, 3D printing has revolutionized how medical devices and prosthetics are created. Just think of the breakthroughs happening right now. Customized implants designed specifically for a patient's unique anatomy can dramatically improve fit and function. For instance, cranial implants can now be tailored for individual patients, enhancing healing processes significantly.
Moreover, the dental field has seen innovations as well. 3D printing opens the door for tailor-made aligners or crowns, resulting in better comfort and effectiveness. Surgeons also use 3D-printed models from patient scans. These models allow for meticulous planning, thus minimizing risks during complex surgeries. In summary, the key benefits of 3D printing in medicine include:
- Customization to individual patient needs
- Reduction of lead times in product delivery
- Enhanced surgical outcomes through surgical planning
"3D printing in healthcare is not just a trend; it is a game changer that saves lives and enhances quality of care."
Aerospace and Automotive Engineering
When we pivot to aerospace and automotive industries, the story remains impressive. Here, 3D printing is leveraged for both prototyping and final products. For instance, companies can fabricate lighter components that minimize fuel consumptionâsmart thinking for both budget and environment.
Lightweight structures crafted through selective laser sintering or metal printing drastically reduce the weight of aircraft, which translates to fuel efficiency. Additionally, spare parts can be produced on-demand, lessening the requirement for extensive inventories. This also leads to improved supply chain models, with potential cost savings. The main elements at play in this sector are:
- Improved efficiency in production cycles
- Tailored designs that were not feasible with traditional methods
- Faster prototyping leading to quicker time-to-market
Fashion and Art
Even the worlds of fashion and art arenât left untouched by this technological wave. Designers have begun using 3D printing to create intricate textiles and accessories that are impossible to produce through traditional means. The ability to design one-off pieces leads to an era of unique identities in apparel. Not only does this challenge conventional concepts of fashion, but it also raises questions about sustainability. By producing only what is needed, waste can be considerably reduced.
Artistic applications also show that artists are harnessing 3D printing for sculpture and installation art. The boundary of creation is pushed every day with designs that might resemble digital fantasies. Aspects to consider here include:
- Customizability and individuality of fashion pieces
- Sustainability through reduced fabric waste
- New artistic expressions that take advantage of printing technology
Architecture and Construction
The influence of 3D printing on architecture is particularly noteworthy. Architects can now visualize and produce intricate building designsâones they only imagined before. Imagine 3D-printed houses that can be put together quickly and at a fraction of traditional costs.
Recent efforts have seen entire homes constructed using massive 3D printers. These initiatives aim not just to innovate, but also to provide affordable housing solutions worldwide. Moreover, creating architectural models can help stakeholders visualize projects before breaking ground. Critical considerations here include:
- Faster construction processes and reduced labor costs
- Novel designs that push architectural limits
- Addressing practical concerns like affordability and scalability
Challenges and Limitations of 3D Printing

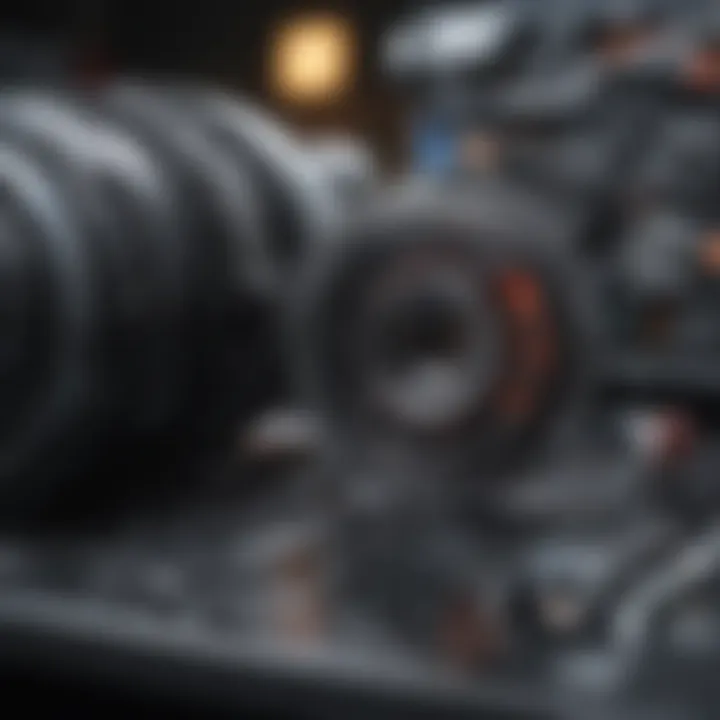
3D printing, while revolutionary, is no walk in the park. As with any technology, it carries its own set of challenges and limitations that are crucial to understand. These hurdles not only influence its current applications but also determine its future trajectory in various industries. For students, researchers, educators, and professionals, grasping these constraints is paramount to harnessing the true potential of this technology and mitigating risks involved in its adoption.
Technical Constraints
One significant hurdle in the realm of 3D printing is technical constraints. This encompasses various factors such as the size of the printer, resolution, speed, and the complexity of the designs. The average 3D printer, especially those that are more traditional, has a limited build volume; creating large-scale objects requires either assembling multiple smaller pieces or using industrial-grade machines that can cost an arm and a leg.
Moreover, the resolution of the print is heavily influenced by layer thickness. Thinner layers yield a smoother finish but often at the cost of longer printing times. This results in a delicate balancing act between speed and quality. Designers must consider not just how their objects look on a screen but also how they will translate into the physical realm. Certain design intricacies may also exceed what certain printers can handle, leading to potential failures during the printing process.
Material Issues
Next on the list is material issues, which highlight the intricacies of the substances used in 3D printing. While the selection of materials has expanded greatly, the compatibility of materials with different technologies remains a challenge. Not every printer can handle every kind of filament or resin. For example, printers may struggle with materials that are either too brittle or too flexible, leading to compromised structural integrity in the final products.
In addition, the properties of common materials like plastics, metals, and ceramics can vary widely. Thermal behaviors, curing times, and bonding strength all play a role in how these materials behave during and after the printing process. For instance, while PLA is user-friendly and biodegradable, it may not withstand higher temperatures compared to ABS, which is stronger but not as environmentally friendly.
The journey from concept to physical object demands a meticulous approach towards selecting materials, ensuring that they fit the specific requirements of the end use.
Economic Considerations
Lastly, we cannot overlook the economic considerations tied to 3D printing. Initial investment in high-quality printers, especially those capable of producing intricate or large-scale items, can be quite steep. Beyond the purchase costs, there's maintenance, material sourcing, and, often, the hiring or training of skilled operators that add to the total expenditure.
Additionally, there are ongoing costs associated with production that can affect profitability. For businesses looking to adopt 3D printing for mass production, the question of scalability arises. Most 3D printers are best suited for small-batch manufacturing. When it comes to competing with traditional methods like injection molding, which can churn out thousands of parts rapidly and at a lower cost, 3D printing may find itself at a disadvantage for large-scale production runs.
"The promise of 3D printing lies not only in what it can create but also in the myriad complexities it unveils along the way. Experience teaches that to innovate is to embrace limitations and find ways to rise above them."
In summary, while 3D printing holds a treasure trove of potential, the hurdles it presentsâbe it technical limitations, material compatibility, or economic constraintsâmust be acknowledged and addressed. Understanding these challenges not only paves the way for more efficient processes but also allows for improved designs and more thoughtful applications within a landscape that is rapidly evolving.
Future Trends in 3D Printing Technology
The landscape of three-dimensional printing is rapidly evolving, driven by technological advancements, shifts in user demand, and an increasing focus on sustainability. Recognizing these future trends is crucial for anyone invested in this space, as they signal possibilities and encourage innovation. As diverse industries look to leverage these enhancements, understanding their implications can guide strategic decisions and operational practices.
Advancements in Materials Science
Material innovation stands at the forefront of 3D printing's future. Traditional plastics are being supplemented and, in some cases, replaced by high-performance materials. For example, researchers are making strides in developing composite filaments that enhance strength without weighing a ton. Additionally, bio-based materials are gaining traction. These not only align with environmental concerns but also demonstrate improved functionality. Consider the potential of thermoplastics infused with natural fibersâquite a leap from conventional materials!
Further research into metals is also notable. Novel alloys designed specifically for 3D printing can yield stronger and more durable parts. Industries such as aerospace and automotive will surely benefit from these materials that withstand extreme conditions while being lightweight.
- Key Focus Areas in Materials Science:
- High-performance thermoplastics
- Bio-based materials
- Specialized metal alloys
Sustainability and Eco-Friendliness
Sustainability is climbing the ranks in importance within the 3D printing sector. As manufacturers seek to lessen their environmental footprint, there's a burgeoning emphasis on eco-friendly practices. This includes optimizing printing processes to reduce waste and energy consumption. Traditional methods often generate excess, but 3D printing can minimize material use by nature of its additive approach.
Moreover, sourcing sustainable materials such as bio-plastics can drastically cut down on reliance on fossil fuels. It's worth noting that companies are also exploring biodegradable materials that break down without leaving a harmful impact. Such advancements not only serve business interests but can resonate well with a more conscious consumer base.
"Incorporating sustainability into 3D printing isnât just a trend; itâs the future of manufacturing."
- Key Sustainability Initiatives:
- Waste reduction in manufacturing
- Use of renewable resources
- Development of biodegradable materials
Integration with Other Technologies
The merging of 3D printing with other technologies is another trend shaping the future. From artificial intelligence to the Internet of Things, these integrations promise to enhance capabilities and efficiencies. For instance, AI can optimize the design process, predicting structural weaknesses and suggesting ideal materials.
Similarly, the Internet of Things allows for real-time monitoring of printing operations, creating opportunities for greater precision and control. These advancements can result in less downtime and more efficient production schedules, helping industries respond swiftly to market demands.
- Noteworthy Integrations:
- AI for design optimization
- IoT for operational monitoring
- Robotics for automated workflows
As 3D printing continues to develop, staying informed about these trends is essential. The future holds unprecedented opportunities for innovation and efficiency, bridging the gap between conception and realization in ways never before imagined.
The End: The Impact of 3D Printing
The subject of three-dimensional printing stands as a significant beacon in modern fabrication and design. This area transcends traditional manufacturing methods, carving new pathways for innovation across varied fields. Recognizing the profound implications of 3D printing is crucialânot just for its technological marvels but for its vast potential to redefine societal norms and processes.
Summary of Key Insights
Many threads intertwine to weave the narrative of 3D printing. Key considerations include:
- Complexity and Accessibility: Originally, 3D printing was a technique reserved for specialized industries with significant capital investments. Now, more affordable tools and software have democratized this technology, allowing small businesses and hobbyists to participate.
- Customization and Prototype Development: One noteworthy feature is the ability to produce highly customized designs. Whether creating anatomical models in healthcare or tailored components in aerospace, 3D printing enables faster iterations and prototyping. This fundamentally alters how products evolve from conceptual stages to final designs.
- Sustainability Considerations: The material waste involved in traditional manufacturing processes raises environmental concerns. In contrast, the additive nature of 3D printing aims to cut down on waste. Still, a long-term evaluation is essential to fully understand its environmental footprint.
The Broader Implications for Society
The rise of 3D printing heralds not just a manufacturing shift, but also a significant societal change. Here are some broader implications that may affect the fabric of communities and industries in the future:
- Job Displacement and Creation: As with any technological revolution, there is a dual effect on employment. While certain jobs may become obsolete, new opportunities in design, engineering, and maintenance of 3D printing technologies will emerge, demanding a workforce skilled in this new paradigm.
- Cultural and Educational Shifts: Schools and universities increasingly integrate 3D printing into their curriculum. Hands-on learning experiences can spark curiosity and innovation in young minds, paving the way for a more technologically adept society.
- Globalization and Local Production: With its ability to manufacture goods locally, 3D printing challenges global supply chains. This shift could foster localized economies, where communities produce what they need, reducing reliance on distant suppliers.