Static Mixer Design: Key Principles and Uses
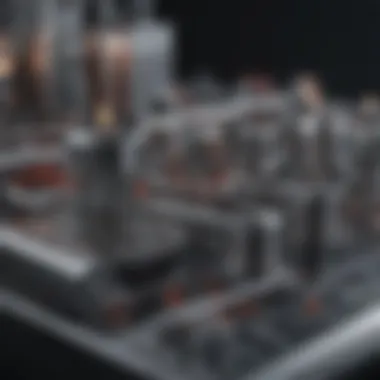
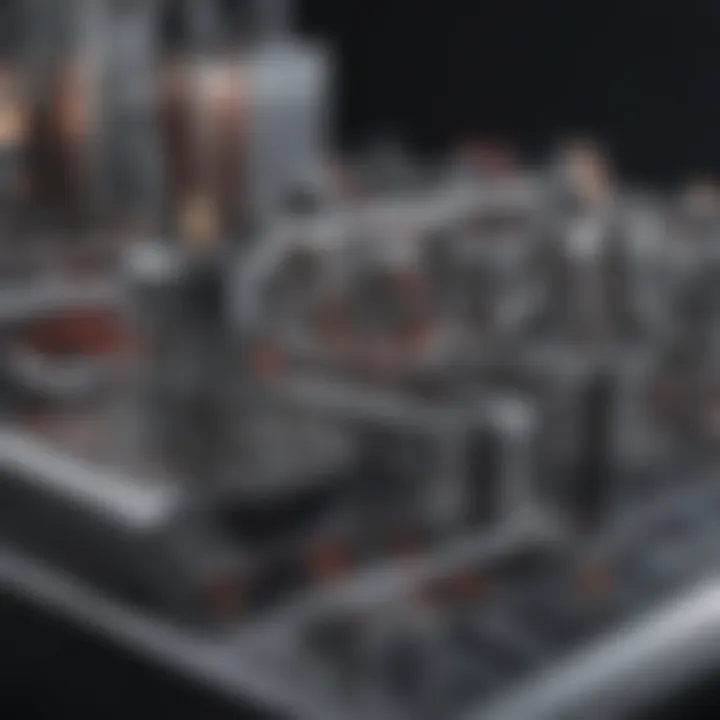
Intro
Static mixers are an essential part of many industries. From food processing to chemical manufacturing, they're behind the scenes, ensuring consistent outcomes without the need for moving parts. Understanding the design principles of these mixers is crucial for those involved in any blending processes. This section aims to set the stage for what’s to come, highlighting the significance of effective mixer design and its impact on operational efficiency.
Static mixers rely on the principles of fluid dynamics to achieve thorough mixing of different components. As we go on in this article, we'll explore various strategies, materials, and innovation trends that shape the effectiveness of these devices. By dissecting the key elements of static mixer design, professionals can gain valuable insights into optimizing their processes.
Research Overview
In the realm of static mixers, gaining an in-depth understanding requires a close examination of both existing literature and practical applications. A focused approach not only reveals key findings but also illustrates current methodologies that drive mixer design.
Key Findings
- Static mixers enhance mixing efficiency without the complexity of moving parts.
- The design can significantly affect the flow regime, impacting the end product consistency.
- Innovations in materials lead to better thermal and chemical resistance, improving longevity and reliability.
Study Methodology
To grasp the intricacies of static mixer design, a triangulated methodology was employed:
- Literature Review: Relevant studies were examined to extract historical data and current advancements in the field.
- Case Studies: A few case studies from industries, such as wastewater management and food processing, were analyzed to identify best practices in mixer usage.
- Expert Interviews: Insights from professionals in the field provided a real-world perspective on the challenges and triumphs associated with static mixer design.
Background and Context
Historical Background
The concept of static mixing dates back several decades, arising from the need for effective mixing techniques in various processes. Early static mixers were simplistic in design, often made from metal or glass, and merely aimed to direct flow through specific geometries. Over time, advancements have been made in both understanding fluid mechanics and the development of innovative materials that could withstand harsh environments. This foundation established the critical role static mixers play today in many industrial processes.
Current Trends in the Field
Today’s designs have evolved to incorporate more sophisticated principles of turbulence and flow. There is a shift towards using customizable options tailored to specific applications. Also, the evolution in materials, such as the integration of polymers that can endure corrosive substances, has seen a surge.
The adoption of smart technologies is another aspect where the industry is headed. IoT integration and real-time monitoring can improve control over the blending process, eventually leading to better product quality and reduced waste.
As we continue our discussion, the principles behind static mixer design will uncover more about how these devices contribute to efficiency in various sectors. With a strategic approach to static mixer design, industries can truly optimize their operational capabilities.
Prelude to Static Mixers
Static mixers have carved out an undisputed niche in the realm of industrial processes, acting as indispensable players in the mixing of fluids without the mechanical complexities associated with dynamic mixers. Their unique ability to blend, disperse, and emulsify materials all while maintaining a steady flow makes them vital in numerous applications, from chemical manufacturing to food production and beyond.
The significance of static mixers lies not only in their operational simplicity but also in their cost-effectiveness and reliability. Key benefits include reduced maintenance due to the absence of moving parts, uniformity in product quality, and enhanced efficiency. They are often employed where precise mixing is necessary, such as in the pharmaceutical industry, ensuring that active ingredients are thoroughly blended before packaging.
When discussing static mixers, one must also consider the conditions under which they operate. Fluid properties, such as viscosity and density, and the specific application requirements can dramatically affect performance.
By understanding the fundamental principles of static mixers, professionals across varied sectors can better optimize their processes. The reliability of static mixers has led to increased emphasis on their design and application, prompting continuous research and development aimed at improving their efficiency and versatility. Their growing significance will be explored further in this article.
Definition and Purpose
A static mixer is a device designed to mix fluids without using any moving components. At its core, the static mixer consists of a series of stationary elements or blades that disrupt the flow of the incoming fluids. This disruption promotes random mixing, which is essential in achieving the desired product properties. The main purpose of static mixers is to create a uniform mixture by blending different components effectively and consistently.
Most static mixers operate based on the principle of turbulence. As the fluid passes through the mixer, it encounters various shapes and configurations that create a turbulent flow, enhancing mixing. This is particularly useful in applications requiring specific characteristics, such as in the creation of emulsions or in chemical reactions.
Historical Context
The journey of static mixers traces back to the increasing needs of various industries to simplify complex mixing processes. Historically, mechanical mixing methods dominated, relying heavily on energy-intensive equipment with numerous moving parts. As industries evolved and the demand for more consistent and efficient mixing solutions grew, static mixers began to surface.
In the 1940s, advancements in material science and fluid dynamics opened the door for the development of static mixing technology. Early designs were quite rudimentary, often consisting of simple pipe constructs with fixed obstructions that aimed to promote mixing. However, with time and research, the designs became more sophisticated, leading to varied types of mixing elements tailored to specific processes.
This evolution reflects a broader trend in engineering and industrial design towards simplifying hardware while enhancing performance. Today, we see complex models engineered for specific applications, employing advanced materials and technology to create efficient mixing solutions. Understanding this historical context not only highlights the evolution of static mixer design but also sets the stage for exploring contemporary applications and future trends in the field.
Fundamental Principles of Static Mixer Design
The essence of static mixer design is crucial for ensuring optimal performance in a wide range of applications. Fundamental principles govern how different variables interact, which ultimately affects both efficiency and output quality. Understanding these principles can significantly improve a system's throughput and enhance the uniformity of mixed products. By grasping these fundamentals, professionals in various industries can tailor their static mixers for specific needs and achieve more consistent results.
Mechanics of Mixing
To appreciate the mechanics behind mixing, one must consider how materials interact at microscopic levels. When two or more fluids enter a static mixer, they don't simply combine like water and sand. Instead, it's akin to trying to integrate different fabrics; each component has its unique properties that influence the outcome. The design of the static mixer plays an essential role here.
The primary mechanics involve shear and torsion forces operating on the fluid particles. This causes the substances to intertwine thoroughly. Think of it as weaving a complex tapestry where every thread contributes to the final product’s aesthetics. These forces ensure that particles are continuously disrupted, promoting better blending and ultimately leading to improved performance.
Flow Dynamics
Flow dynamics in a static mixer refer to the behavior of fluids as they traverse through the mixer’s structure. The flow can be laminar or turbulent, with each state having its implications for mixing efficiency. In simpler terms, laminar flow is like a serene stream, where everything moves smoothly, while turbulent flow resembles a rapids, agitating the water in many directions.
Appropriate design can help achieve the desired flow characteristics. For instance, using elements with strategic placements, one can increase turbulence in regions requiring more intense mixing. Moreover, the flow rates are also critical. Too fast, and you might sacrifice thorough mixing; too slow, and you waste valuable time. A well-designed mixer considers all these aspects, creatively aligning with the specific requirements of the fluid dynamics at play.
Viscosity and Its Effects
Viscosity is a game-changer in the world of static mixers. Essentially, it measures a fluid's resistance to flow. High-viscosity fluids, like thick honey, tend to be more challenging to mix than low-viscosity ones, like water. It’s not just about adding energy; it's about understanding how different viscosities change mixing behavior.
For static mixers, this characteristic impacts not only the mixer’s design but also the choice of materials. When dealing with viscous fluids, one must consider aspects like slowing down the velocity of the flow and the configuration of the mixing elements to improve contact between the components. Practical applications often involve dairy or polymer industries, where ignoring viscosity could lead to suboptimal products.
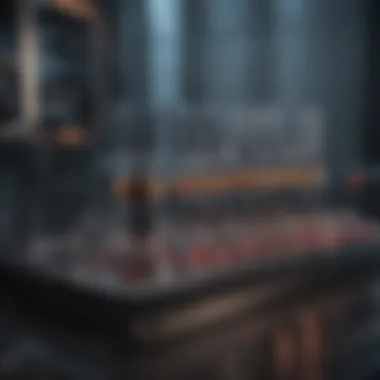
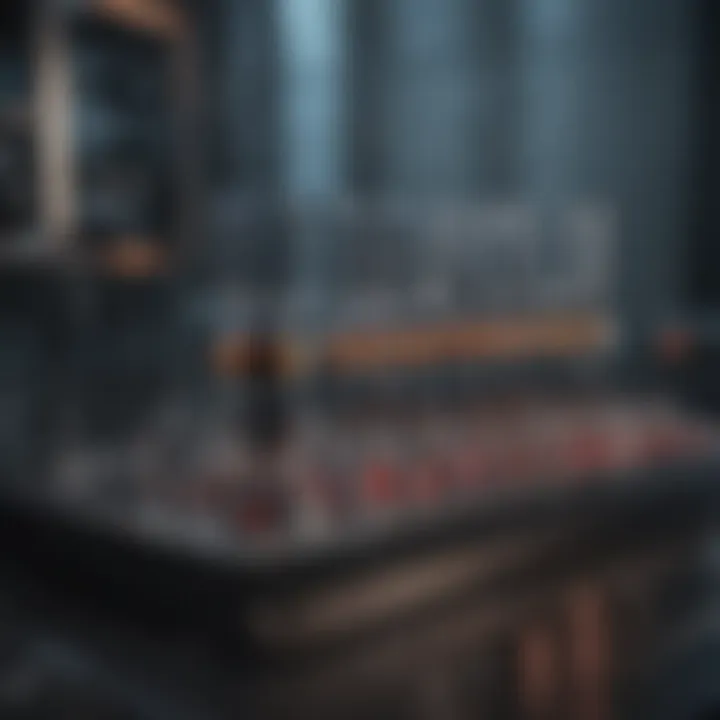
Components of Static Mixers
Understanding the components of static mixers is like knowing the ingredients of a good recipe; without them, you won't get the desired outcome. Static mixers consist of various elements that play crucial roles in the blending process. Each component contributes to the overall efficiency, effectiveness, and consistency of fluid mixing, thus making the selection of these components vital in the design phase.
Static Mixing Elements
Types of Elements
When talking about static mixing elements, we can break them down into several types, such as helical elements, distributive elements, and mixing blades. Helical elements, for instance, are designed to induce a swirling motion into the fluid. This swirls the fluid streams into each other, enhancing the mixing process significantly. One of the most prominent features of helical elements is their ability to create a continuous flow pattern, which is beneficial in applications that require a thorough blending of different fluids.
In contrast, distributive elements are crafted to divide the fluid streams into smaller segments before recombining them. They excel in scenarios where uniform distribution is the goal. This unique capability allows them to achieve greater mixing at lower energy costs, making them a popular choice for many industries. However, they may not be as efficient in blending highly viscous fluids compared to their helical counterparts.
Advantages of these elements are often tied to the specific needs of a process. For instance, while helical elements are effective for fast-moving and turbulent flows, distributive elements serve well in low-speed applications where gentle mixing suffices.
Geometry Considerations
The geometry of static mixers can’t be overlooked. The shape and configuration of mixing elements affect how fluids interact and mix. Typically, circular or rectangular cross-sections are common, but the details can vary widely. The key characteristic here is that geometry directly impacts the flow patterns within the mixer, which in turn influences the overall mixing efficiency.
For instance, a mixer with a more complex geometry can induce higher turbulence levels, resulting in better mixing. This complexity may come with its disadvantages, like increased pressure drops. Thus, designers must strike a balance between an effective mixing design and keeping flow resistance within acceptable limits.
Moreover, the dimensions of the static mixer must align with the expected flow rates. An oversized mixer may lead to wasted materials and costs, while an undersized one could result in insufficient mixing. A careful analysis of fluid properties and desired outcomes is crucial for choosing the right geometry.
Mixer Configurations
Inline Mixers
Inline mixers incorporate static mixing elements directly in the flow path. As fluid passes through these mixers, it encounters various elements that alter its structure, leading to a homogeneous blend. The simplicity of inline mixers is one of its major attractions; they're easy to install and often require little maintenance. A significant benefit lies in their compact design, which allows for seamless integration into existing systems without a need for major adjustments.
A unique feature is their ability to maintain the same flow direction, ensuring the mixing happens continuously as the fluid travels through. However, one should also note that the pressure drop across inline mixers can be more pronounced due to the flow resistance created by the mixing elements.
Pipeline Mixers
Pipeline mixers represent another configuration where mixing occurs within pipes. These mixers usually have larger structures that handle higher volumes of fluids. Because pipeline mixers function effectively in larger systems, they're often the go-to choice in industries that deal with high flow rates. A key characteristic of these mixers is their ability to handle solids or slurries efficiently, which is not always achievable with inline mixers.
The flexibility in installation is a major benefit; pipeline mixers can be placed at different stages in a system for optimal results. Yet, challenges can arise in terms of effective mixing. If not properly designed, these mixers may have dead zones where mixing is not as effective, leading to inconsistencies in the final product.
"The right choice of mixing components shapes not just the mixing efficiency but also the overall product quality. "
Design Methodologies
When it comes to crafting a static mixer, design methodologies stand as foundational pillars. They guide engineers in approaching the complex task of mixer design, ensuring that the end product meets the specific requirements of various applications. Understanding these methodologies can enhance both the performance and reliability of the mixers, ultimately leading to improved operational efficiency.
Key considerations include:
- Fluid characteristics: Properties of the fluids being mixed can significantly affect how the mixer should be designed.
- Desired mixing quality: Depending on the application, the level of mixing required may vary.
- Operational environment: Temperature, pressure, and the presence of corrosive substances can dictate materials and design choices.
- Safety and regulatory compliance: Always a priority, adhering to industry standards helps prevent accidents and ensures long-term reliability.
The methodologies employed can roughly be categorized into two main approaches: Computational Fluid Dynamics (CFD) and empirical methods. Each holds its own significance depending on the nature of the project.
Computational Fluid Dynamics (CFD)
CFD uses numerical analysis and algorithms to simulate fluid flow and mixing processes. With the ability to mimic various conditions, CFD enables designers to visualize and predict mixing behavior before any physical mixer is constructed. This strategy often saves both time and resources during the development phase.
Consider the capability of CFD to model:
- Inlet and outlet conditions: Analyzing how fluids enter and exit the mixer, providing insight into the operational flow dynamics.
- Mixing patterns: Identifying how effectively different fluids blend based on the selected static mixing elements.
- Pressure drop: Evaluating how much energy loss occurs due to flow characteristics, which is crucial for energy-efficient operation.
The insights garnered can potentially lead to better performance metrics, translating into higher quality end products. However, it is worth noting that simulation outcomes depend heavily on the quality of input data. Misrepresenting fluid properties can lead to flawed designs.
Empirical Methods
Empirical methods rely more heavily on real-world testing and observations rather than elaborate simulations. These methods often come into play when intuitive knowledge and historical data play a crucial role in the design process.
For instance, engineers might conduct:
- Pilot tests: Creating small-scale models to evaluate the effectiveness of different mixer configurations before committing to full-scale production.
- Performance comparisons: Using established mixers as benchmarks, allowing for a more straightforward evaluation of proposed designs.
Here, development moves through an iterative process, refining the design based on actual performance rather than theoretical predictions.
While empirical methods may seem less sophisticated, they offer invaluable data derived from practical experiences, which can sometimes outweigh the benefits of simulated outcomes. Not only do they provide real-time insight into mixing performance, but they also reveal unforeseen challenges that might not be captured in a simulation model.
By combining both methodologies, engineers can create a more robust and effective static mixer design, blending science with art to achieve optimal results.
A balanced combination of CFD and empirical methods can yield designs that meet both performance metrics and real-world demands.
Material Selection for Static Mixers
The choice of materials in static mixer design is not just a minor detail; it’s central to achieving effective mixing and ensuring longevity under various operational conditions. Selecting the right material involves considering factors such as chemical compatibility, viscosity of the fluids involved, and the environmental conditions the mixer will face. A well-made stirrer can significantly impact performance, affecting efficiency, costs, and overall system efficacy.
Common Materials
Metals
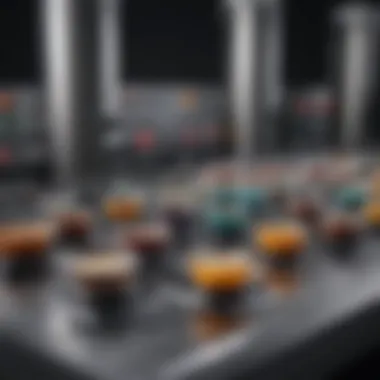
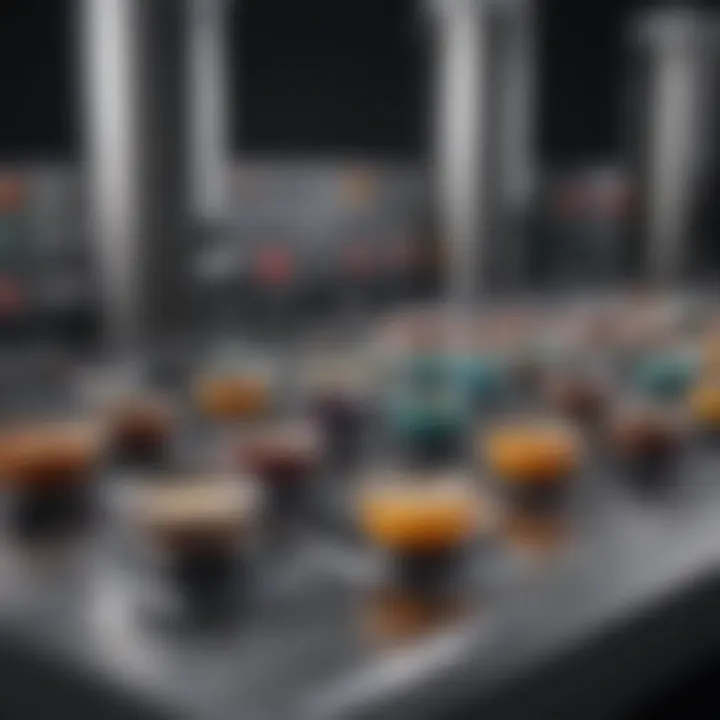
Metals stand out as some of the most robust materials used in static mixers. Stainless steel, in particular, is highly favored due to its excellent resistance to corrosion and mechanical wear. Its key characteristic is its durability under extreme conditions, which is paramount for industries that deal with aggressive chemicals or high-temperature processes.
In the context of static mixers, stainless steel’s low friction and high strength contribute favorably to fluid dynamics, minimizing pressure losses and enhancing mixing performance. Yet, they are not without their drawbacks; the cost of stainless steel can be significant compared to other materials, particularly for larger scale applications. Additionally, if not properly treated or maintained, it may be susceptible to pitting corrosion over time, leading to eventual failures.
Plastics
Plastics, such as polycarbonate and polypropylene, are another popular choice in the design of static mixers. One of the appealing aspects of plastics is their lightweight nature, which simplifies installation and maintenance. Furthermore, many plastics inherently possess good chemical resistance, making them suitable for a wide array of applications, from food processing to certain chemical treatments.
A unique feature of plastics is their manufacturing versatility; they can be easily molded into complex shapes that enhance mixing efficiency or tailored for specific applications. However, while cheaper in raw material costs, they might not hold up as well under high stress, especially at elevated temperatures. Over time, they may also become brittle or degrade when exposed to harsh chemicals, limiting their lifespan in some contexts.
Corrosion Resistance and Durability
When it comes to the life expectancy and reliability of static mixers, corrosion resistance and durability are of utmost importance. The materials chosen must withstand not only the mechanical forces at play but also the chemical environment they operate in.
Ensuring longevity in a static mixer design is critical for processes that require continuous operation without the frequent need for maintenance.
Many engineers opt for specialty alloys and coatings that extend the life of the mixer components. Materials with high corrosion resistance will typically decrease downtime and maintenance costs significantly, making them a worthwhile investment.
In summary, whether selecting metals or plastics, careful consideration must be given to the specific application and conditions of use. Balancing performance with cost-effectiveness is vital in making the right choice in material selection for static mixers.
Performance Evaluation Metrics
In the realm of static mixer design, performance evaluation metrics serve as the backbone for assessing how effectively a mixer operates. They not only guide the design process but also ensure that the mixer meets the necessary standards for various applications. Understanding these metrics provides valuable insights into the blend quality and overall efficiency, crucial for industries relying on precise fluid mixing.
Efficiency of Mixing
The efficiency of mixing is one of the primary metrics to evaluate in static mix design. It reflects how well the mixer achieves homogeneity in the output fluid. Efficiency can be assessed through several factors:
- Blend Uniformity: A critical aspect, this refers to the consistency of the mixture. For instance, in chemical processing, uneven blending can lead to inadequate reactions, impacting product quality.
- Mixing Time: This indicates how long it takes for the fluids to reach a desired level of homogeneity. Short mixing times often equate to higher throughput, which is especially vital in industries with high production demands.
- Fluid Properties Compatibility: Mixing efficiency can fluctuate based on the viscosities and flow rates of the fluids involved. For example, a static mixer designed for water may not perform efficiently with heavy oils without adjustments in design or operation.
To put it simply, if the mixer cannot achieve the ideal blending within a reasonable timeframe, it might require redesigning or further optimization.
Pressure Drop Analysis
Pressure drop analysis arises as another critical performance evaluation metric. It measures the resistance to fluid flow within the mixer. Understanding this aspect is crucial for several reasons:
- Energy Consumption: A significant pressure drop can indicate inefficient mixing and can raise energy costs. In an industrial setup, where energy efficiency is paramount, minimizing this drop can lead to substantial savings.
- Operational Stability: Excessive pressure drops could destabilize the overall mixing process. If the pressure fluctuates widely, it may lead to inconsistent mixing, causing downtime and ultimately affecting productivity.
- System Compatibility: Assessing the pressure drop helps to ensure that the static mixer integrates seamlessly with existing system components. It allows engineers to match the mixer with pumps and other fluid transport systems effectively.
"The pressure drop in a system isn’t merely a number; it’s a telltale sign of performance that can indicate potential problems before they become costly failures."
Applications of Static Mixers
Static mixers are not just pieces of equipment; they are essential drivers in various industries, providing solutions that are critical to maintaining quality and efficiency in fluid blending processes. Their applicability spans across sectors such as chemical processing, food and beverage production, and wastewater treatment, showcasing their versatility. The beauty of static mixers lies in their ability to achieve a high degree of mixing without moving parts, leading to lower maintenance, improved reliability, and cost-effectiveness in operations. Let’s delve into the specific applications to understand their distinct contributions.
Chemical Processing
Reactions and Product Formation
In chemical processing, static mixers play a vital role in facilitating reactions and product formation. These mixers ensure a uniform distribution of reactants, leading to enhanced reaction kinetics. The main characteristic that makes them so effective is their ability to create a turbulent flow, which promotes better contact between different phases, such as liquid-liquid or liquid-gas mixtures. This characteristic helps accelerate product formation, thus increasing overall yield.
A unique feature of using static mixers in reactions is their simplicity and compact design, allowing for easy integration into existing systems. However, while they excel in enhancing reaction rates, careful consideration is required regarding the viscosity of the fluids being mixed, as high-viscosity materials may present challenges in achieving optimal mixing efficiency.
Sustainability Considerations
Sustainability is a crucial aspect of modern chemical processing, and static mixers contribute significantly in this regard. Their design inherently minimizes energy consumption due to the lack of moving parts, which is often a game changer in industries striving for greener operations. By employing static mixers, companies can reduce waste generation and achieve higher efficiency in their mixing processes.
An important characteristic of static mixers is their ability to maintain consistent mixing quality, which in turn enhances product stability and minimizes the need for added preservatives or additives – a notable advantage in sustainable practices. However, it’s essential to evaluate the lifecycle impact of materials used in these mixers to ensure that sustainability goals are genuinely met.
Food and Beverage Industry
Consistency in Production
Consistency in production is paramount in the food and beverage industry, and static mixers help achieve that goal effectively. These mixers ensure that ingredients are uniformly mixed, which is critical for maintaining flavor profiles and texture in food products. The main benefit of using static mixers here is their ability to handle fluctuations in production volume without sacrificing quality.
A noteworthy feature of static mixers is their adaptability. They can be designed to accommodate varying recipes or formulation changes, thus allowing manufacturers to quickly pivot without extensive downtime. Nevertheless, one must consider the potential need for cleaning and sterilization processes when switching between different food products to avoid cross-contamination.
Quality Assurance
Quality assurance in food production is significantly enhanced by the use of static mixers. These devices provide guaranteed mixing uniformity, which is crucial for regulatory compliance and customer satisfaction. The key characteristic that sets static mixers apart is their ability to work under a wide range of temperatures and pressure conditions, making them suitable for various culinary applications.
A specific advantage of static mixers is their ease of validation for quality assurance protocols. However, their stationary nature means any design flaws could lead to critical mixing inconsistencies, necessitating careful design and testing phases to ensure they meet industry standards.
Wastewater Treatment
Improving Efficiency
In the realm of wastewater treatment, static mixers are indispensable for improving process efficiency. Their role in uniform mixing ensures that chemicals added for treatment are evenly distributed, which optimizes the effectiveness of the treatment process. The standout feature of static mixers in this application is their ability to function effectively under diverse flow conditions while ensuring minimal energy loss.
The advantage of enhancing treatment efficiency equates to lower operational costs and improved compliance with environmental regulations, a pivotal goal for treatment facilities. However, the presence of solids or particulates in wastewater may pose challenges for static mixer design, requiring careful selection and engineering to mitigate blockages.
Regulatory Compliance
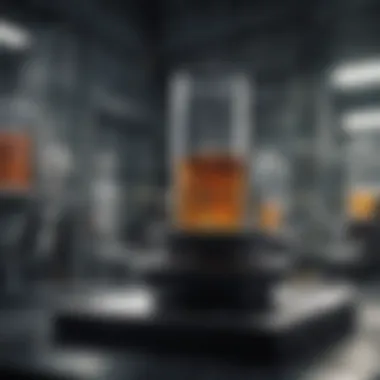
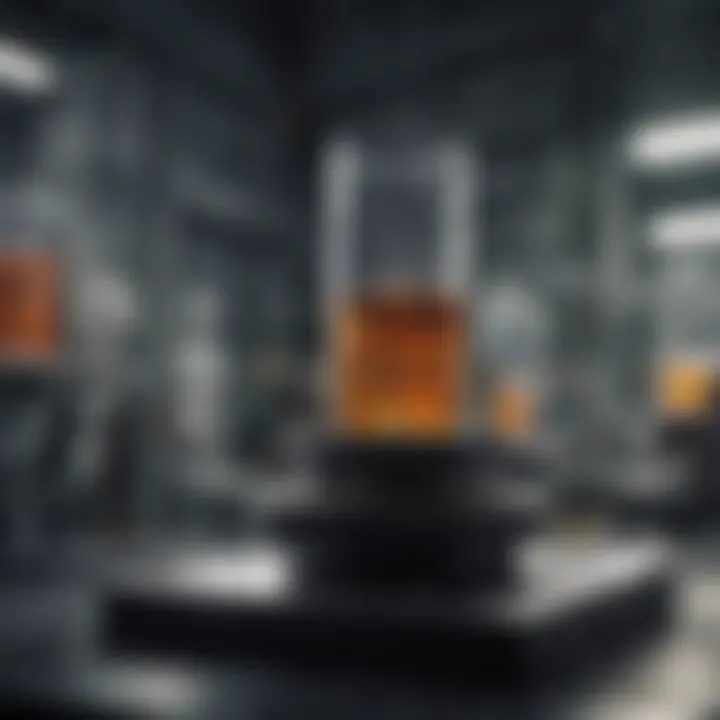
Regulatory compliance is a critical consideration in wastewater treatment, and static mixers support this by maintaining consistent mixing and operational standards. One key characteristic of static mixers is their reliability in producing uniform results, which is crucial for meeting stringent governmental regulations on effluent quality.
Static mixers are also beneficial during inspections, as their simple design allows for easier access to components for maintenance and cleaning. Nevertheless, the challenge lies in ensuring that the materials used in the mixers withstand the corrosive nature of wastewater without compromising performance, which calls for ongoing evaluation of material integrity in long-term applications.
In summary, static mixers stand as pivotal components across multiple industries, optimizing processes and ensuring quality while supporting sustainability efforts.
Challenges in Static Mixer Design
When it comes to static mixer design, there are numerous hurdles that designers and engineers must navigate. These challenges, while complex, are paramount to understanding how effective mixing can be achieved across various industries. The intricate relationships between the properties of fluids, the mixer configuration, and the operational conditions play a crucial role in the overall performance of static mixers. Addressing these challenges not only helps in maximizing efficiency but also in ensuring that the final product meets the necessary quality standards. The following sections will delve into two primary challenges: handling viscous fluids and operational limitations.
Handling Viscous Fluids
Viscous fluids present a unique set of difficulties in the realm of static mixer design. High-viscosity materials, such as polymer solutions or certain food products, require a deeper understanding of flow dynamics. When these fluids enter a static mixer, their thickness can impede effective mixing, often leading to insufficient blending or uneven distribution of components.
- Flow Behavior: The flow patterns of viscous fluids differ significantly from those of less viscous liquids. This variance can create dead zones where mixing is minimal. Designers must select mixing elements that are tailored for handling high viscosity to avoid such issues.
- Pressure Drop Considerations: One has to be cautious with pressure drops when working with viscous materials. A considerable pressure drop across the mixer can be detrimental, as it may lead to increased energy costs. Therefore, it's vital to conduct thorough studies on the pressure loss characteristics of different mixer designs.
- Customization of Mixer Design: Often, a generic mixer configuration is simply not adequate for higher viscosity materials. Custom-designed mixing elements or specific geometrical configurations can enhance performance. Adjustments might include the use of helical elements or specialized vanes that ensure better distribution and mixing efficacy.
- Temperature Control: For some viscous materials, heat can reduce viscosity, improving flow and mixing. However, introducing temperature control systems may add complexity to mixer design, complicating maintenance and operational protocols.
Addressing the challenges posed by viscous fluids is essential, as it directly impacts the efficiency and quality of the final product.
Operational Limitations
Static mixers, while advantageous in many scenarios, also come with operational constraints that need consideration.
- Flow Rate Inflexibility: Static mixers are predominantly designed for specific flow rates. Deviating from these rates can compromise mixing efficiency. If the flow rate is too low, inadequate mixing occurs, while excessively high flow can lead to issues like inadequate residence time for the materials to blend properly.
- Limited Control over Fluid Properties: Unlike dynamic mixers that allow for the adjustment of mixing speeds, static mixers do not facilitate such controls. This can be limiting, especially in applications where varying fluid properties demand adaptability in mixing intensity and speed.
- Maintenance Challenges: Although static mixers are typically low-maintenance due to their lack of moving parts, they are not immune to issues. Over time, some materials can accumulate inside the mixer, leading to blockages or decreased performance. Regular inspections are critical, which may not always be factored into operational budgets.
- Energy Consumption: Static mixers often rely on system pressure to drive the mixing process, leading to questions about energy efficiency compared to other mixer types. Understanding energy consumption patterns is vital to evaluating the overall sustainability of using static mixers.
"Efficiency in design is not just about meeting specifications, it’s about anticipating the demands of materials and processes that are not yet defined."
Navigating these operational limitations is key to optimizing static mixer performance across diverse applications. Keeping these challenges in mind can lead to more refined designs and a better understanding of how to employ static mixers effectively.
Future Trends in Static Mixer Design
The evolution of static mixer design is an ongoing journey, one that constantly adapts to the pressing demands of various industrial sectors. This importance of future trends lies not just in technological advancements, but also in sustainability, efficiency, and overall operational adaptability. Considering the rapid pace of industrial changes, it is vital to look ahead and anticipate how static mixers will integrate new material technologies and computational techniques to optimize fluid mixing processes.
Revolutionizing static mixer design goes beyond mere enhancements; it’s about integrating sustainable practices while boosting the efficacy of the mixing processes. The ability to utilize lightweight, durable materials that can withstand different conditions paves the way for unparalleled efficiency. Moreover, the upcoming trends in computational techniques enable designers and engineers to simulate and analyze mixes far better than ever before. These shifts can lead to reduced waste and improved product quality, laying the foundation for innovative solutions that prioritize environmental responsibility.
Innovative Materials
In recent years, we have witnessed a significant shift towards the utilization of innovative materials in the construction of static mixers. This trend is underscored by the need for enhanced performance, durability, and reduced environmental impact. Materials like advanced composites and specialized polymers are carving out a niche for themselves in mixer design, showing remarkable resilience to corrosive substances and extreme temperatures.
- Lightweight Composites: These materials not only reduce the weight of the mixers but also enhance their strength, allowing for easier installation and maintenance. In industries where mobility is key, lighter components contribute to overall efficiency.
- Biodegradable Plastics: With sustainability becoming a priority, mixers crafted from biodegradable materials address environmental concerns. These materials often showcase adequate mixing capabilities while fulfilling industry regulations on waste reduction.
- Coatings for Longevity: Enhanced coatings offer protection against wear and tear, improving the life span of static mixers. This is just as critical for industries like food processing, where cleanliness and hygiene are vital.
Using such materials opens doors to diverse applications while addressing concerns about performance and ecological impact. A precise material selection can markedly enhance mixing efficiency and reduce energy requirements in the long run.
Advancements in Computational Techniques
The realm of computational techniques has transformed the landscape of static mixer design, enabling designers to foresee challenges and optimize configurations before physical prototypes are built. One of the most powerful tools in this regard is Computational Fluid Dynamics (CFD). It allows for:
- Predictive Analysis: Engineers can model fluid dynamics within mixed environments, enabling them to evaluate how different designs influence the mixing process. Simulations can predict flow patterns and identify potential bottlenecks, leading to more informed design choices.
- Customization: New software allows for the customization of static mixer designs tailored precisely to the needs of specific applications. Whether it's adjusting geometric configurations or material responses, these tools enable a level of precision previously unimaginable.
- Real-time Adjustments: Integrating real-time data acquisition systems allows for on-the-fly adjustments to mixing processes. This leads to greater versatility and adaptability in operational environments, particularly useful in industries like chemical processing where conditions can frequently fluctuate.
The influence of these computational advancements extends beyond mere design; they bring significant advantages in operational efficiency. By decreasing the need for extensive physical testing, time and cost in the development stages diminish significantly, affording companies the opportunity to bring innovative products to market swiftly.
In summary, the future of static mixer design is promising, with innovative materials and computational techniques set to play crucial roles. These emerging trends not only address existing challenges but also pave the way for sustainable and efficient industrial practices.
Closure
The conclusion serves a critical role in summarizing the wealth of insights gathered throughout this exploration of static mixer design. It not only underscores the pivotal points discussed but also illuminates the myriad benefits that stir these concepts together and their implications across industries. Understanding the principles and applications of static mixers helps stakeholders optimize their processes, reduce operational costs, and maintain product consistency.
Recap of Key Insights
To reiterate some of the highlights, here are the major takeaways from our discussion:
- Fundamental Principles: We’ve delved into important mechanical and flow dynamics that dictate how effectively static mixers perform. Recognizing the interplay between viscosity and flow conditions is crucial for any effective design.
- Component Effectiveness: The types and geometry of static mixing elements can significantly alter mixing efficiency. Choices made here have long-term ramifications on performance metrics.
- Material Suitability: Selecting the right materials, particularly considering factors like corrosion resistance and durability, is essential for ensuring a static mixer’s longevity and operational integrity.
- Performance Metrics: Evaluating efficiency and understanding pressure drop dynamics allows engineers to fine-tune their designs and achieve optimal outcomes.
- Future Directions: As technology evolves, new materials and computational techniques offer exciting prospects for enhancing the capabilities of static mixers.
Final Thoughts on Static Mixer Design
Reflecting upon static mixer design opens up avenues for innovation and improvement. The key lies in grasping not just the static aspects but also how dynamic the mixing processes are. Industries are constantly looking for ways to adapt to changing regulations and market demands, making it crucial to embrace ongoing research and development.
It is our hope that what has been explored here serves as more than just a reference. This compendium can act as a launchpad for further inquiries into static mixer applications. Whether it's in chemical processing, food production, or wastewater management, these mixers are more than functional parts; they are integral to achieving efficiency and quality. With continued advancements on the horizon, the significance of static mixers in various sectors is set to expand, providing a canvas for future innovation.
Importance of References
References act as a roadmap, guiding students, researchers, educators, and professionals through the intricate landscape of static mixer design. Here’s why having well-cited references is vital:
- Credibility: Linking to reputable sources, such as academic papers or industry standards, lends weight to the arguments being made. A citation from a scholarly article in a journal like "Chemical Engineering Science" can significantly bolster the validity of claims regarding mixer efficiency.
- Broadening Perspectives: Engaging with various studies and opinions allows readers to grasp the multifaceted nature of the subject. This is particularly important in static mixer design, where numerous parameters may influence outcomes, such as fluid properties and mixer geometry.
- Referencing Advancements: The field of static mixers is continually evolving due to technological advancements. Citing up-to-date sources ensures that the information reflects current trends and methodologies, keeping the discussion relevant.
Specific Elements to Consider
When discussing static mixers, it’s essential to reference specific elements that may contribute to a deeper understanding:
- Design Methodologies: By referencing studies that focus on Computational Fluid Dynamics (CFD) or empirical methodologies, the reader can see how simulation and experimental techniques have shaped how mixers are designed today.
- Material Properties: Citing research on material science, especially regarding corrosion and wear resistance, adds significant value. Choosing appropriate materials directly impacts the longevity and effectiveness of a static mixer.
- Performance Metrics: Including references to performance evaluations in industrial applications shows how theoretical knowledge translates to practical use. Metrics like mixing efficiency and pressure drop are often well documented in engineering reports.
Benefits of Comprehensive References
Incorporating an array of references throughout the article brings numerous benefits:
- Enhanced Learning: Readers are equipped with a path to further explore the subject matter, fostering a deeper understanding of static mixers. They can pursue areas of interest more extensively through linked studies.
- Analytical Framework: Strong references provide an analytical backdrop, allowing professionals to compare and contrast different designs and approaches based on empirical evidence.
- Encouragement of Innovation: By highlighting cutting-edge research and innovative findings, the text inspires future advancements in the field of static mixer design, spurring continued exploration and experimentation.
As a final note, the inclusion of references shapes the entirety of the discussion. Instead of existing in a vacuum, the information connects to a larger body of knowledge, emphasizing that static mixer design is a dynamic field, continuously informed by research and application. Readers who dive into the references cited here may unlock new insights, paving the way for advancements that could transform their own practices.