In-Depth Analysis of Strain Gauges for Crack Monitoring
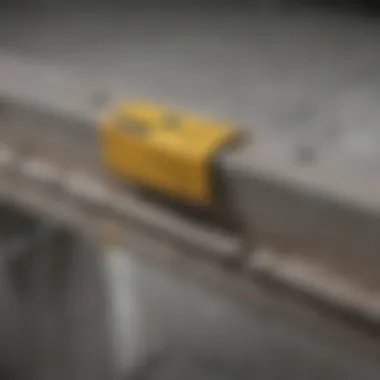
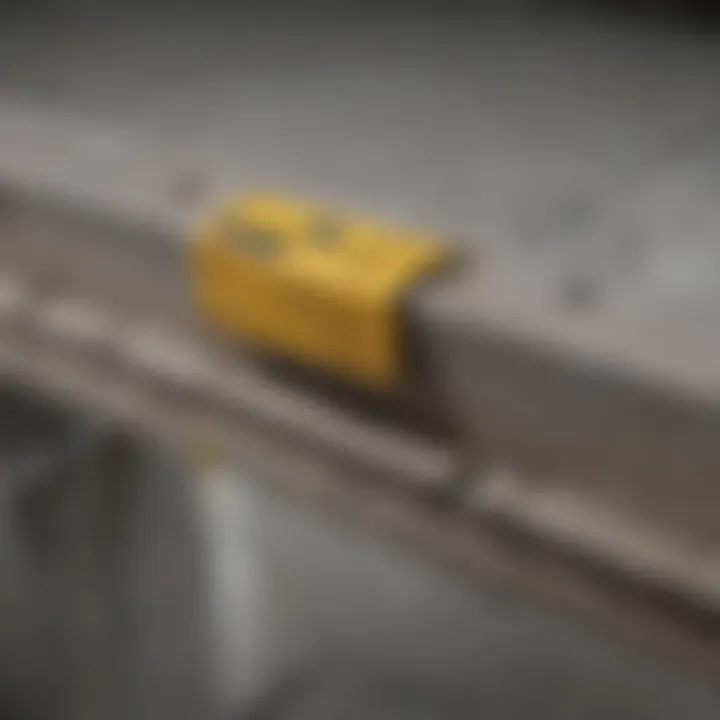
Intro
Crack monitoring in structural engineering is a critical aspect of maintaining safety and integrity in various materials. As structures age and experience environmental stressors, the likelihood of crack formation increases. This raises the need for effective monitoring methods that can provide real-time insights into the health of these structures. Strain gauges emerge as a reliable solution in this regard.
Strain gauges are devices that measure strain on an object. They are vital for understanding how structures respond to various forces. Their application in crack monitoring not only helps in detecting the presence of cracks early but also in understanding the load conditions that contribute to crack propagation. This article examines the principles underlying strain gauges, the technologies available, and their application in monitoring crack formation.
Research Overview
Key Findings
Strain gauges have been proven to be effective for crack monitoring in multiple contexts. From bridges to buildings, their integration has led to improved safety outcomes. Some key findings include:
- Sensitivity: Strain gauges can detect minute changes, enabling early identification of cracks.
- Versatility: They can be used on various materials, including metals, plastics, and concrete.
- Real-time Monitoring: Many modern setups allow continuous data collection, aiding proactive maintenance decisions.
Study Methodology
The methodologies used in studies of strain gauges focus on their design and deployment. Researchers typically follow these steps:
- Selection of Gauge: Choosing the appropriate strain gauge based on the material and expected strain levels.
- Installation: Careful placement and bonding to the target surface to ensure accurate readings.
- Data Collection: Utilizing data loggers to capture strain measurements over time.
- Analysis: Comparing data against established thresholds to interpret structural performance.
Background and Context
Historical Background
The use of strain gauges dates back to the mid-20th century. While their early applications were primarily in aerospace and automotive industries, the adaptability of strain gauges has since led to widespread usage in civil engineering. This evolution reflects a growing awareness of the need for preventive measures in infrastructure management.
Current Trends in the Field
Recent advances have introduced digital strain gauges, enhancing data accuracy and reliability. Integration with Internet of Things technologies allows remote monitoring and access to data via mobile devices. These developments indicate a shift towards more interconnected and informed systems in structural engineering.
"The adoption of strain gauges in crack monitoring represents a significant advancement in proactive structural integrity management."
Prelude to Crack Monitoring
Crack monitoring plays a critical role in maintaining the integrity of structures. It is essential for safety and longevity in various industries, from construction to aerospace. Monitoring cracks helps identify potential problems before they escalate into serious failures. A proactive approach reduces costs associated with repairs and potential disasters, making it vital in engineering.
In this article, we will explore the nuances of crack monitoring, particularly through the use of strain gauges. Understanding any structure's behavior under stress and strain is not just relevant but imperative. Strain gauges serve as effective tools, providing detailed insights into structural health. They help detect early signs of distress that would otherwise go unnoticed.
The integration of crack monitoring methods enhances the safeguarding of infrastructures, thus emphasizing their value in modern engineering. Research into strain gauge technology demonstrates the advancing nature of monitoring systems, ensuring that we stay ahead of the challenges in structural safety. This article illustrates the relevance of these techniques and underscores why they should be integral components of any engineer's toolkit.
Fundamentals of Strain Measurement
Understanding the fundamentals of strain measurement is essential for effectively applying strain gauges in crack monitoring. Strain gauges measure the deformation (strain) of materials, providing critical data to assess structural integrity. Precise strain measurement is necessary to track the behavior of materials under load, stress, and other external factors. This understanding supports effective monitoring and management, ultimately contributing to the safety and longevity of structures.
Definition of Strain
Strain is a measure of deformation representing the displacement between particles in a material body. It is expressed as the change in length relative to the original length. Mathematically, strain is defined as:
[ \textStrain (\epsilon) = \frac\Delta LL_0 ]\
Where ( \Delta L ) is the change in length and ( L_0 ) is the original length. Strain can be classified into two main types: normal strain, occurring in the direction of the applied force, and shear strain, which occurs in response to forces applied at an angle. Understanding this concept is crucial, as it allows engineers to predict how materials will react under various conditions.
Strain Gauge Working Principle
The strain gauge operates on a simple electro-mechanical principle. It consists of a thin metallic foil arranged in a grid pattern, which is bonded to the surface of a material. When the material experiences deformation, the foil stretches or contracts, causing a change in its electrical resistance. This change can be accurately measured and correlated to the strain experienced by the material.
The relationship between the strain and the change in resistance is expressed by the gauge factor, defined as:
[ \textGauge Factor = \frac\Delta R / R_0\epsilon ]\
Where ( \Delta R ) is the change in resistance, ( R_0 ) is the original resistance, and ( \epsilon ) is the strain. The higher the gauge factor, the more sensitive the strain gauge is to deformation.
Strain gauges can be categorized based on their material composition. For example, metallic strain gauges are commonly used due to their high sensitivity and reliability, while semiconductor strain gauges offer even higher sensitvity but are typically more brittle. Each type has specific applications, depending on the environmental and material conditions involved.
In practice, the application of strain gauges provides engineers with valuable insights into the structural health of materials. This can be particularly essential in civil engineering applications where understanding the deformation behavior of beams, bridges, or any structural components can prevent catastrophic failures.
"Accurate strain measurement directly correlates with the safety and reliability of structures, making it a key focus in monitoring methodologies."
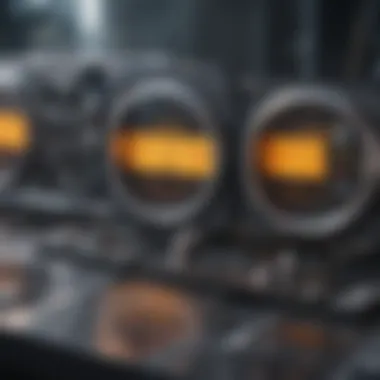
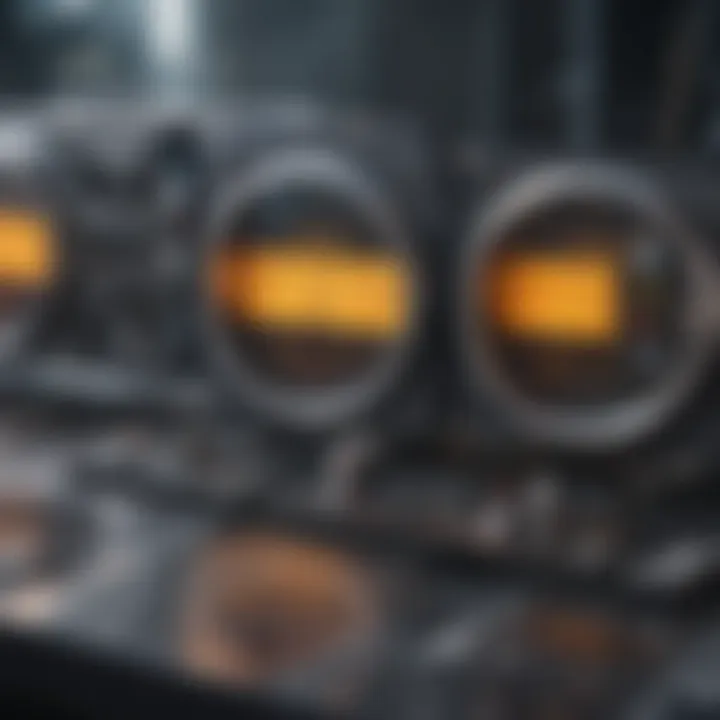
By grasping the fundamentals of strain measurement, professionals can effectively utilize strain gauges to enhance their crack monitoring efforts and maintain structural integrity.
Types of Strain Gauges
Understanding the types of strain gauges is essential in the context of crack monitoring as each type has unique characteristics that determine suitability for specific applications. The selection process involves considering various factors such as sensitivity, temperature resistance, and the environmental conditions the gauges will be exposed to. Proper knowledge of these categories ensures effective monitoring of structural integrity, thereby preventing catastrophic failures.
Metallic Strain Gauges
Metallic strain gauges are among the most common types used in engineering and structural monitoring. They consist of a metallic wire or foil arranged in a grid pattern. When mechanical stress is applied, the metal gauge changes its resistance due to deformation. This alteration in resistance is measured and correlated to the strain experienced by the material.
The benefits of metallic strain gauges include:
- Cost-effectiveness: They are widely available and reasonably priced.
- Robustness: These gauges can withstand harsh environments and mechanical stresses.
- Linearity: They provide a predictable response, making calculations straightforward.
However, there are considerations when using metallic strain gauges. They may suffer from temperature sensitivity, leading to less accurate readings if the temperature fluctuates significantly. Moreover, their installation requires careful surface preparation to ensure proper bonding and performance.
Semiconductor Strain Gauges
Semiconductor strain gauges operate on a different principle compared to metallic variants. Utilizing silicon or germanium, these gauges are significantly more sensitive and can detect much smaller changes in strain. The semiconductor material exhibits a high gauge factor, which means that the change in electrical resistance is proportionally higher than that of metallic gauges.
The advantages of using semiconductor strain gauges include:
- High sensitivity: They can measure minute strains accurately, making them ideal for applications where precision is paramount.
- Compact size: Their smaller footprint allows for installation in constrained spaces.
Despite these benefits, semiconductor gauges are more expensive and can be more complex to interface with data acquisition systems. They also tend to be more sensitive to temperature variations, necessitating careful compensation strategies during measurement.
Optical Strain Gauges
Optical strain gauges represent a modern approach to crack monitoring. Utilizing the principles of light transmission through optical fibers, these gauges measure strain by detecting changes in the light properties as they pass through the gauge. Optical gauges are inherently immune to electromagnetic interference, making them suitable for challenging environments.
Key features of optical strain gauges include:
- Non-contact measurement: They can monitor strain without physically interacting with the material, reducing potential damage.
- Long-distance monitoring: Optical fiber can transmit data over significant distances without loss of quality, useful in large structures.
Nevertheless, optical strain gauges often require sophisticated data acquisition and processing systems, which can increase the overall project cost. Additionally, while they can provide excellent long-term performance, their initial setup may be more complex compared to traditional gauges.
Overall, the choice of strain gauge type directly impacts the effectiveness and accuracy of crack monitoring systems. Understanding the unique benefits and limitations of each type is crucial for practitioners in structural engineering.
Methodologies for Crack Monitoring
Proper methodologies for crack monitoring are vital. They ensure that infrastructure and various structures remain safe and functional over time. The techniques used for crack monitoring significantly impact data reliability, installation success, and overall monitoring effectiveness. Understanding these methodologies helps in choosing the right tools and processes to use for real-world applications.
Installation Techniques
Installation is the first step in effective crack monitoring. It requires precise methods to ensure that strain gauges perform optimally. There are several techniques to consider:
- Surface Mounting: This method involves adhering the strain gauge directly to the material surface. It is economical but can affect the gauge's accuracy due to environmental factors.
- Drilled Installation: Here, a hole is drilled into the material, and the strain gauge is placed within it. This provides better protection against external influences but is more invasive.
- Adhesive Bonding: This technique relies on a specialized adhesive to attach the gauge. Proper surface preparation is crucial to avoid errors and ensure the gauge reads accurately.
Each method has its benefits and challenges. Choosing the right installation technique depends on the material being monitored, environmental conditions, and the potential impact on the structure.
Data Acquisition Systems
Data acquisition systems (DAS) play an important role in crack monitoring. They collect data from strain gauges and convert it into usable information. The systems should have:
- High Sampling Rates: To capture changes accurately, especially at critical times when cracks may develop.
- Remote Monitoring Capability: This is essential for large or hard-to-reach locations, providing the ability to monitor from a distance.
- Integration with Other Sensors: Having multiple types of sensors can offer a more comprehensive overview of the structural integrity.
Ultimately, data acquisition systems should be reliable, easy to operate, and capable of providing real-time data.
Signal Processing Methods
Once the data is collected, effective signal processing methods are necessary. They help interpret the raw data into meaningful insights. Key methods include:
- Filtering: This removes noise from the signals, ensuring clarity in measurements. Low-pass filters are commonly used to eliminate high-frequency noise.
- Statistical Analysis: Various statistical techniques can analyze the data patterns over time, helping to identify trends that indicate potential issues.
- Machine Learning: This emerging field provides advanced capabilities in predictive analytics. Algorithms can learn from historical data and predict when and where cracks may develop.
Incorporating these signal processing methods improves the quality of the data and enhances the understanding of structural health. Overall, methodologies for crack monitoring are critical. They ensure safety and efficacy over the life of structures.
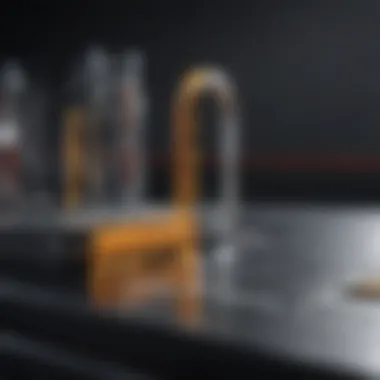
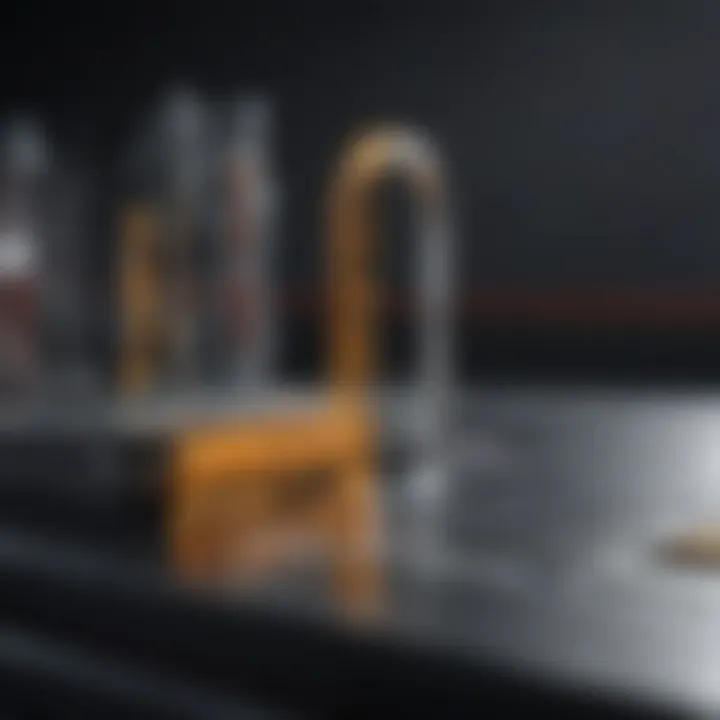
Advantages of Strain Gauge Monitoring
Strain gauge monitoring plays a crucial role in ensuring the structural integrity of materials and infrastructures with cracks or potential failure points. By utilizing these monitoring systems, engineers and researchers can obtain valuable insights into the behavior of structures under various loads and environmental conditions. This section discusses the specific advantages of strain gauge monitoring, focusing on precision in measurements and real-time monitoring capabilities that enhance overall assessment and decision-making processes.
Precision in Measurements
Precise measurements are fundamental in crack monitoring to predict potential failures in structural elements. Strain gauges provide accurate readings of deformation caused by stress, allowing for detailed assessment of material behavior. Unlike other measurement techniques, strain gauges can detect minute changes in strain, contributing to a more nuanced understanding of how cracks develop over time.
The precise data obtained from strain gauges can help:
- Identify critical stress points within a structure.
- Monitor the effectiveness of repairs or reinforcements.
- Validate structural integrity against design specifications and safety standards.
Moreover, the high sensitivity of metallic and semiconductor strain gauges enables them to capture data in a wide range of conditions, including temperature fluctuations. The correct installation and calibration of these devices enhance their precision further, ensuring that the results are reliable for engineering analyses and decisions.
Real-Time Monitoring Capabilities
One notable advantage of strain gauges is their ability to provide real-time data. This capability is vital in situations where immediate responses to structural changes are necessary. Continuous monitoring using strain gauges enables:
- Timely detection of unforeseen stress accumulations and crack growth.
- Immediate alerting systems that can trigger safety protocols or maintenance actions.
- Enhanced long-term data collection for analyzing trends and predicting potential failures based on historical performance.
With the integration of wireless monitoring systems, real-time data can be transmitted efficiently to monitoring stations. This advancement reduces the need for physical inspections and allows for immediate response to critical changes. Real-time monitoring can lead to more efficient management of infrastructure, ensuring safety and longevity in various applications.
"The integration of strain gauge monitoring systems marks a significant advancement in structural health monitoring, allowing professionals to make informed decisions based on quantifiable data."
Limitations of Strain Gauges
Understanding the limitations of strain gauges is crucial for proper application in crack monitoring. While they offer significant advantages for real-time monitoring and high precision, they have some drawbacks that users must consider. It is essential to assess these limitations to ensure the reliability and effectiveness of strain gauge measurements in various applications.
Temperature Sensitivity
Strain gauges typically exhibit temperature sensitivity, which can influence their measurements. Changes in temperature can cause the gauge to expand or contract, leading to readings that may not accurately represent the strain experienced by the material.
For instance, a metallic strain gauge may show increased resistance as the temperature rises, leading to false positive strain readings. This phenomenon highlights the need for careful calibration under varying temperature conditions. Users can mitigate this issue by implementing temperature compensation methods, but this adds complexity to the monitoring system.
To manage temperature sensitivity, several strategies can be employed:
- Use of temperature compensating materials: Some strain gauges are designed with materials that can counteract temperature effects.
- Calibration protocols: Regular calibration under expected environmental conditions can help maintain measurement accuracy.
- Integrated temperature sensors: Incorporating temperature sensors alongside strain gauges allows for data correction, providing a clearer picture of the structural integrity being monitored.
Potential Damage to Materials
Another significant limitation of strain gauges is the potential for damage to the materials they are monitoring. The installation process can involve adhesive bonding or drilling into the material, which may compromise structural integrity.
Moreover, if a strain gauge is improperly applied, it can introduce stress concentrations around its attachment site, leading to premature failure or false strain readings. This is particularly critical in sensitive structures where every small change matters.
To minimize the risk of such damage:
- Select appropriate installation techniques based on the material type and environment.
- Conduct pre-installation assessments to understand the physical characteristics of the materials in question.
- Prefer non-invasive methods whenever possible, which include surface mounting techniques that do not require surface penetration or alteration.
"Strain gauges must be used with consideration for their impact on both the materials and the accuracy of the readings they produce."
Integration with Modern Technologies
The advent of modern technologies has significantly transformed the landscape of crack monitoring. Integration with advanced tools not only enhances the capabilities of traditional strain gauges but also propels the field into a new era of precision and efficiency. The importance of this integration lies in several specific elements: enhanced data collection, improved monitoring accuracy, and real-time analysis of structural integrity. These advancements provide professionals in structural engineering a more robust framework for decision making.
Wireless Monitoring Systems
Wireless monitoring systems have emerged as a vital component of contemporary crack monitoring strategies. These systems eliminate the need for cumbersome wires and allow for more flexible sensor placements. The use of wireless technology simplifies the installation process, making it easier to deploy strain gauges in hard-to-reach areas. Furthermore, they enable the collection of data from multiple sensors simultaneously without interrupting the environment.
The benefits of wireless monitoring systems include better scalability and adaptability. Engineers can add or reposition sensors based on evolving project demands. This adaptability is crucial in construction and maintenance phases, where structural dynamics may change over time.
However, several considerations must be taken into account. Secure data transmission is paramount; systems must employ encryption and robust communication protocols to prevent unauthorized access. Power management is also an essential factor. Many wireless sensors operate on batteries and require energy-efficient designs to ensure longevity.
Data Analysis Using AI
Artificial Intelligence (AI) plays a critical role in the analysis of data collected from strain gauges. As the volume of monitoring data grows, traditional data analysis methods become insufficient for deriving meaningful insights. AI algorithms can process vast amounts of data quickly and identify patterns that might not be visible to human analyst. This leads to improved predictive maintenance and risk assessment.
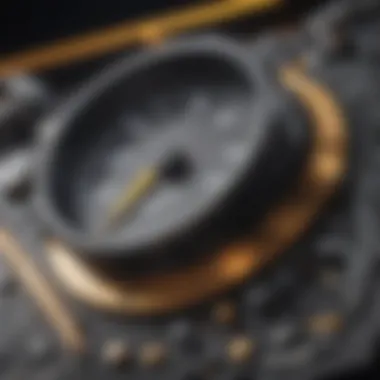
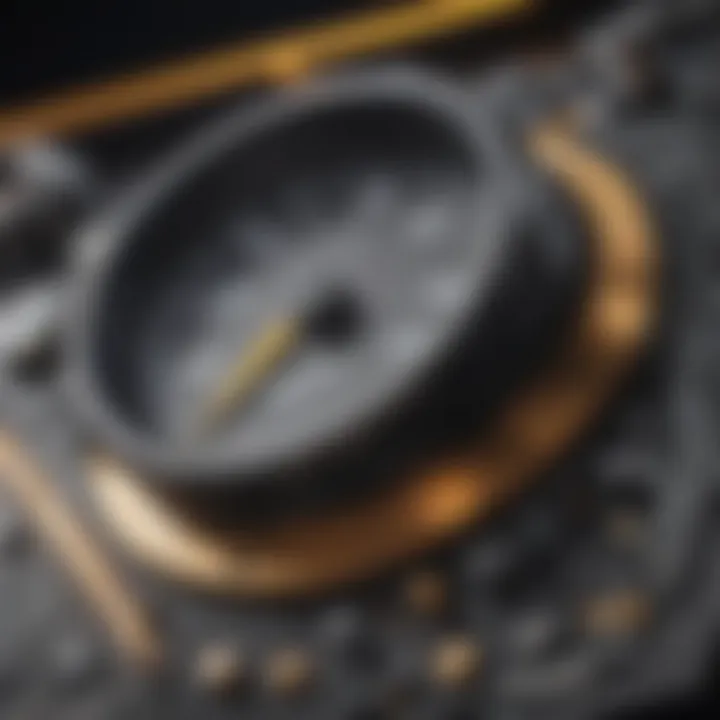
Key applications of AI in data analysis include anomaly detection, trend analysis, and predictive modeling. Anomaly detection algorithms can flag unusual strain readings promptly, allowing engineers to take immediate action to prevent structural failure. Trend analysis helps in understanding how strains evolve over time, while predictive modeling can forecast potential crack developments based on historical data.
"AI enhances our ability to interpret strain gauge data, offering deeper insights into structural health than ever before."
The integration of AI in crack monitoring brings its own challenges. Data quality is crucial, as inaccurate or noisy data can lead to misleading results. Therefore, ensuring high-quality measurements is fundamental before employing AI techniques.
Case Studies in Crack Monitoring
Understanding how strain gauges can be applied through real-world cases provides invaluable insights into their effectiveness for crack monitoring. This section emphasizes the significance of various case studies, showcasing how they illuminate practical applications of strain gauge technology and the insights derived from these implementations. Detailed case studies enhance our comprehension of operational challenges, benefits of using strain gauges, and valuable lessons learned through their application in diverse scenarios.
Infrastructure Applications
Infrastructure is crucial to sustaining modern society, making its integrity essential. The application of strain gauges in fields like bridges, dams, and buildings ensures timely detection of cracks, which might otherwise lead to catastrophic failures.
One compelling case study can be found in the bridge monitoring system used in the Edinburgh Gateway Project in the UK. Here, metallic strain gauges were installed throughout the structure to provide continuous data on stress and deformation. This approach allowed engineers to monitor strain in real-time, mitigating the risks associated with unforeseen stress concentration due to environmental factors or heavy traffic loads. The outcome highlighted how proactive monitoring could extend the lifespan of infrastructure while ensuring safety.
Another illustrative example comes from the Hoover Dam where semiconductor strain gauges monitored concrete strain under varying temperature and loading conditions. The data collected not only informed maintenance schedules but also played a vital role in assessing the dam’s overall structural health.
Geotechnical Applications
Geotechnical engineering also benefits significantly from strain gauge technologies. Soil stability is complicated, particularly in construction zones where subsurface conditions might be unpredictable. By integrating strain gauges, engineers can effectively monitor stress changes within soil and rock structures.
A notable case study involves the use of optical strain gauges during the construction of a tunnel in a seismic zone. The Einich Tunnel Project in Italy employed these gauges to monitor ground deformation in real-time. This monitoring enabled the team to make necessary adjustments to construction methods as the project progressed, ultimately preventing potential failures.
Moreover, the use of strain gauges in slope stability assessments has been documented in various landslide studies. One such example can be seen in the investigation of the Anderson Creek Landslide, where gauges provided critical data on strain changes in the soil, allowing engineers to predict potential landslide movements. This application not only aids in mitigation planning but also equips researchers with necessary data to explore better predictive models for future projects.
Modern applications of strain gauges are pivotal in understanding structural health, allowing for informed decision-making in the field of engineering.
These case studies exemplify how strain gauges are applied in practice, illuminating both the versatility and effectiveness of the technology in relevant fields. They affirm the necessity of integrating such monitoring systems into construction and maintenance practices, facilitating safer and more durable structures in diverse applications.
Future Trends in Crack Monitoring
Understanding future trends in crack monitoring is essential for advancing structural engineering practices. The growing complexity of infrastructures and the increasing emphasis on safety make it imperative to look towards innovative solutions. Strain gauges play a critical role in this evolution, as they provide precise data on material integrity. Developing this understanding will benefit not only researchers but also practitioners in the field.
Innovations in Sensor Technology
The field of sensor technology is advancing rapidly, leading to improved performance in crack monitoring. Innovations in micro-electromechanical systems (MEMS) are making sensors more sensitive and compact. This means strain gauges can now be placed in tighter configurations, capturing data in more locations than before.
Wireless technologies are also revolutionizing how monitoring is conducted. Traditional wired systems have limitations in installation and data retrieval. In contrast, wireless sensors allow for real-time data transmission, significantly improving the monitoring process. These advancements lead to reduced manual labor and increased accuracy over time.
Another important development is the integration of nanotechnology into strain gauges. This enhancement allows for smaller, yet incredibly responsive sensors. Such technologies can detect minuscule changes in strain, providing insights that were previously unattainable.
"The future of sensing technology lies in its precision and adaptability, ensuring infrastructure safety like never before."
Increased Emphasis on Sustainability
As global awareness of environmental impacts increases, sustainability has become a guiding principle in engineering practices. In crack monitoring, sustainable materials are gaining attention. Strain gauges are now being manufactured from eco-friendly materials, reducing the carbon footprint associated with traditional manufacturing processes.
Furthermore, the emphasis on sustainability translates to life-cycle analysis of materials used in construction. Engineers are increasingly tasked with monitoring not only the structural integrity but also the impact of materials on ecosystems. This holistic approach fosters more responsible usage of resources, ensuring that environmental safety is considered alongside structural safety.
Coupled with sustainability efforts is the trend toward smart materials. These materials adapt based on environmental conditions and can provide self-monitoring capabilities. Integrating such technologies with strain gauges can lead to a paradigm shift, where ongoing assessments occur without extensive human intervention.
The integration of these two trends—innovations in sensor technology and sustainability—indicates a promising future for crack monitoring. These developments not only ensure safety and reliability but also align with broader societal goals of minimizing environmental footprint.
End
The examination of strain gauges for crack monitoring is crucial in understanding the integrity of various structures. As discussed throughout the article, these devices provide essential insights into stress and deformation, informing maintenance decisions and enhancing safety measures. The role of strain gauges extends beyond mere measurements; they contribute significantly to long-term structural health monitoring. In this conclusion, we summarize vital findings and discuss their significance.
Summary of Key Findings
Throughout this article, several critical points stand out regarding the implementation of strain gauges for crack monitoring:
- Precision Measurement: Strain gauges deliver accurate data on stress and strain, enabling engineers to detect issues early.
- Versatile Applications: These gauges can be applied across multiple domains, including infrastructure and geotechnical settings.
- Modern Technological Integration: The advent of wireless monitoring systems and data analysis techniques utilizing artificial intelligence enhances the effectiveness of traditional methods. The integration of these technologies allows for real-time data tracking and analysis, making the monitoring process more efficient and responsive.
- Challenges Identified: Although strain gauges are invaluable, the article highlights some limitations, such as temperature sensitivity and the potential for damaging materials during installation.
Implications for Future Research
Future research in the field of crack monitoring with strain gauges should focus on several key areas:
- Enhanced Sensor Design: There is a need for improved strain gauge technology that minimizes weaknesses, particularly temperature sensitivity and damage risk.
- AI and Machine Learning Integration: Continued exploration in the use of AI could provide deeper insights from the data collected, facilitating better predictive maintenance strategies.
- Broader Application Studies: Investigating the performance of strain gauges in various environments and conditions could expand their usage and improve robustness.
- Sustainability Efforts: Research should also consider developing environmentally friendly materials for strain gauges, aligning with the global push for sustainability in engineering practices.
By focusing on these implications, future advancements could significantly refine crack monitoring processes, ensuring safer structures and prolonging the lifespan of various materials.