Exploring Synthetic Thermoplastic Polymers and Their Impact
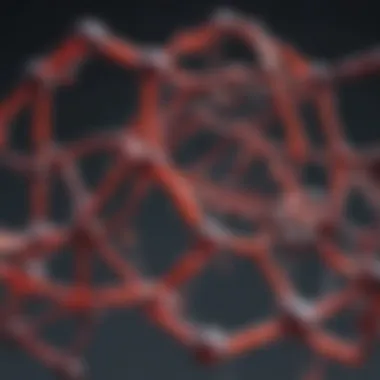
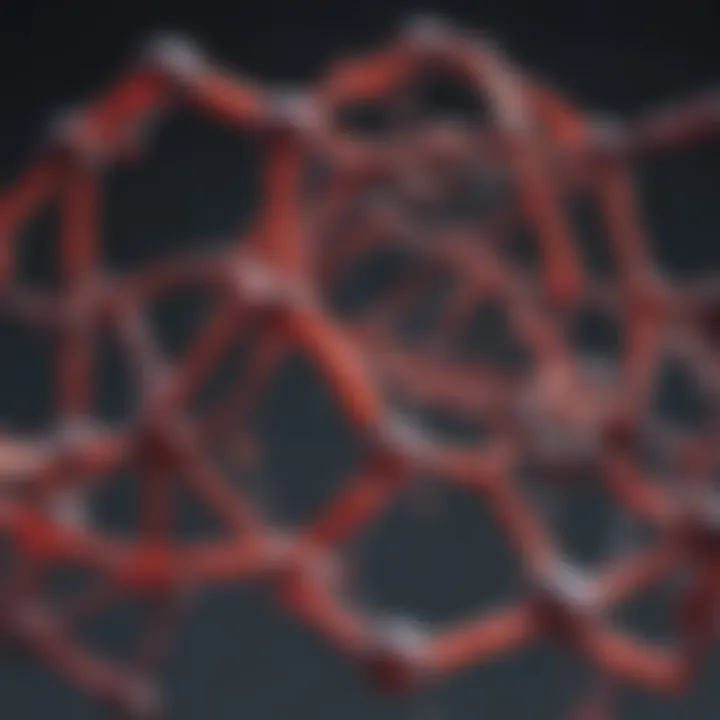
Intro
Synthetic thermoplastic polymers have revolutionized various industries by providing materials that are versatile, durable, and adaptable. Their importance cannot be overstated, as they seamlessly blend into many aspects of modern life—from packaging to automotive components. The fascinating blend of chemical composition, mechanical properties, and real-world applications makes this subject both complex and enriching.
These polymers often exhibit unique traits tailored to specific industrial uses, making them essential in the development of cutting-edge technologies. Their production processes have continually evolved to suit the growing demand for innovative materials. However, it’s not all roses; the increasingly important dialogue around sustainability reveals some significant environmental impacts tied to their production and disposal.
Examining synthetic thermoplastic polymers involves delving into critical aspects, including:
- Chemical structure and composition that defines their properties
- Manufacturing methodologies that influence performance and applications
- Mechanical characteristics that determine usability in various settings
- Environmental considerations, addressing the challenges posed by their lifecycle
Understanding these components is crucial for students, researchers, and professionals who are navigating this rapidly changing domain and aiming to drive future innovations. As we explore this field, we'll highlight key findings and current trends to provide a deeper insight into synthetic thermoplastic polymers.
Foreword to Synthetic Thermoplastic Polymers
Synthetic thermoplastic polymers play a crucial role in modern materials science and manufacturing. As versatile substances, they have woven themselves into the fabric of countless industries, ranging from automotive to healthcare. These polymers are engineered for performance, offering remarkable flexibility in applications which derive from their unique molecular structures.
In this article, we will delve into the world of synthetic thermoplastic polymers, unpacking their composition, properties, and uses. It's not just a matter of understanding what they are; it's about recognizing their significance in contemporary innovations and sustainability efforts. With the ability to be molded and reshaped, thermoplastic polymers have their own set of behavioural nuances that necessitate a closer look.
Definition and Characteristics
Synthetic thermoplastic polymers are a category of plastics that become soft when heated and return to a solid state upon cooling. This property allows them to be formed into a variety of shapes, making them incredibly advantageous in manufacturing processes.
One key characteristic that distinguishes these materials is their amorphous or semi-crystalline nature. For instance, polyethylene and polystyrene exhibit distinct structural traits that influence their application. Polyethylene presents a good balance of flexibility and toughness, while polystyrene is known for its rigidity and clarity.
Another significant aspect is their susceptibility to thermal cycles, which leads to controlled deformation without breaking. They can be easily reprocessed and remolded, aiding in recycling efforts and reducing waste. This functionality finds them not just in everyday products like containers and toys, but also in more specialized applications, such as medical devices.
Historical Development
The journey of synthetic thermoplastic polymers is marked by innovation and evolving technology. The first synthetic plastic, Bakelite, was invented in the early 20th century. This marked a groundbreaking step in materials science, where for the first time, man-made substances began to mimic natural materials.
Following Bakelite, the introduction of low-density polyethylene in the 1930s was a game changer. It paved the way for the widespread use of plastic, being lightweight yet durable. As the decades rolled on, advancements in polymer chemistry gave rise to an array of new synthetic thermoplastics, each developed for specific properties and functionalities.
The latter half of the 20th century saw significant growth in the use of these polymers across various fields. The automotive sector, for example, adopted them for their lightweight and cost-efficient benefits, reshaping how vehicles are constructed. Today, the focus has also shifted towards sustainability, with newer polymers being developed to reduce environmental impacts.
Synthetic thermoplastic polymers are not just products of haste but reflect a deep understanding of material science and engineering. Their evolution marks a timeline of innovation that combines scientific progress with consumer needs, paving the way for future advancements in this fascinating field.
Chemical Composition
Understanding the chemical composition of synthetic thermoplastic polymers is critical for grasping their functionalities and myriad applications. The specific arrangement of atoms and the bonds that form between them dictate not only the physical properties of these materials but also their performance in real-world applications. As we delve into monomer structures and polymerization processes, we see how these foundational aspects influence everything from flexibility to heat resistance.
Monomer Structures
Monomers act as the basic building blocks of polymers; they are the smallest units that can chemically bond to create larger structures. The choice of monomer largely determines the characteristics of the resultant polymer. For example, polyethylene is made up of recurring ethylene, while polystyrene derives from styrene monomers. Each monomer has its unique characteristics that directly affect properties like rigidity, clarity, and chemical resistance.
In practical terms, if you mix certain monomers in specific ratios, you can tweak the final product significantly. This versatility is one of the main attractions of synthetic thermoplastic polymers. Manufacturers can tailor materials to meet specific standards, whether for durability or aesthetic qualities.
Polymerization Processes
The processes of converting monomers into polymers can happen through either addition or condensation polymerization.
Addition Polymerization
Addition polymerization involves the direct linkage of monomer units with the release of no additional byproducts; it is a straightforward method. This characteristic makes it a popular choice among industries aiming for efficiency. The key aspect of this process lies in the ability to form long chains with remarkable mechanical properties.
Benefits of addition polymerization include:
- High molecular weight: It allows for stronger materials suitable for structural applications.
- Controlled properties: By altering reaction conditions, the properties of the final polymer can be fine-tuned.
However, addition polymerization can struggle with producing uniform products as well as being sensitive to conditions like temperature and pressure. If not controlled, these variables can lead to an increase in defects in the final product.
Condensation Polymerization
On the other hand, condensation polymerization involves the reaction of monomers that results in the loss of a small molecule, often water. This unique aspect gives the process a different flavor altogether. One of its significant contributions is the ability to form high-performance polymers; Nylon is a classic example, showcasing excellent wear resistance and strength.
The advantages of this method include:
- Multifunctionality in products: The possibility to create materials with diverse functionalities due to the introduction of various side groups during polymerization.
- Adaptability in applications: The polymers can find use in various sectors, from textiles to automotive parts.
That said, condensation polymerization often requires more precise control over reaction conditions, and the generation of byproducts can complicate processing and purification.
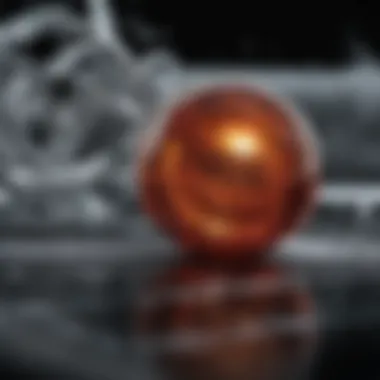
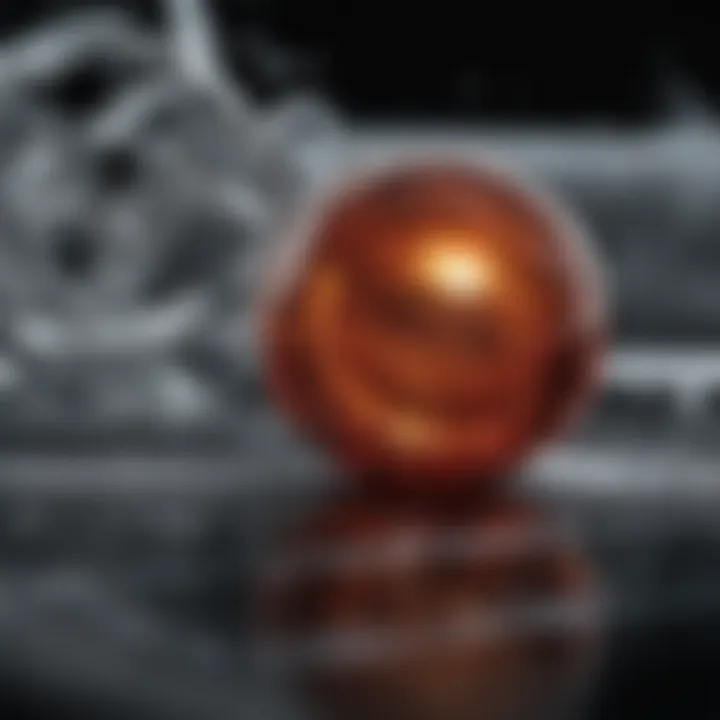
In summary, the chemical composition of synthetic thermoplastic polymers is not only critical for understanding their properties but also lays the groundwork for innovation in various applications. By exploring the intricacies of monomer structures and the nuances of polymerization processes, we open the door to discovering new applications and improving existing technologies.
Types of Synthetic Thermoplastic Polymers
Understanding the various types of synthetic thermoplastic polymers is crucial for both academic and industry professionals. Each polymer brings a distinct set of properties and applications that cater to a myriad of needs. Natural materials have served humanity well for a long time, but synthetic thermoplastics offer a flexibility and functionality that often surpass their traditional counterparts. The significance of focusing on types lies in recognizing their individual characteristics, which can be a game-changer in innovation and material selection in various sectors.
Polyethylene
Polyethylene, one of the most widely produced plastics globally, is known for its lightweight and durable nature. It comes in several forms, including low-density polyethylene (LDPE) and high-density polyethylene (HDPE). LDPE is more flexible, making it suitable for items such as plastic bags and films. On the other hand, HDPE is tougher and finds its place in products like milk jugs and detergent bottles. Both types possess excellent resistance to chemicals, which is a boon in many industrial applications.
The environmental considerations are worth noting, as polyethylene degradation takes a significant amount of time. Yet, advancements in recycling processes can mitigate some of these concerns, making it a focal point in the discussion about sustainable practices in polymer use.
Polypropylene
Polypropylene is another standout thermoplastic, known for its high melting point and excellent fatigue resistance. It's often utilized in applications requiring durability, such as automotive components and household goods. Unlike polyethylene, which has a more linear structure, polypropylene’s structure allows it to be molded into a variety of shapes without losing its integrity. This versatility translates to a broad spectrum of uses, spanning from containers to textiles.
In addition, polypropylene can be produced with varying levels of transparency and can be recycled effectively. This adaptability not only enhances its appeal but also supports efforts toward a circular economy in material usage.
Polystyrene
Polystyrene, often encountered in its expanded form (commonly known as Styrofoam), is widely used in packaging and insulation. What sets polystyrene apart is its excellent thermal insulation properties combined with significant rigidity. However, there are drawbacks, including its environmental impact. As a material known for its buoyancy, it presents recycling challenges, making responsible disposal a hot topic among environmentalists.
Moreover, the flexibility of polystyrene opens doors for innovation, especially in the creation of disposable consumer products. It’s a material that keeps on giving, so to speak, with ongoing research focused on enhancing its sustainability.
Polyvinyl Chloride
Polyvinyl chloride (PVC) is noteworthy in the construction and medical sectors due to its impressive mechanical and chemical properties. Found in many pipes, flooring, and even medical devices, PVC’s adaptability in manufacturing strongly appeals to numerous industries. The polymer can be either flexible or rigid, allowing varied formulations to suit specific uses.
However, PVC's production and disposal raise concerns about harmful chemicals, urging a need for careful consideration regarding its lifecycle. This has led to some industries seeking alternatives or better methods for recycling PVC, thus keeping it relevant in discussions surrounding environmental sustainability.
Thermoplastic Elastomers
Thermoplastic elastomers (TPEs) combine the best of rubbery flexibility with the moldability of thermoplastics. TPEs are incredibly versatile, finding applications across many sectors, including automotive, medical devices, and consumer goods. Their unique characteristics allow them to provide both performance and comfort, which is particularly important in making items like soft-touch grips and seals.
The dual nature of TPEs allows for innovations that cater to various functionalities, ensuring they remain a key focus area in the evolving landscape of synthetic thermoplastics. Equally important is the ongoing research into improving their environmental footprint, ensuring that their benefits are not overshadowed by sustainability issues.
As the landscape of synthetic thermoplastics evolves, each type comes with its own set of advantages and challenges. The key is to balance functionality with sustainability to maximize the benefits these materials offer.
Mechanical Properties
Understanding the mechanical properties of synthetic thermoplastic polymers is crucial in grasping their performance under various conditions. This section highlights the different attributes that determine how these materials react when subjected to stress, heat, or impact. Mechanical properties, such as tensile strength, impact resistance, and thermal behavior, govern their suitability for a range of applications, from automotive components to consumer goods. Knowing these properties helps researchers and engineers select appropriate materials for specific uses and optimize their performance in real-world applications.
Tensile Strength and Modulus
Tensile strength and modulus are vital metrics showcasing how a polymer material behaves when stretched. Tensile strength refers to the maximum amount of tensile (pulling) stress a material can withstand before failing. Conversely, the tensile modulus, or elasticity, measures a material's stiffness, defining how much it will deform under stress.
The following points illustrate their significance:
- Load-bearing: High tensile strength means a polymer can bear significant loads without breaking, which is essential in construction and engineering applications.
- Durability: Materials with good tensile properties maintain their shape and structural integrity over time, making them reliable for long-term applications.
- Safety: Understanding tensile characteristics aids in designing components that must withstand high operational stresses, ensuring that they do not fail unexpectedly.
For example, polyethylene exhibits a high tensile strength, making it suitable for packaging materials that require durability. Knowing these properties allows manufacturers to innovate in creating more resilient products.
Impact Resistance
Impact resistance defines a polymer's ability to withstand sudden forces or shocks without cracking or breaking. In industries where products are subject to drops or hits, this property is of utmost importance.
Consider the following points:
- Energy Absorption: Materials with high impact resistance can absorb energy from impacts, lowering the risk of failure.
- Cost-Effectiveness: Choosing polymers with better impact resistance can reduce the need for protective casing and improve overall product longevity.
- Reputability: Products that withstand impacts are more likely to perform well, enhancing a company's reputation for quality.
Polystyrene, noted for its excellent impact resistance, is widely used in protective packaging. Understanding a polymer's impact properties ensures practical applications in packaging, toys, and automotive parts, where durability is critical.
Thermal Properties
Thermal properties encompass how materials respond to temperature changes, which is vital in many applications. Key thermal properties include heat resistance, thermal expansion, and thermal conductivity.
Here are critical considerations:
- Heat Resistance: Some polymers maintain their functional integrity at elevated temperatures, while others may soften or degrade. This property is critical in applications involving heat, such as automotive components.
- Thermal Expansion: Different materials expand or contract when exposed to temperature changes. Knowing this helps avoid mechanical failures in precision parts.
- Thermal Conductivity: Understanding how well a polymer conducts heat is essential, especially in electrical insulation applications.
For instance, polyvinyl chloride is noteworthy for its thermal stability under heat. This makes it valuable in plumbing and electrical applications, where exposure to high temperatures can occur. Assessing thermal properties is fundamental for ensuring safety, enhancing performance, and reducing failure rates in various industries.
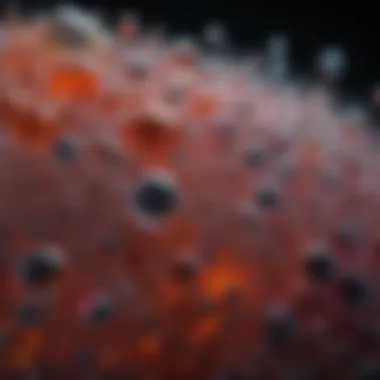
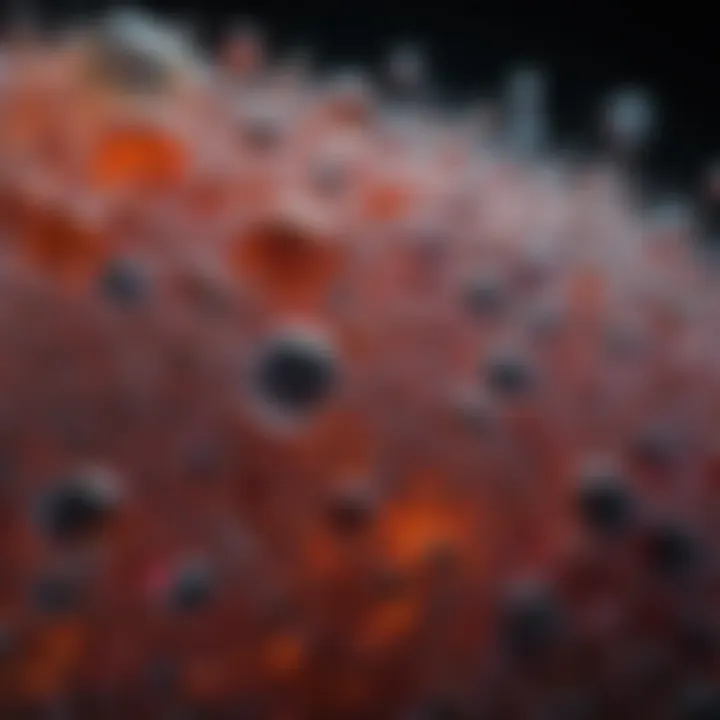
"The interplay of mechanical properties in synthetic thermoplastic polymers reveals not just material performance but also their significance in innovative applications across diverse sectors."
Processing Techniques
The methods used to process synthetic thermoplastic polymers are crucial in determining their final properties and performance. It’s more than just a step in manufacturing; it shapes how these materials will behave in their end-use environments. By masterfully manipulating these techniques, manufacturers can achieve desired characteristics, leading to innovative applications across different fields. Key techniques include injection molding, blow molding, and extrusion, each with unique advantages and specific considerations that can impact production efficiency, material properties, and overall sustainability.
Injection Molding
Injection molding is a highly versatile and widely adopted process for shaping synthetic thermoplastic polymers. In this method, melted plastic is injected under pressure into a mold. Once cooled, the mold is removed and reveals a finely detailed product.
Some important elements of injection molding include:
- Fast Production Speed: This method enables the mass production of parts which helps in meeting high demand efficiently.
- Complex Geometries: It allows for the creation of intricate designs that might be difficult to achieve through other means.
- Material Efficiency: The process generates minimal waste since excess material can be reclaimed and reused.
However, it’s paramount for manufacturers to consider mold design, as this can significantly affect lead times and costs. High-quality molds often involve larger upfront investments but pay off with durability and precision in production.
Blow Molding
Blow molding, another essential technique, is primarily used for hollow products such as bottles and containers. In this process, a thermoplastic polymer is heated until soft, formed into a parison, and then inflated within a mold. The expansion of the material helps to establish the desired shape and thickness.
Advantages of blow molding include:
- Cost-Effective for Large Scale Production: It’s ideal for producing large quantities of similar items without compromising quality.
- Lightweight Products: The process can result in thinner walls, thereby reducing the weight without sacrificing strength.
- Versatile Material Options: A variety of polymers can be utilized, making it adaptable for different products.
Yet, blow molding does present some challenges. For instance, manufacturing involves controlling temperatures and pressures carefully, and any deviation can lead to defects in the final product.
Extrusion
Extrusion is a continuous process in which polymer pellets are melted and forced through a die to create long shapes such as films, sheets, and tubes. This method is particularly noteworthy for its efficiency and versatility, allowing manufacturers to maintain high throughput with consistent quality.
Benefits of extrusion include:
- Continuous Production: Unlike batch processes, extrusion can run indefinitely, producing a steady stream of material, which can significantly lower costs.
- Customization of Product Dimensions: The die used in extrusion can be customized to create complex cross-sections, catering to specific customer needs.
- Less Waste Generation: Scrap material can be easily reintroduced into the process, promoting sustainability.
However, it is essential to monitor the cooling process carefully as uneven cooling can lead to warping or defects in the product, affecting performance.
"Each technique has unique advantages and drawbacks, and the choice of method often dictates the material's final characteristics and suitability for specific applications."
In summary, understanding these processing techniques is vital for anyone working with synthetic thermoplastic polymers. It not only informs the manufacturing decisions but also plays a pivotal role in harnessing the full potential of these materials.
Applications of Synthetic Thermoplastic Polymers
The significance of synthetic thermoplastic polymers in today’s world cannot be overstated. These materials are basically the bread and butter of modern industries, serving a multitude of applications across various domains. One of the essential elements of synthetic thermoplastic polymers is their versatility, which allows them to be engineered to meet a wide range of needs. From consumer products to high-tech medical devices, the utilization of these materials reflects a blend of functionality, sustainability, and economic viability. As we explore the various avenues where these polymers are pivotal, we delve into the specific benefits and considerations surrounding their applications.
Consumer Goods
Synthetic thermoplastic polymers find their way into everyday consumer goods more than one might realize. Items ranging from kitchen utensils to toys often rely on these materials for their durability and ease of production. For instance, polyethlene, a type of thermoplastic polymer, is widely used in making containers for food storage due to its safe, versatile nature.
Some characteristics of synthetic thermoplastics in consumer goods include:
- Durability: These materials can endure various stresses, making them ideal for long-lasting products.
- Cost-Effectiveness: The production processes are generally less expensive than traditional materials.
- Design Flexibility: They can be molded into various shapes, allowing for creative product designs.
However, one must also consider the environmental aspects tied to consumer goods made of synthetic thermoplastics. With increased scrutiny on plastic waste, manufacturers face pressure to adopt recycling practices and innovate more sustainable alternatives.
Automotive Industry
The automotive industry is another major sector that relies heavily on synthetic thermoplastic polymers. Cars today are designed with a focus on reducing weight while maintaining strength, and that's where these polymers shine. For instance, polypropylene is used in interiors and bumpers because it offers a balance of low weight and high impact resistance. Essential applications include:
- Dashboards and Door Panels: These components are often produced from materials like polyvinyl chloride and ABS, reducing vehicle weight and improving fuel efficiency.
- Fuel Tanks: High-density polyethylene is used to manufacture robust, lightweight fuel tanks that can resist shrinkage and cracking over time.
Naturally, the trend towards electric vehicles is also shaping the future of synthetic polymer applications, adapting to changing dynamics in materials and design.
Medical Applications
In the realm of health care, synthetic thermoplastic polymers play a crucial role. They are pivotal in manufacturing medical devices that require precision and reliability while being biocompatible. For example, polycarbonate is commonly used for making surgical instruments and components in drug delivery systems due to its clarity and strength.
Key applications in the medical sphere include:
- Syringes and IV Bags: Many of these items are crafted from clear polypropylene or polyethylene, ensuring no chemical interactions with the contents.
- Prosthetics: Thermoplastic elastomers can be molded into comfortable and functional prosthetic devices, allowing for improved patient mobility.
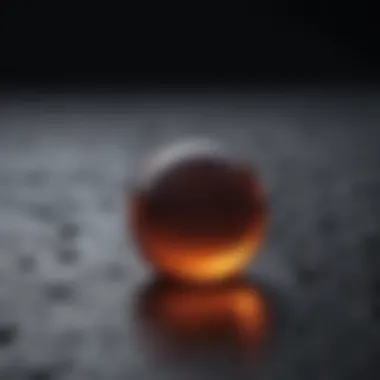
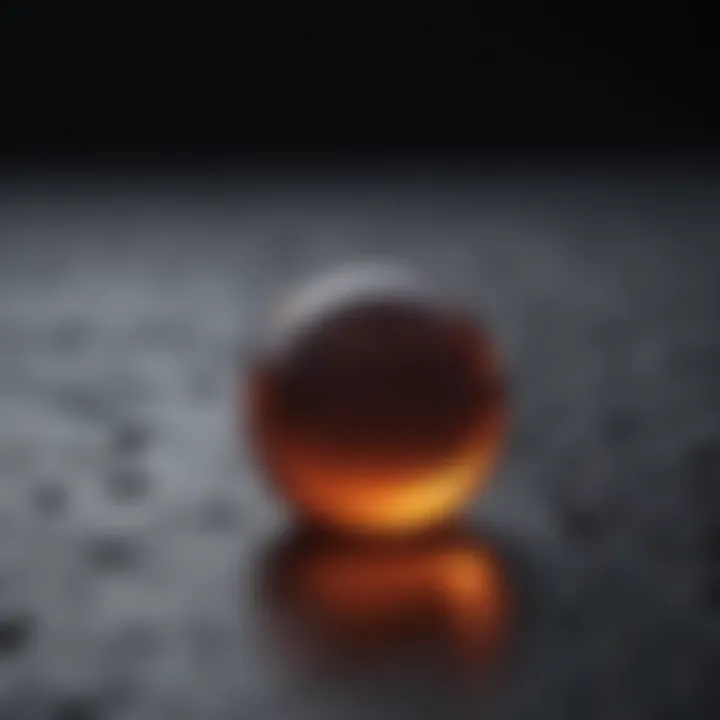
The rapid innovation in this field points towards a future where synthetic thermoplastic polymers become even more integral in life-saving technologies.
Packaging Solutions
Packaging is another vital area where synthetic thermoplastic polymers dominate. They offer benefits like moisture resistance, strength, and lightweight properties, essential for keeping products safe during transport and extending their shelf life. Common applications include:
- Bottles and Containers: Polyethylene terephthalate (PET) is a staple in beverage packaging, offering both strength and recyclability.
- Flexible Packaging: Polyester films made from thermoplastics are used extensively in the food industry, enhancing the freshness of perishable goods.
Despite their advantages, the packaging sector is under continuous challenge to improve recyclability and reduce reliance on single-use plastics, further pushing the need for innovation in synthetic thermoplastic design.
"Understanding the breadth of applications of synthetic thermoplastic polymers helps us appreciate their role in modern life, while also prompting a dialogue on sustainability and future innovation."
Innovations and Trends
The landscape of synthetic thermoplastic polymers is rapidly evolving. Innovations in formulation and processing techniques are key drivers that enhance their performance and broaden their applications. These advances are crucial not just for businesses aiming to boost efficiency but also for addressing pressing global challenges like waste management and sustainability. Understanding these trends helps stakeholders navigate the complexities involved in polymer utilization, ensuring they remain competitive and responsible.
Biodegradable Alternatives
Recent shifts in consumer attitudes towards plastic products emphasize sustainability. This brings biodegradable polymers to the forefront as a viable alternative. These materials can break down into natural substances in specific environmental conditions, aiming to reduce the accumulation of plastic waste.
One notable example is polylactic acid (PLA), derived from renewable resources like cornstarch. PLA serves as a versatile candidate for various applications, including food packaging and disposable cutlery. Its importance lies in its potential to mitigate environmental impact, offering an alternative that can support the circular economy.
Nonetheless, deployment of biodegradable polymers is not devoid of challenges. One critical consideration is the specific conditions required for biodegradation. It may often necessitate industrial composting, which limits the material's effectiveness in typical landfill environments. Adapting these materials for maximum efficiency and addressing public perceptions about their efficacy remain vital.
"Biodegradable polymers may be the key to harmonizing our industry with environmental stewardship, but without proper waste management systems in place, they may not fulfill their promise."
Smart Polymers
On a different note, smart polymers introduce an exciting frontier in materials science. These polymers have the unique ability to respond to external stimuli such as temperature, pH, or light. Their responsiveness can significantly enhance product functionality across a range of sectors, from healthcare to electronics.
For instance, thermoresponsive polymers can alter their state with temperature changes, which is particularly advantageous in drug delivery systems. In this context, the polymer encapsulates medication and releases it when heated to a specific point in the body. This technology can lead to more efficient treatments with fewer side effects.
Moreover, smart polymers can be employed in the textile industry, enabling clothing that changes color in response to environmental triggers, making them not just functional but also innovative. Companies in this sector have begun to explore these unique properties, potentially setting the stage for a wave of new consumer-focused products.
Yet, the development of smart polymers requires careful consideration of the underlying technologies. Issues such as production costs, scalability, and regulatory circumstances need thorough examination, ensuring these innovations don’t become just a flash in the pan but a lasting solution in the polymer landscape.
Environmental Considerations
Environmental considerations concerning synthetic thermoplastic polymers are crucial in contemporary discussions surrounding the material sciences. As industries and consumers become more aware of their ecological footprint, the spotlight shines on these polymers, driving the need to assess their life cycles and recycling potentials intimately. Addressing environmental concerns isn't just about compliance; it’s becoming an ethical obligation within the framework of sustainability.
Lifecycle Analysis
Lifecycle analysis (LCA) serves as a fundamental tool for understanding the environmental implications of synthetic thermoplastic polymers throughout their existence – from extraction to disposal. LCA encompasses several stages:
- Raw Material Extraction: The environmental impact begins with the extraction of raw materials necessary for these polymers, such as petroleum or natural gas. This stage often involves significant environmental disturbances, like habitat destruction and resource depletion.
- Manufacturing Processes: During production, energy consumption and emissions from factories are crucial factors to consider. Manufacturing synthetic thermoplastics often involves complex processes that can release greenhouse gases and toxic byproducts.
- Usage Phase: Once in the market, these polymers tend to serve various functions, from packaging to automotive components, which generally have low environmental impact during their usage. However, their durability and resistance to degradation pose a substantial concern post-use.
- Disposal and End-of-Life Options: One of the significant challenges in LCA is the disposal of synthetic thermoplastics. Landfilling can lead to long-term environmental issues, whereas incineration, while reducing mass, generates emissions that can affect air quality.
A comprehensive LCA not only highlights critical areas for improvement in sustainability but also assists in guiding future materials research and development towards greener alternatives.
Recycling Challenges
Recycling synthetic thermoplastic polymers is a complicated and multifaceted issue that poses significant challenges. Some of the most pressing difficulties include:
- Contamination: One of the major hurdles in recycling is the contamination of materials. Often, products made from different types of thermoplastics are mixed together, making it hard to separate and recycle them efficiently. This contamination can significantly diminish the quality and value of recycled materials.
- Material Properties: Different synthetic thermoplastics have diverse melting points and structural characteristics. This variability creates difficulties in standardizing recycling processes, especially when the industry lacks properly designed sorting technologies.
- Market Demand: There's often limited market demand for recycled materials. Manufacturers may hesitate to utilize recycled inputs due to potential quality concerns, relying more on virgin materials, thus perpetuating a cycle of resource consumption.
- Economic Factors: The costs associated with sorting, cleaning, and processing recycled thermoplastics can be prohibitively high. These can deter recycling initiatives, as the economic feasibility becomes questionable without sufficient incentives.
To combat these challenges, policymakers, industry leaders, and researchers must collaborate to innovate effective recycling technologies and foster market demand for recycled materials. Making strides in this area is vital—not just for enhancing the longevity of the materials but also for promoting a circular economy in which waste is minimized, and resources are reused.
Future Perspectives
The discussion surrounding synthetic thermoplastic polymers is growing increasingly critical as industries evolve in response to environmental and technological challenges. These materials have already carved out a niche across various sectors, from automotive to medical applications, but as we peer into the future, it's clear that numerous avenues await exploration. Understanding these future perspectives isn’t just academic; it empowers businesses and researchers to make informed decisions that resonate with sustainability, efficiency, and innovation.
Here are some key elements to consider regarding the future of synthetic thermoplastic polymers:
- Sustainability: As consumers become more environmentally conscious, there's heightened pressure on manufacturers to reduce their carbon footprint. Synthetic thermoplastics are under scrutiny, and advancements in biodegradable alternatives may take center stage. This shift not only addresses ecological concerns but can also enhance brand loyalty among new generations of consumers.
- Technological Advancements: Emerging technologies such as 3D printing and smart materials are set to transform how synthetic thermoplastics are utilized. These innovations could lead to entirely new applications that we cannot yet imagine.
- Interdisciplinary Collaborations: The future will likely see more collaborations between chemists, engineers, and environmental scientists. Such partnerships can harness diverse expertise, leading to novel approaches in polymer design and application.
End
The discussion surrounding synthetic thermoplastic polymers is not just an academic exercise; it serves as a foundation for understanding a critical component of modern material science. The insights gained from this exploration highlight the significant role these materials play across various sectors of industry and daily life.
Summary of Key Points
- Definition and Scope: Synthetic thermoplastic polymers are versatile materials characterized by their ability to soften upon heating and harden on cooling. This property is the cornerstone of their wide applicability.
- Diverse Applications: We have examined applications in consumer goods, the automotive industry, and medical fields, showcasing how they impact our daily lives and industrial practices.
- Innovations and Promises: Further, innovations such as biodegradable alternatives and smart polymers open new pathways for sustainable development, addressing the growing concerns regarding environmental impact.
- Mechanical and Processing Insights: Understanding the mechanical properties, processing techniques, and the nuances of polymerization helps inform better design and application strategies.
- Environmental Considerations: The lifecycle analysis of these materials underscores the importance of recycling and sustainability in polymer technology, presenting challenges that require innovative solutions.
Final Thoughts on Synthetic Thermoplastic Polymers
Synthetic thermoplastic polymers represent a crucial intersection of technology, industry, and daily life. Their ability to adapt and provide solutions to specific needs makes them indispensable in today's manufacturing landscape. However, as the environmental challenges loom large, the continued research in materials science focused on creating sustainable and eco-friendly alternatives is paramount. The future of synthetic thermoplastic polymers will largely be shaped by our ability to innovate while remaining conscious of our environmental footprint. This balance is not only crucial for industry leaders and researchers but also for consumers who increasingly demand sustainable practices.
In closing, as we further our understanding of these materials, we must foster a sense of responsibility towards their life cycle and the impacts they impart on our world.