Understanding Inkjet Nozzles: Mechanisms and Design
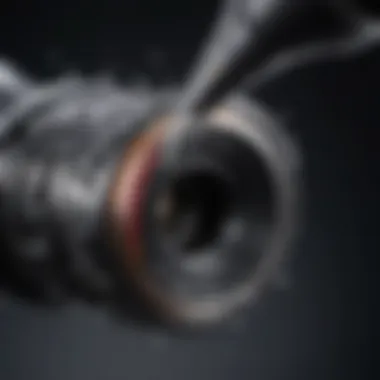
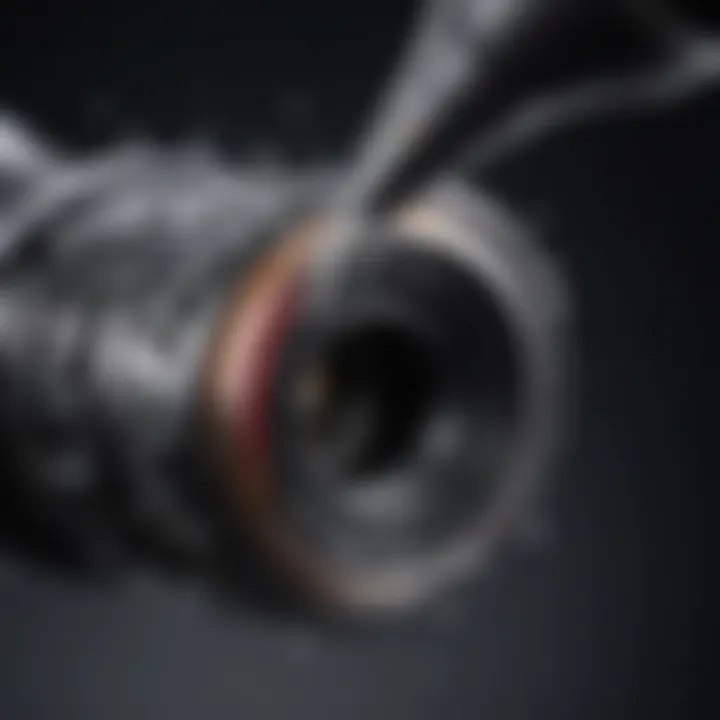
Intro
The study of inkjet nozzles represents a critical area in printing technology. As these components function at the heart of inkjet printers, understanding their mechanisms, design variations, and practical applications across different industries is essential. This exploration not only aids in grasping the operational aspects of these devices but also reveals their influence on print quality and efficiency. Through careful analysis, one can appreciate the nuances in nozzle technology that contribute to advancements in diverse fields including art, manufacturing, and healthcare.
Research Overview
Key Findings
The examination of inkjet nozzle design and functionality has led to several significant findings that shape current practices in the industry. Notably, advancements in microfabrication techniques have enabled the creation of smaller and more efficient nozzles. This innovation enhances the precision of ink delivery, resulting in better print quality.
Additionally, materials selected for nozzle production have been shown to impact not only the durability but also the performance of the nozzles. For instance, the implementation of durable polymers and specific alloys has been explored to prevent clogging and ensure consistent ink flow. Moreover, the introduction of piezoelectric and thermal inkjet technologies exhibits varied effects on operation and maintenance.
Study Methodology
The research methodology employed in this analysis includes a comprehensive review of existing literature, paired with practical case studies focusing on nozzle performance metrics in real-world applications. Various parameters such as droplet size, ink viscosity, and temperature settings were examined to evaluate their effects on print resolution and consistency. This dual approach allowed for a well-rounded perspective on the challenges and innovations present within the industry.
Background and Context
Historical Background
The concept of inkjet printing can be traced back to the 1950s, but significant technological advancements have only emerged in the past few decades. Early inkjet systems were rudimentary and often prone to malfunction due to the lack of stable nozzle designs. Over time, research and development in fluid dynamics and material science have greatly improved nozzle technology, transitioning from basic designs to more complex systems capable of delivering high-quality prints over varied substrates.
Current Trends in the Field
Currently, there is a notable trend towards integration of smart technology in inkjet nozzles. This includes sensors that monitor performance in real-time, adjustments in ink viscosity to prevent clogging, and systems designed for quick maintenance. Moreover, sustainability considerations have prompted the rise of eco-friendly inks and recyclable materials for nozzle construction. As these trends continue to evolve, they pave the way for exciting innovations in the world of inkjet printing.
Prologue to Inkjet Technology
Inkjet printing is a pivotal technology that has revolutionized the way visuals and text are produced across diverse fields. The importance of understanding inkjet technology lies not only in its foundational principles but also in its practical applications in everyday life. Students, researchers, educators, and professionals alike can benefit from a detailed exploration of this technology. Inkjet printers have become increasingly commonplace due to their efficiency, versatility, and ability to deliver high-quality output. This article examines the intricate components of inkjet nozzles, which are essential for the functionality of these printers.
The benefits of understanding inkjet technology include improved application in various industries such as publishing, textiles, and packaging. Knowledge about how inkjet nozzles operate can aid in addressing challenges related to printquality and material usage. Furthermore, recognizing the various design considerations allows for a better grasp of how innovations might evolve to meet growing demands in precision and speed.
In this article, we will dive into the historical context and delve into how nozzles play a critical role in inkjet printing, laying the groundwork for further discussions on nozzle mechanisms, design considerations, and their applicable fields.
Historical Context of Inkjet Printing
The journey of inkjet printing began in the late 20th century, emerging from a need for more efficient printing methods. The early innovations during the 1950s and 1960s led to the development of the first inkjet printers, but it was not until the 1980s that commercial viability kicked in. Companies began to realize the potential for high-volume printing coupled with lower costs. Inkjet technology opened doors to desktop printing solutions, significantly impacting businesses and individual users alike. The printer's ability to produce images without physical contact with the media was a groundbreaking feature that contributed to its rapid adoption.
Over the decades, advancements in nozzle technology have concurrently evolved, refining the quality and speed of inkjet printers. As the market expanded, so did the diversity of application, paving the way for specialized printers for industrial uses. This evolution has now culminated in an era where inkjet printing is not just limited to paper but extends to textiles, ceramics, and even electronics, showcasing the versatility of inkjet technology.
The Role of Nozzles in Inkjet Printing
Nozzles are often considered the heart of inkjet printers; they play a paramount role in determining the print quality and efficiency. Their primary function is to create and eject ink droplets with precision, which is crucial for forming high-resolution images and text. There are two dominant types of inkjet nozzles: thermal and piezoelectric, each employing different mechanisms for ejection.
Inkjet nozzles determine several key performance metrics, including:
- Droplet Size: The size affects how effectively ink adheres to various mediums.
- Ejection Frequency: Higher frequencies allow for faster printing speeds.
- Ink Volume Control: This enables variations in density and can impact overall image quality.
The relationship between nozzle design and printing results is intricate. Adjustments in nozzle size, shape, and arrangement can lead to significant differences in performance. Understanding these dynamics is likely to lead to better, more efficient designs in the future.
Fundamentals of Inkjet Nozzles
Inkjet nozzles serve as the heart of inkjet technology. Understanding their fundamentals is essential to discerning how inkjet printers achieve high-quality output across various applications. The performance of an inkjet printer is heavily reliant on the nozzle's design and functionality.
Key elements such as droplet size, ejection speed, and material composition directly impact the print quality and efficiency. Furthermore, the type of nozzle utilized can determine capabilities in different environments, affecting industries from commercial printing to textiles.
Definition and Functionality
Inkjet nozzles are precision-engineered components that generate droplets of ink with extreme accuracy. Each nozzle delivers small, controlled droplets onto a substrate, enabling the creation of detailed images and text. Their primary function is to translate digital signals into physical ink patterns.
Every nozzle operates through specific mechanisms, either heating the ink to create vapor bubbles or utilizing piezoelectric forces to push ink through an orifice. These methods dictate the rate of ink ejection, droplet size, and shape of sprays it can generate. This control is paramount for applications in all areas, from artistic printing to functional tests in industrial applications.
Types of Inkjet Nozzles
Two primary types of inkjet nozzles dominate the market: thermal inkjet nozzles and piezoelectric inkjet nozzles.
Thermal Inkjet Nozzles
Thermal inkjet nozzles operate through a heating element that vaporizes ink to form bubbles. These bubbles rapidly expand, forcing a droplet to eject through the nozzle. A significant characteristic of thermal inkjet technology is its straightforward design, which promotes easier manufacturing and lower production costs.
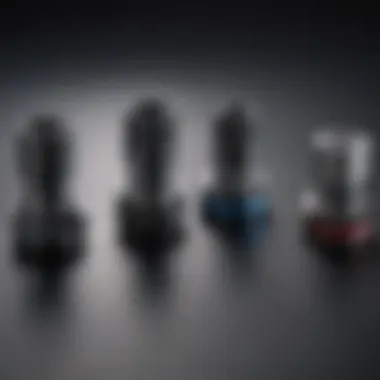
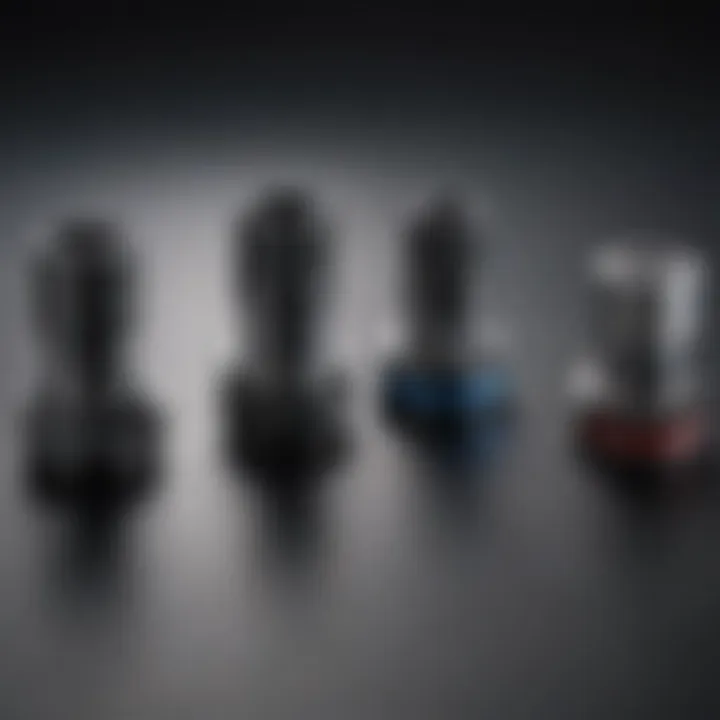
The main advantages of thermal inkjet nozzles include:
- Cost-effectiveness: They generally have lower manufacturing costs.
- Wide Availability: Products from established brands use this type extensively, making them widely accessible.
However, there are notable disadvantages as well, such as:
- Limited Ink Types: Not all ink types can be used due to the heat-sensitive nature.
- Potential for Clogging: Residue from certain inks can lead to blockages, demanding more maintenance.
Piezoelectric Inkjet Nozzles
Piezoelectric inkjet nozzles utilize a piezoelectric crystal within the nozzle to create pressure that forces ink out when an electric field is applied. Their unique feature is the ability to control droplet volume and size precisely. This precision makes them suitable for a broader range of applications compared to thermal counterparts.
Key characteristics include:
- Versatile Ink Selection: They can handle a variety of ink types, including those that are thicker or sensitive to heat.
- Less Clogging: They tend to be more reliable over time.
Yet, there are some downsides:
- Higher Costs: The manufacturing process is more complex and can lead to increased costs for printers using this technology.
- Power Consumption: They may consume more energy compared to thermal versions.
Both types of nozzles play vital roles in inkjet technology, each bringing unique advantages and challenges to the table. Understanding these fundamentals is necessary for choosing suitable inkjet solutions tailored to specific printing needs.
Design Considerations for Inkjet Nozzles
The design of inkjet nozzles encompasses critical elements that directly affect print quality and efficiency. Proper consideration of these factors is essential for optimizing performance. Design aspects such as geometric parameters and material selection significantly influence how well a nozzle operates within the inkjet system.
A well-designed nozzle ensures precise droplet formation and ejection. This not only enhances image fidelity but also reduces the risk of common issues like clogging. Furthermore, advances in materials can lead to more durable nozzles capable of withstanding various printing substances and conditions. Thus, understanding the design considerations is paramount for those involved in the field of inkjet technology.
Geometric Parameters
Orifice Size
Orifice size is one of the most crucial aspects of nozzle design. A smaller orifice may deliver smaller droplets, which can enhance detail but may also require higher pressures. Conversely, larger orifice sizes can produce bigger droplets, meeting applications that prioritize speed over fine detail.
The key characteristic of orifice size is its direct impact on droplet formation. Smaller orifices can result in a more varied droplet size, which can be beneficial for applications needing gradients or complex fills. However, smaller orifices are more prone to clogging, presenting a risk that needs careful management. Therefore, balancing between droplet size and potential clogging risks is a critical consideration.
Unique features of orifice size involve its relationship to the viscosity of ink. Higher viscosity inks generally require larger orifices to ensure proper ink flow. As a result, nozzle rheology becomes a significant factor in determining the optimal size for a particular application.
Channel Length
Channel length also plays a significant role in the performance of inkjet nozzles. Shorter channels generally allow for faster ink delivery from the cartridge to the nozzle. This is beneficial for rapid printing processes where speed is essential.
The key characteristic of channel length is its influence on flow dynamics. Longer channels can lead to increased resistance which may cause issues such as reduced pressure and even inconsistent droplet formation. Therefore, a short channel design is typically favored in modern applications.
However, lengthened channels can have their advantages too. They might facilitate better ink mixing, essential for certain printing processes that require color precision. Thus, the choice between short and long channels often depends on the specific requirements of the print task.
Material Selection
Impact of Materials on Performance
The choice of materials in nozzle construction profoundly influences performance. Materials must withstand the operational demands of the printing process, including heat, pressure, and interaction with the ink. The wrong material selection can lead to early failure, reduced print quality, and costly downtimes.
A key characteristic of material selection is its effect on viscosity handling. Materials that can accommodate a broader range of ink viscosities afford greater versatility, allowing users to switch inks without modifying the nozzle. This adaptability is especially crucial in commercial applications where different ink types often come into play.
Unique features of material selection may involve trade-offs. For instance, while certain materials offer superior resistance to wear and tear, they can also increase production costs. Therefore, assessing the total cost of ownership versus performance benefits is the prime challenge in material selection for inkjet nozzles.
Corrosion Resistance
Corrosion resistance in nozzle materials is fundamental to ensuring longevity and reliability. Inkjet nozzles frequently handle various ink formulations, including those containing corrosive components. Thus, materials used must display an adequate resistance to such elements, preventing degradation over time.
A key characteristic of corrosion-resistant materials is their ability to maintain structural integrity and performance even in harsh environments. Using coated metals or specially engineered plastics can significantly extend the usable life of nozzles.
The unique feature of corrosion-resistant materials is their impact on maintenance costs. By implementing materials that resist corrosion, manufacturers can reduce maintenance requirements and improve operational efficiency, providing a long-term financial edge.
Operating Mechanisms of Inkjet Nozzles
Understanding the operating mechanisms of inkjet nozzles is crucial for recognizing how these components influence the overall functionality of inkjet printing systems. The nozzle directly affects print quality, speed, and efficiency. A thorough grasp of how ink is ejected and how fluid dynamics play a role can inform better design practices and material selection, ultimately leading to innovations in printing technology.
Ink Ejection Processes
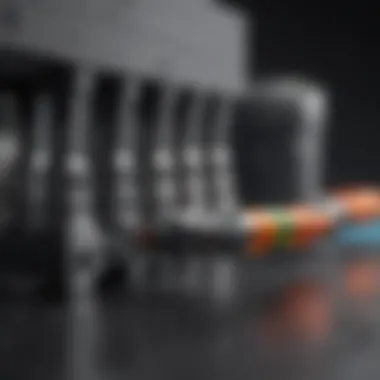
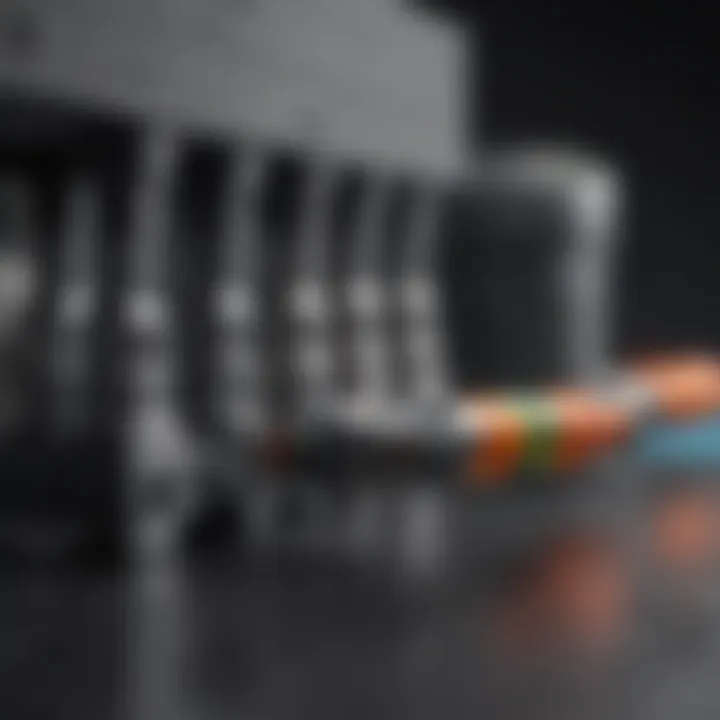
The ink ejection process is a fundamental mechanism in inkjet technology. This ejection can occur through various methods, primarily classified into two major categories: phase change mechanisms and mechanical deformation mechanisms. Each method has unique properties that determine its operational characteristics and suitability for different applications.
Phase Change Mechanisms
Phase change mechanisms rely on the transformation of ink from one physical state to another, which is key in driving the ejection process. Typically, this involves heating the ink to create vapor bubbles, which expand and force a droplet to exit the nozzle. The primary characteristic of phase change mechanisms is their ability to create a precise droplet size, making them popular for high-quality print demands.
One unique aspect of these mechanisms is their utilization of thermal energy. When the ink is heated, it results in rapid bubble formation. This fast response time is beneficial because it enables quicker printing speeds without sacrificing quality. However, phase change methods may have drawbacks, such as potential overheating leading to issues like nozzle clogging.
Mechanical Deformation Mechanisms
Mechanical deformation mechanisms operate differently by using physical movement to expel ink. This approach often involves the use of piezoelectric materials. The key feature of mechanical deformation is its adaptability; it can control droplet formation without relying on temperature changes. This results in consistent droplet ejection, which is important for maintaining color accuracy and quality in prints.
One significant advantage of mechanical deformation mechanisms is their compatibility with a wider range of ink formulations, including those that are more viscous. However, they may have limitations in terms of speed compared to phase change systems. The intricacies in how these systems operate can significantly impact the design of nozzles and their efficiency in various applications.
Flow Dynamics in Inkjet Nozzles
Flow dynamics within inkjet nozzles is another pivotal area that influence performance. When the ink travels through the nozzle, it must overcome different resistances, which can affect droplet formation and jet stability. It is essential to understand the interplay between pressure, velocity, and viscosity of the ink.
The study of these dynamics helps to optimize nozzle design for reducing back pressure and maximizing flow rates. Effective flow management can lead to improved print head performance, lower maintenance needs, and enhanced overall print quality, making it a significant element of nozzle technology development.
Performance Metrics for Inkjet Nozzles
Performance metrics for inkjet nozzles are essential to understanding their effectiveness and reliability in various applications. These metrics serve as benchmarks, guiding manufacturers and users in evaluating nozzle performance related to print quality and durability. In a world where precision and quality are critical, careful consideration of these performance metrics can lead to significant advantages in product excellence and customer satisfaction. The core metrics commonly examined include print quality indicators and measures of reliability and longevity.
Print Quality Indicators
Print quality indicators are quantifiable measures that impact how the final print product is perceived. They are vital for application in commercial and industrial settings, where quality directly correlates with market competitiveness.
Droplet Size Consistency
Droplet size consistency is a crucial aspect that influences the uniformity of printed images. High consistency can lead to better color saturation and overall print clarity. A notable characteristic of droplet size consistency is its role in avoiding unwanted artifacts such as banding or color degradation.
This aspect becomes especially valuable in line production environments where precision is paramount. When droplet sizes vary too significantly, it can result in noticeable differences in tonal qualities and sharpness. The unique feature of maintaining a steady droplet size is its direct advantage in enhancing print quality and providing a smoother gradient.
However, the challenge lies in the complexity of achieving and retaining this consistency, especially over extended printing sessions. A careful calibration and maintenance protocol must be adhered to, or quality may suffer.
Color Accuracy
Color accuracy refers to the ability of the inkjet nozzle to reproduce colors that are true to the original image. This metric influences customer satisfaction as it dictates how closely the final printed output aligns with the desired visual specification. Key characteristics include a broad color gamut and consistency across different media types.
This measurement is extensively beneficial in sectors like graphic arts and textile printing, where accurate color representation can define the value of the output. The uniqueness of color accuracy lies in its need for finely tuned color profiles and sensor technologies, which can add to the complexity of design. Additional advantages include higher customer loyalty and lower return rates due to misprints.
Despite these advantages, achieving color accuracy can be challenging due to variations in display tech and media properties. Continuous calibration is needed to ensure that the consistency is maintained in varying production environments.
Reliability and Longevity
Reliability and longevity of inkjet nozzles are factors that greatly affect overall printing operations. These metrics are instrumental in assessing how well a nozzle can withstand wear over time and under different usage conditions. It is essential to ensure that customers receive high-quality outputs consistently without frequent disruptions.
A reliable nozzle contributes to fewer maintenance interventions and reduced downtime, which ultimately translates to cost savings. Furthermore, a long-lasting design decreases the frequency of component replacement, further enhancing operational efficiency and sustainability.
In summary, performance metrics provide substantial insights into inkjet nozzle operation. By addressing print quality indicators, such as droplet size consistency and color accuracy, as well as evaluating reliability and longevity, stakeholders can make informed decisions.
Performance metrics serve not only as benchmarks for quality but also as a pathway to operational efficiency and excellence in inkjet printing technology.
Applications of Inkjet Nozzles
The applications of inkjet nozzles are vast and significantly enhance various processes across multiple industries. Their ability to accurately and efficiently dispense ink allows for high-quality output in both commercial and industrial contexts. The versatility of inkjet nozzles in different settings highlights their technological importance. As businesses seek innovative solutions for printing needs, understanding these applications becomes critical.
Commercial Printing
In commercial printing, inkjet nozzles play a central role in producing high-quality printed materials. They are vital for applications such as flyers, brochures, and posters, where color precision and detail are paramount. The technology behind inkjet printing allows for vibrant colors that can gradually blend, creating aesthetically pleasing results.
Moreover, inkjet printers are increasingly favored for short runs. This flexibility minimizes waste, allowing businesses to adjust quickly to market demands. Customization is another hallmark of commercial printing with inkjet nozzles. Companies can produce tailored prints more easily, satisfying diverse consumer preferences. However, achieving a consistent print quality remains a challenge, and continual improvements in nozzle design are essential for overcoming these hurdles.
Industrial Applications
Textile Printing
Textile printing represents a specialized segment of industrial applications utilizing inkjet nozzle technology. This method allows for precise and elaborate designs to be printed directly onto fabrics. One key characteristic of textile printing is its ability to produce vibrant, detailed images quickly and cost-effectively. The use of digital inkjet techniques in textile printing leads to improved production efficiency. It reduces the time from design to finished product.
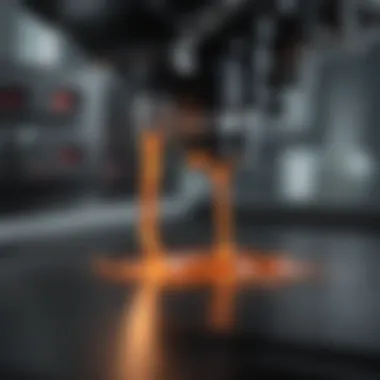
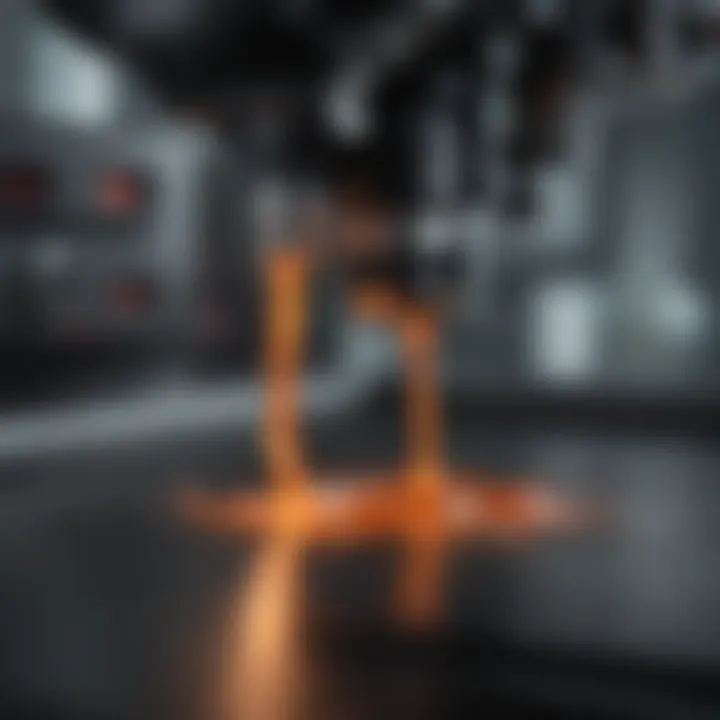
Furthermore, this technique allows for smaller batch sizes, which meets the increasing demand for personalized textile products. Benefits include reduced inventory costs and lower waste levels when compared to traditional methods. However, fabric compatibility and ink selection require careful consideration to ensure long-lasting results and avoid issues like fading.
Packaging Industry
The packaging industry has embraced inkjet nozzles for their ability to deliver high-resolution graphics and important information on packages. This application is crucial for branding and consumer information. One significant characteristic of the packaging industry is the need for versatility. Packaging varies widely, requiring different materials and sizes. Inkjet nozzles offer solutions ranging from labels to large shipping cartons.
A unique feature of packaging with inkjet technology is the capacity for variable data printing, which allows companies to customize labels and packaging on-the-fly. This ability enhances marketing strategies, as it enables targeted campaigns. While the benefits are numerous, challenges like ink adhesion on various surfaces and maintaining ink durability in different environments must also be addressed to maximize effectiveness.
Inkjet nozzles are revolutionizing how industries approach production, leading to innovative, cost-effective, and personalized solutions across diverse applications.
Challenges in Inkjet Nozzle Design
Inkjet nozzle design is central to the efficacy of inkjet printing technology. Various challenges arise during the design phase, impacting overall performance and usability. Addressing these challenges is crucial for maintaining high-quality output and industrial efficiency. Two primary issues in this context are clogging and maintenance, along with cost considerations.
Clogging and Maintenance
A significant challenge that designers face is the tendency of nozzles to clog. Clogging occurs when ink particles, dust, or air bubbles accumulate within the nozzle. This problem can lead to inconsistent print quality and may stop the printing process altogether. Regular maintenance can mitigate some clogging issues, but it is not always sufficient. Therefore, engineers often look for design modifications that reduce the likelihood of clogs.
Strategies to minimize clogging include:
- Optimizing orifice size to balance flow and pressure.
- Selecting inks with properties that prevent sedimentation.
- Designing self-cleaning mechanisms within nozzles.
The maintenance of inkjet nozzles is also critical. Users must be aware of proper cleaning protocols to keep the nozzles functioning optimally. This includes periodic cleaning cycles using specific cleaning solutions that safely dissolve ink residues. Manufacturers sometimes provide automated solutions for maintenance, which can be more efficient but also add to the overall cost of the printer.
"Maintaining the nozzle's functionality is as crucial as its initial design. The collaboration between design engineers and maintenance teams is pivotal," says an industry expert regarding the importance of maintenance in nozzle design.
Cost Considerations
Cost is another pressing challenge in the design of inkjet nozzles. High-performance nozzles made from advanced materials often come with a higher price tag. This raises the question of balancing performance with affordability. For instance, using high-quality materials can enhance durability but may not be justifiable for every application.
Key factors influencing costs include:
- Material Choice: Selecting metals or plastics impacts both performance and cost.
- Research and Development: Innovative designs require investment, which can affect the final consumer price.
- Production Scale: Larger batches often lead to reduced costs per unit, but market demand can influence production decisions.
Ultimately, manufacturers face a conundrum: invest in advanced materials and mechanisms to improve performance or limit costs to compete in a saturated market. Understanding these dynamics is essential for researchers and practitioners involved in nozzle technology, guiding them towards more successful designs.
Future Trends in Inkjet Nozzle Technology
The field of inkjet nozzle technology is rapidly evolving. Future trends focus on enhancing performance, efficiency, and reliability of inkjet systems. Innovations in materials and integration of smart technologies are two major areas of development. Understanding these trends is essential for researchers and professionals who want to stay updated in this competitive landscape.
Advancements in Materials
Materials play a crucial role in the effectiveness of inkjet nozzles. Future advancements will likely focus on developing specialized materials that can withstand higher pressures and a wider range of ink viscosities.
- Thermal Stability: Nozzles that can function effectively over a wider thermal range can improve reliability. This is especially important in high-volume printing scenarios.
- Wear Resistance: New coatings can enhance the longevity of nozzles. Materials such as ceramics and advanced polymers are gaining interest for their ability to resist wear and corrosion from aggressive inks.
- Bio-Compatibility: There is increasing demand in biomedical applications for inkjet printing. Developing materials that are bio-compatible can open new market opportunities, especially in producing medical devices.
Integration with Smart Technologies
The integration of smart technologies into inkjet printing systems offers significant opportunities for innovation. Sensors and connectivity options can transform traditional printing into intelligent printing solutions.
- Real-Time Monitoring: Sensors can provide data on nozzle performance, ink levels, and clogging issues. This data helps in predictive maintenance, reducing downtime.
- Adaptive Control Systems: Future inkjet nozzles may incorporate algorithms that adjust the ejection parameters based on the specific characteristics of the ink. This could lead to improved print quality and reduced waste.
- Internet of Things (IoT): The connection of inkjet systems to the IoT can facilitate automated ordering of supplies, user notifications for maintenance, and access to remote troubleshooting services. This could greatly enhance operational efficiency.
"Integration of smart technologies is not just a trend; it is the future of efficient printing systems."
By focusing on these two areas—advancements in materials and smart technology integration—the inkjet printing industry can expect to enhance the performance and efficiency of their products significantly. This evolution will contribute to better quality prints and a reduce in operational costs over time.
Culmination
The implications of improved nozzle technology extend beyond simple print quality; they resonate through an entire industry. Key benefits include reduced production costs, higher operational efficiency, and a more sustainable approach to printing. Enhanced nozzle designs can lead to innovations in various sectors, such as commercial printing and industrial applications like packaging and textiles.
Moreover, as we move towards more integrated and automated printing solutions, the significance of reliable and adaptable inkjet nozzles cannot be overstated. With their ongoing evolution, the future of printing technology promises to be exciting and transformative.
Summary of Insights
Throughout this article, we have discussed crucial aspects of inkjet nozzles. We outlined their functionality and categorized them based on their types, addressing thermal and piezoelectric variations. Design considerations such as orifice size and channel length were explored, demonstrating their impact on print performance. Additionally, we examined the operating mechanisms, emphasizing ink ejection processes and flow dynamics.
The performance metrics highlighted included essential parameters that influence print quality, such as droplet size consistency and color accuracy. We identified the application spectrum of inkjet nozzles, touching on their role in commercial and industrial environments. The challenges faced, particularly regarding clogging and maintenance, were also discussed.
Implications for Future Research
As the field of inkjet technology continues to advance, several areas emerge as ripe for further investigation. One crucial implication centers on the exploration of advanced materials. Continued innovation in material science could yield nozzles that offer better durability and enhanced corrosion resistance, further extending their longevity and reliability.
Additionally, the integration of smart technologies into nozzle design opens a wide avenue for research. As printers become more automated, the requirement for real-time performance monitoring and adjustment becomes clear. This could lead to self-cleaning mechanisms or adaptive nozzle designs that respond to various ink viscosities and substrates, significantly reducing operational downtime and enhancing print quality.
In essence, the future of inkjet nozzles appears promising. Ongoing research and development will not only refine existing technologies but also pave the way for innovations that can redefine industry standards and capabilities.