Understanding MEMS Acoustic Sensors: Principles & Applications

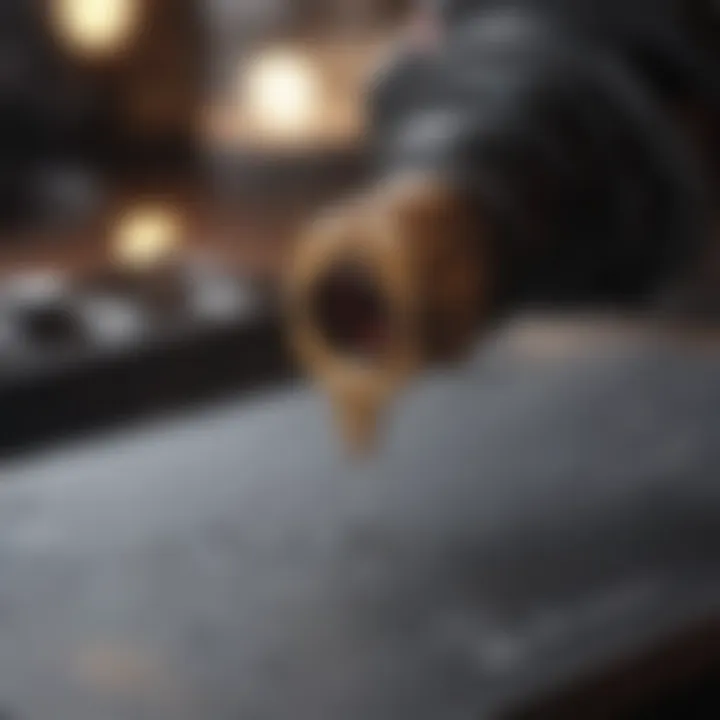
Research Overview
In the domain of Micro-Electro-Mechanical Systems (MEMS), acoustic sensors play a pivotal role. Understanding their operational principles and applications is essential for both researchers and industry experts. This section provides an insightful overview, highlighting key findings and the methodologies adopted in various studies.
Key Findings
- Sensitivity and Accuracy: MEMS acoustic sensors demonstrate high sensitivity and accuracy. Their compact design enables precise sound detection even in complex environments.
- Integration with Devices: These sensors are increasingly integrated into consumer electronics, automotive applications, and healthcare devices. This integration enhances functionality and enables innovative features in products.
- Emerging Applications: From mobile phones to medical diagnostics, the scope of MEMS acoustic sensors extends beyond traditional uses. They are now integral in areas like environmental monitoring and industrial automation.
Study Methodology
To understand the advancements in MEMS acoustic sensors, a review of various methodologies is pertinent. Researchers often employ a combination of:
- Experimental techniques to analyze sensor performance under different conditions.
- Computational modeling to predict sensor behavior and optimize designs.
- Surveys to gather data on industry needs and trends.
Background and Context
A well-rounded grasp of the evolution and current landscape of MEMS acoustic sensors provides essential context. This section covers the historical background and highlights current trends shaping this field.
Historical Background
MEMS technology has roots dating back decades, evolving significantly over time. Initially, these sensors were limited in application and functionality. However, advancements in materials and fabrication techniques have transformed MEMS from niche devices into essential components in numerous fields.
Current Trends in the Field
The MEMS acoustic sensor industry is witnessing rapid innovation driven by:
- Miniaturization: Devices are becoming smaller while enhancing performance.
- Smart Technology: Integration with artificial intelligence is evolving the way sensors analyze sound data.
- Sustainability Focus: There is a growing emphasis on developing eco-friendly materials for sensor production.
"The future of MEMS acoustic sensors is not just about improved sensitivity but also about their contribution to intelligent systems."
Preface to MEMS Acoustic Sensors
MEMS acoustic sensors are instrumental in recognizing and interpreting sound. Their significance stems from advancements in micro-electromechanical systems (MEMS) technology that enable miniaturization and enhanced performance. Acoustic sensors detect sound vibrations and convert them into electrical signals for various applications. In today's fast-paced technological environment, understanding these sensors is increasingly crucial for numerous industries.
Defining MEMS Technology
MEMS technology refers to the integration of mechanical and electrical components at microscopic scales. These systems combine tiny mechanical elements, sensors, actuators, and electronics on a single chip. MEMS devices are compact, scalable, and cost-effective, leading to their adoption in many sectors. In the context of acoustic sensors, MEMS technology facilitates high precision in sound detection.
Acoustic Sensors: An Overview
Acoustic sensors are devices that can detect sound waves and provide a response based on their analysis. They can be categorized based on their operating principle, including capacitive, piezoelectric, and optical sensors. Their deployment ranges across diverse fields such as consumer electronics, healthcare, and industrial applications, enhancing functionality by enabling sound-based features. MEMS acoustic sensors, in particular, are lightweight, compact, and highly sensitive, making them optimal for modern needs.
The Relevance of MEMS in Acoustic Sensing
The integration of MEMS technology in acoustic sensing offers various benefits. It allows for improved sensitivity, better noise performance, and lower power consumption compared to traditional acoustic sensors. These advantages are critical in applications where precision and efficiency are paramount. Furthermore, MEMS acoustic sensors play a vital role in the growing Internet of Things (IoT) ecosystem, enabling smart devices to interpret audio data intelligently. As technology advances, the relevance of MEMS in sound detection continues to expand.
Fundamental Principles of MEMS Acoustic Sensors
Understanding the fundamental principles of MEMS acoustic sensors is crucial for anyone working with or studying this technology. These principles form the backbone of how these sensors operate, offering insight into their applications in various fields. In this section, we delve into the mechanics of sound detection, the key components that make up MEMS acoustic sensors, and the operating principles that govern their functionality.
Mechanics of Sound Detection
Sound detection is essentially the ability to convert sound waves into electrical signals. This process begins with sound waves hitting a diaphragm, which vibrates in response. MEMS acoustic sensors typically utilize a finely crafted diaphragm, pivotal for this conversion. The mechanical structure is sensitive enough to respond to sound waves in a broad frequency range.
The acoustic sensing mechanism involves the detection of pressure variations caused by sound waves. As sound waves travel through the air, they create changes in air pressure, which the diaphragm senses. The detected mechanical movement is transformed into electrical signals, providing a digital representation of the sound.
This ability to accurately translate acoustic signals into usable data is what makes MEMS sensors essential in contemporary applications from consumer electronics to healthcare.
Key Components of MEMS Acoustic Sensors
Understanding the core components of MEMS acoustic sensors helps to appreciate their design and functionality. Each component plays a specific role in ensuring the effectiveness of the sensor.
Microphone Diaphragms
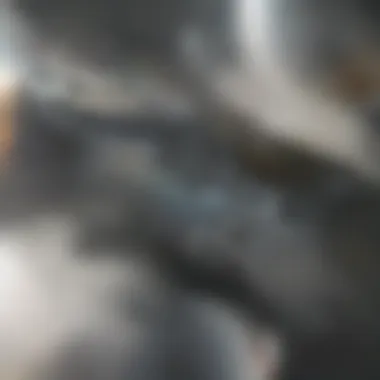
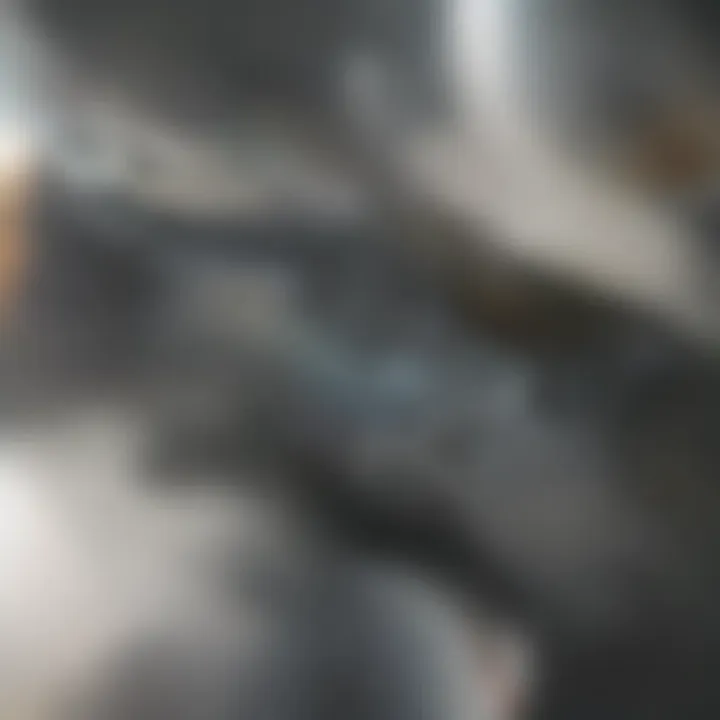
Microphone diaphragms are critical to the operation of MEMS acoustic sensors. These thin membranes are designed to respond to incoming sound waves, creating mechanical vibrations. The key characteristic of diaphragm materials is their ability to efficiently transmit sound and convert it into an electrical signal.
Silicon is often the material of choice due to its favorable acoustic properties and compatibility with microfabrication techniques. These properties render silicon diaphragms beneficial for MEMS applications.
Advantages:
- High sensitivity to sound
- Compatibility with other microfabrication processes
However, their fragility is a noteworthy disadvantage, requiring careful design to avoid damage.
Transducers
Transducers in MEMS acoustic sensors are responsible for converting the mechanical vibrations into electronic signals. They operate on basic principles of piezoelectricity, where piezoelectric materials generate voltage when they are mechanically stressed by sound waves.
Their key characteristic is the ability to provide a fast response time, making them essential for high-frequency sound applications. The choice of transducer significantly impacts the sensor's performance, especially in sensitive environments.
Advantages:
- Fast response time
- High-frequency response
Nonetheless, transducers can face limitations in sensitivity, especially in lower frequency ranges, which must be considered in design.
Signal Processing Units
Signal processing units are imperative for MEMS acoustic sensors as they refine the raw data obtained from the transducers. These units filter, amplify, and digitize the electrical signals, making them suitable for analysis.
A crucial characteristic of effective signal processing units is their ability to minimize noise, ensuring clear and accurate readings. These units often incorporate advanced algorithms for real-time processing, enhancing overall sensor performance.
Advantages:
- Ability to reduce noise interference
- Enhanced accuracy of sound measurements
On the downside, complex algorithms may lead to increased power consumption, which is a significant consideration for battery-powered devices.
Operating Principles of MEMS Sensors
MEMS sensors function using established physical principles, particularly the interplay of mechanical and electrical properties. The operating principles hinge on the relationship between sound wave energy and the responsive elements in the sensor. Once the diaphragm vibrates, the transducer's action generates an electrical signal proportional to the sound pressure level.
In summary, the interplay of mechanical designs and the materials used in MEMS acoustic sensors determines their operating efficiency. Understanding these components and their functions is vital for optimizing sensor designs for specific applications, ultimately leading to advancements in technology.
Design Considerations for MEMS Acoustic Sensors
Designing MEMS acoustic sensors requires careful thought and knowledge about numerous factors that influence their functionality. The design considerations are critical to ensuring that these sensors meet performance requirements while maintaining cost-effectiveness. Key aspects must align with the desired applications. This section explores significant elements, benefits, and considerations in designing MEMS acoustic sensors.
Materials Used in MEMS Fabrication
Selecting appropriate materials is essential in the fabrication of MEMS acoustic sensors. The properties of these materials directly affect the sensors' sensitivity, durability, and overall performance. Common materials include silicon, polymers, and metals.
- Silicon: Silicon is the most widely used material in MEMS technology due to its excellent mechanical properties and compatibility with established microfabrication processes.
- Polymers: These materials offer flexibility and lower weight. They are often used in applications where sensor vibration is desirable.
- Metals: Metals may be employed in components requiring high electrical conductivity.
Each material presents distinct advantages and challenges. Silicon, for instance, might be prone to fracture under stress, while polymers could encounter issues with heat stability. Balancing these aspects is crucial in achieving the desired performance characteristics.
Microfabrication Techniques
Microfabrication techniques play a pivotal role in the creation of MEMS acoustic sensors. These methods determine the precision and quality of the sensors. Standard techniques used in MEMS fabrication include:
- Lithography: This process helps define the structures on the sensor. Photolithography is widely adopted for its ability to create detailed patterns.
- Etching: Both wet and dry etching techniques are employed to remove unwanted material, creating the geometry necessary for device performance.
- Deposition: Techniques such as chemical vapor deposition and sputtering are utilized to apply thin films of materials on substrates, enabling essential component formation.
Every fabrication approach poses specific advantages regarding time and cost. Choosing the right method can enhance production efficiency without sacrificing quality.
Challenges in Design and Fabrication
The design and fabrication of MEMS acoustic sensors face several challenges. Recognizing and addressing these issues is vital for successful development. The major difficulties include:
- Sensitivity and Calibration: Achieving optimal sensitivity while maintaining accuracy can be demanding. Compensating for environmental factors such as temperature can complicate calibration.
- Durability: MEMS components are often small and delicate. Ensuring they can withstand operational stresses without degrading performance is critical.
- Cost Management: While advanced materials and techniques can improve performance, they may also escalate production costs. Finding a balance is essential for market viability.
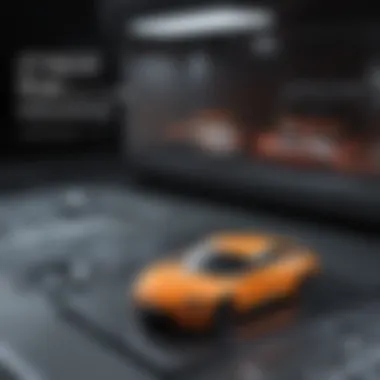
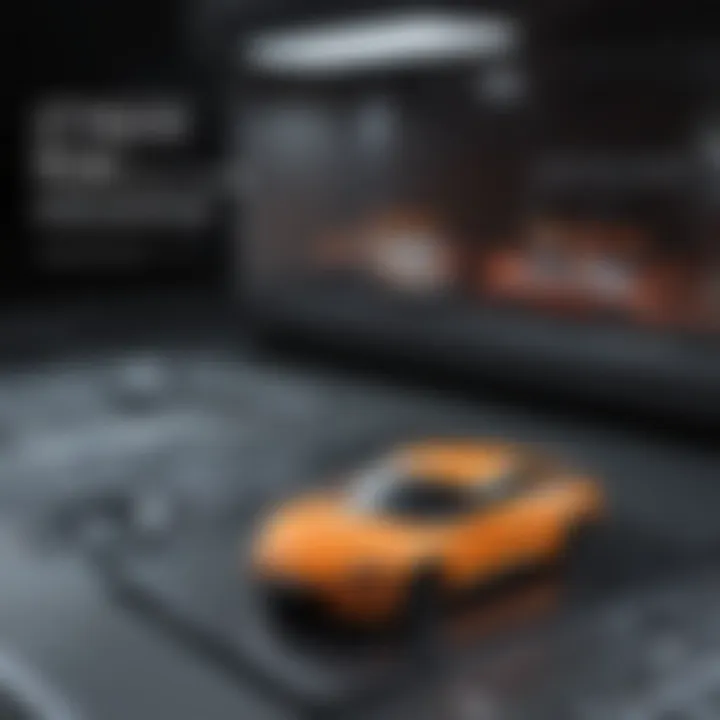
In summary, understanding and addressing these design considerations is paramount for creating effective MEMS acoustic sensors. The ongoing developments in both material science and manufacturing techniques will continue to shape the future of this technology.
"Materials selection, microfabrication techniques, and inherent challenges are critical to the successful design of MEMS acoustic sensors."
By focusing on these considerations, engineers and researchers can enhance the capability and application of MEMS technology in the field of acoustic sensing.
Applications of MEMS Acoustic Sensors
The utility of Micro-Electro-Mechanical Systems (MEMS) acoustic sensors extends across various fields, offering innovative solutions and enhancing existing technologies. In this section, we delve into several key applications, showcasing their importance and the benefits they provide. Understanding the applications aids in appreciating the versatility and impact of MEMS technology.
Consumer Electronics
Smartphones
Smartphones have become central in daily communication and entertainment. MEMS acoustic sensors play a pivotal role in the functionality of smartphones. These sensors facilitate superior voice recognition, noise cancellation, and sound quality enhancement. The compact size of MEMS sensors allows manufacturers to design slimmer devices while maintaining audio performance. Key characteristics, such as high sensitivity and low power consumption, make MEMS acoustic sensors an advantageous technology in smartphones. However, despite their benefits, they can be susceptible to environmental factors such as temperature and humidity, which may impact accuracy.
Headsets
Headsets, particularly those used for gaming and communication, heavily rely on MEMS acoustic sensors. These sensors improve sound clarity and provide a more immersive experience. With features like active noise cancellation, they are favored by users who seek high-quality audio. Their small size and lightweight nature do not compromise sound performance, making them a favored option in modern audio technology. However, high sensitivity also means that background noise can sometimes interfere with audio quality, which is a limitation in noisy environments.
Healthcare Innovations
Medical Diagnostics
In the realm of medical diagnostics, MEMS acoustic sensors are crucial for various applications, including ultrasound imaging. These sensors enhance the precision of diagnostic tools by providing clearer images and facilitating better detection of abnormalities. The ability of MEMS sensors to operate at high frequencies allows for detailed imaging, making them a valuable resource in healthcare settings. However, while they offer enhanced capabilities, the cost and integration of this technology can present challenges in some applications.
Patient Monitoring
MEMS acoustic sensors are also integral to patient monitoring systems. They can track various physiological sounds, such as heart sounds or respiratory noises, providing real-time data to healthcare professionals. This continuous monitoring capability leads to better patient outcomes and timely interventions. The lightweight design and unobtrusive nature of these sensors make them suitable for long-term use. On the downside, false positives may arise due to ambient noise, highlighting the need for further advancements in noise filtering.
Industrial Applications
Noise Monitoring
In industrial settings, MEMS acoustic sensors are employed for noise monitoring. This application is essential for workplace safety, ensuring that noise levels do not exceed safe limits. By continuously monitoring sound levels, companies can mitigate potential health risks for employees, thereby fostering a safer workplace environment. The sensitivity of MEMS sensors allows for accurate detection of specific frequencies, aiding in compliance with noise regulations. However, they are sometimes limited in range, requiring proper placement to ensure coverage.
Production Line Efficiency
Production line efficiency is significantly enhanced by MEMS acoustic sensors. These sensors can detect unusual noises from machinery, indicating potential malfunctions or inefficiencies. By providing timely alerts, MEMS sensors support predictive maintenance strategies, ultimately reducing downtime and maintenance costs. Their integration into industrial systems improves overall productivity. Nevertheless, there may be challenges related to installation and calibration, which can complicate the implementation process.
Environmental Monitoring
Air Quality Measurement
MEMS acoustic sensors are also utilized in air quality measurement. These sensors help in monitoring pollutants and other harmful emissions, essential for public health and environmental protection. Their compact size and ability to provide real-time data make them ideal for both urban and remote locations. Despite their effectiveness, the deployment of such sensors can sometimes be costly, limiting widespread use in developing regions.
Wildlife Research
In wildlife research, MEMS acoustic sensors contribute significantly to understanding animal behavior and habitat. By capturing and analyzing the sounds in natural environments, researchers can gather valuable data on species' interactions and population dynamics. This non-invasive method is a key advantage, as it minimizes disturbance to wildlife. Nonetheless, the range and sensitivity of the sensors can pose challenges in dense habitats, where sound may be obstructed.
Advancements in MEMS Acoustic Sensor Technology
The evolution of MEMS acoustic sensors is marked by significant advancements that enhance their functionality and adaptability. As technology progresses, these sensors are becoming integral to multiple applications, from consumer electronics to industrial systems. Innovations in MEMS technology enable improved sound detection and signal processing capabilities. Consequently, this area has attracted attention from researchers, developers, and businesses alike.
Integration with IoT Devices
The integration of MEMS acoustic sensors with Internet of Things (IoT) devices represents a pivotal advancement in this field. This fusion allows for real-time sound monitoring and interaction, which enhances the overall user experience. MEMS sensors embedded in IoT systems can capture ambient sounds and process them efficiently.
Benefits include:
- Enhanced Connectivity: MEMS sensors in IoT devices facilitate greater connectivity and data exchange.
- Real-time Processing: The technology allows for immediate response to audio stimuli, supporting applications in smart homes and health monitoring.
- Reduced Power Consumption: MEMS sensors typically consume less power, which is critical for battery-operated devices.
Moreover, as devices become more interconnected, the demand for capable acoustic sensors will rise. Recent developments allow these sensors to become smaller, yet more effective, catering to the compact designs of modern devices.
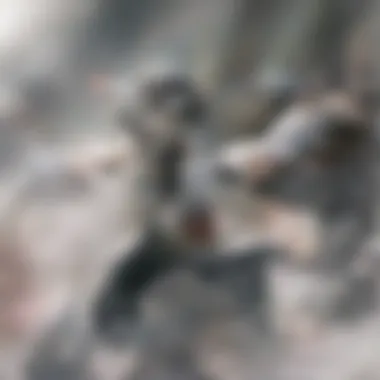
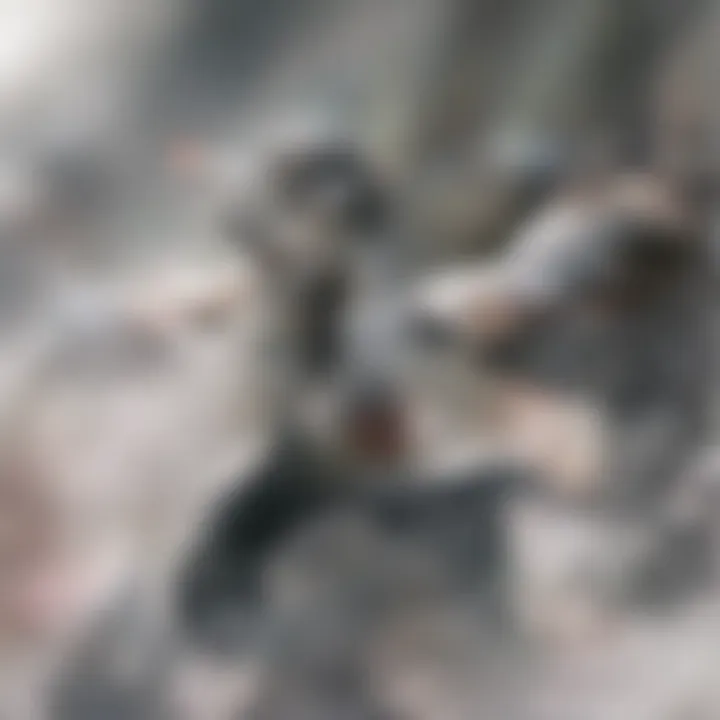
Innovative Signal Processing Techniques
Innovative signal processing techniques play a crucial role in enhancing the capabilities of MEMS acoustic sensors. These techniques improve the signal-to-noise ratio and facilitate better sound analysis.
Key aspects include:
- Machine Learning Applications: The application of machine learning algorithms enables MEMS sensors to analyze sound patterns more accurately. This leads to better classification of audio signals and improved performance in signal interpretation.
- Adaptive Filtering: This method helps to minimize background noise, allowing for clearer audio capture. It adjusts parameters in real-time, depending on surrounding conditions.
- Digital Signal Processing (DSP): Integration of DSP with MEMS technology can drastically enhance the functionality of acoustic sensors in applications like voice recognition and acoustic imaging.
"Continuous advancements in signal processing techniques are setting the stage for highly effective MEMS acoustic sensors that meet the demands of various complex applications."
As a result of these enhancements, MEMS acoustic sensors are now capable of performing tasks that were previously unfeasible, thus expanding their market potential and application scope. This area of research continues to evolve with the promise of even more sophisticated solutions for sound detection and analysis.
Challenges Facing MEMS Acoustic Sensors
The development and deployment of MEMS acoustic sensors involve several hurdles that impact their effectiveness and usability. Understanding these challenges is essential, as they can have direct implications on product performance and application suitability. High sensitivity and accuracy are crucial for many applications. However, various elements can adversely affect these parameters. Furthermore, the durability and longevity of these sensors must be considered to ensure they meet the demands of their environments.
Sensitivity and Accuracy Issues
MEMS acoustic sensors rely on precise sound detection capabilities. However, achieving high sensitivity is not straightforward. Environmental factors such as temperature fluctuations and humidity can influence sensitivity levels. It can lead to inaccuracies in sound detection and measurement. Also, external noise can interfere with the sensor's ability to isolate and process sounds effectively.
Another important factor is the calibration of these sensors. Proper calibration is necessary to maintain a balance between sensitivity and noise levels. A sensor that is too sensitive may pick up unwanted background noise, while a less sensitive sensor may fail to detect softer sounds.
The advancements in signal processing methods have helped improve sensor performance. Innovative algorithms can help mitigate the effects of noise, enhancing overall accuracy. Yet, these solutions are not without challenges. They require sophisticated hardware and computing power, which can increase production costs.
Durability and Longevity Concerns
Durability is a pivotal concern in the lifecycle of MEMS acoustic sensors. These sensors often operate in environments that expose them to physical stress, moisture, and temperature extremes. This exposure can lead to degradation of their performance over time.
For instance, MEMS sensors used in industrial applications may encounter vibrations and shocks that can negatively affect their internal structures. Such effects can compromise their reliability during operation. The materials used in manufacturing these sensors must be chosen carefully to enhance their resilience.
Longevity is also a critical aspect, especially for sensors deployed in inaccessible areas. If a sensor fails prematurely, it could lead to significant downtime or costly repairs. Thus, manufacturers need to invest in research to improve material properties and protective coatings. As the demand for MEMS acoustic sensors continues to grow across various sectors, addressing these durability and longevity issues will be vital for ensuring sustained performance and viability in the marketplace.
Future Directions for MEMS Acoustic Sensors
The future directions of MEMS acoustic sensors present an exciting arena for exploration and innovation. As this technology evolves, it has the potential to enhance various fields through improved acoustic sensing capabilities. Understanding these future prospective areas is crucial for researchers and industry professionals aiming to leverage MEMS technology effectively. The advancements depend on several elements, including technological innovations, market needs, and collaborations with other technologies.
In the context of MEMS acoustic sensors, focusing on research and development within specific areas will lead to significant benefits. These advancements can create sensors with higher sensitivity, broader frequency ranges, and lower power consumption. Enhancing these features is essential for applications such as healthcare, industrial monitoring, and environmental assessment, where precision is paramount.
Potential Research Areas
- Miniaturization: Continued research on microfabrication techniques can lead to even smaller MEMS sensors that maintain or increase performance. Advanced techniques like 3D printing in micro-scale can also play a role in creating complex structures that traditional methods cannot achieve.
- Smart Materials: Investigating the use of piezoelectric and magnetostrictive materials can improve the performance of MEMS sensors. These materials can provide better sensitivity and broader operational ranges.
- Signal Processing Algorithms: Developing robust algorithms for better signal processing will enhance the accuracy of data interpretation. This is particularly important in applications requiring real-time data analysis and noise reduction.
- Wireless Communication: Researching methods to integrate wireless communication into MEMS sensors can result in smarter sensor systems that communicate efficiently over larger distances. This integration is vital for IoT applications, where data transfer is critical.
- User-Centric Designs: Studying user interactions and needs can drive design innovations. Sensors that are more adaptive to user environments can open new applications, particularly in consumer electronics.
- Sustainability: Exploring eco-friendly materials and processes in MEMS fabrication is crucial. Sustainable practices can reduce environmental impact while enhancing the appeal of these technologies to more consumers and businesses.
Industry Trends and Predictions
The MEMS acoustic sensor industry is poised to experience notable growth driven by several trends. As technology continues to advance, the demand for more precise and versatile sensors is increasing.
- Rise in IoT Devices: The proliferation of Internet of Things (IoT) devices is a major trend influencing the demand for MEMS acoustic sensors. The need for real-time monitoring and communication in smart homes and cities is accelerating the development of these sensors.
- Healthcare Growth: As healthcare technology advances, MEMS sensors are expected to play a crucial role in medical diagnostics and patient monitoring. The ability to conduct non-invasive assessments will become increasingly valuable.
- Integration with AI: Machine learning and artificial intelligence (AI) integration into signal processing will provide potentially game-changing enhancements in data interpretation. The pairing of AI with MEMS sensors can generate actionable insights that are currently not possible.
- Expansion Across Industries: The application of MEMS sensors is not limited to consumer electronics. Industrial automation, environmental monitoring, and automotive sectors are all looking to incorporate these sensors into their operations for enhanced efficiency and accuracy.
"The future of MEMS acoustic sensors rests on innovation that addresses user needs while maintaining performance and sustainability."
In summary, the future of MEMS acoustic sensors is bright and full of opportunities. The continuous advancement in technology and understanding of applications will drive this field forward, creating more precise, efficient, and versatile sensing solutions.
The End
The conclusion serves as a vital summary of the entire article, encapsulating the key insights around MEMS acoustic sensors. This section distills the complex information presented previously, reinforcing the significance of MICROSENSORS in various fields such as healthcare, consumer electronics, and environmental monitoring. A thorough understanding of these sensors is crucial for anyone involved in or studying modern sensing technologies.
The importance of MEMS acoustic sensors cannot be overstated. They offer enhanced sensitivity and reliability compared to traditional acoustic sensors. As the demand for high-performance sound detection continues to grow, MEMS technology evolves to meet these needs efficiently. Their small size, coupled with the ability to integrate with other devices, makes them essential in IoT applications and wearables.
Key benefits of MEMS acoustic sensors include:
- Small Form Factor: Their compact design enables deployment in a wide array of devices without consuming significant space.
- Cost-Effectiveness: The mass production of MEMS sensors leads to lower cost options for manufacturers and consumers alike.
- Versatility: These sensors can be used across a multitude of applications, adapting to different needs and requirements.
However, the discussion does not conclude with just the benefits. It is essential to acknowledge the challenges faced by this technology as it matures. Though advancements are steady, addressing concerns related to sensitivity, environmental resilience, and manufacturing scalability remains important.
By summarizing the exploration of MEMS acoustic sensors, this article aims to inspire further research and innovation in the field. As we look into the future, a clear trajectory emerges for MEMS technology. Embracing these innovations will not only enhance current applications but also open avenues for new opportunities in sound detection and analysis.
As a final note, understanding the intricacies of MEMS acoustic sensors is crucial for students, researchers, educators, and professionals alike, ensuring they are well equipped to engage with and contribute to this evolving landscape.
"In the realm of technology, understanding is the first step toward innovation."
For further exploration on MEMS and acoustic detection technologies, consider resources like Wikipedia or Britannica for a more detailed view.